Power & Energy Management Industry Forum: Modernization without interruption
"The hardest part of the project was interfacing to the older systems to continue to generate power during each phase." Andy Dieball of EthosEnergy oversaw the stem-to-stern modernization of power plant controls for Tri-State Generation & Transmission—all without interrupting electricity production.
If your power generation and transmission facilities are where wind power is on the rise, you know how important it is to be flexible, and ready to ramp. Such was the case at Tri-State Generation and Transmission (G&T), which has 3.8 GW of capacity over a four-state region, with 1,600 employees and $1.4 billion annual revenue. It’s also a wholesale supplier to 43 electric co-ops. “The region receives significant production from wind turbines,” said Andy Dieball, vice president of sales, EthosEnergy. “Since the wind can fluctuate, the key for Tri-State is for the power generation to be highly available, and quick to ramp.”
EthosEnergy is an independent turbomachinery service provider. Dieball's group is focused on turbomachinery controls, the brains of gas and steam turbines. The group is essentially a Rockwell Automation system integrator for turbomachinery control within a large company, with other groups focusing on the mechanical aspects. The company does about $1 billion in annual revenue with 4,500 employees, and the group has completed over 900 turbomachinery control system upgrades.
EthosEnergy provided services to upgrade Tri-State G&T’s JM Shafer Generating Station, a 5x2 combined-cycle plant in Fort Lupton, Colo., a small army community north of Denver. Dieball discussed the challenges of upgrading an obsolete control system, and how automation was used to give the plant a competitive advantage in his presentation to attendees of the Power and Energy Management Industry Forum at Automation Fair this week in Houston.
"The plant uses five GE LM6000-PA gas turbines providing a total of almost 300 MW output,” Dieball said. Based on a GE flight engine, the turbines are relatively small, but are highly flexible and fast. “These nimble gas turbines can reach full load in eight minutes, and exhaust through two Nooter/Eriksen heat-recovery steam generators (HRSGs) to feed two ABB STAL steam turbines."
Obsolete control structure
"The overall plant control system at Tri-State was a Bailey Infi90, obsolete for many years," said Dieball. "The gas turbines were run using Woodward Netcon gas turbine controllers. The steam turbines used Unitrol controllers. There were also several Rockwell PLC-5 controllers for HRSG duct burners, with Emerson Ovation for plant HMI. It was quite a patchwork of control systems."
All these different major control systems presented challenges, and the plant was approaching 20 years in operation with existing control systems no longer supported by the OEMs. "The obsolescence of plant systems became a major source of risk," said Dieball. "Tri-State's tolerance for risk was very low, so it desired to eliminate risk and to adopt a common control system platform."
The plant owner also wanted to continue to produce power during installation. "The plant couldn't be shut down for 60 days," said Dieball. "This made things more complex, with new systems needing to communicate with old systems."
Detailed design, tight schedule
EthosEnergy used a thin client concept for HMI, and included a Stratus ftServer to do all the heavy lifting for the FactoryTalk SE HMIs. FactoryTalk Historian and SQL server, and a redundant network rounded out control room, with 16 displays running as thin clients.
The balance of the plant was upgraded from Bailey Infi90 I/O to redundant ControlLogix hardware from Rockwell Automation. Using prefabricated I/O cables simplified installation and commissioning, as de-termination and re-termination of field wiring was not required.
"The first upgrade project was the gas turbine control," said Dieball. "It was the most difficult task, as the turbines are very quick. They could run away or stall very quickly. The system uses a ControlLogix controller mounted in the turbine cabinet with a local HMI, power monitor and auto-synchronizer."
Flex I/O was mounted in an on-engine control cabinet used for field wiring. "It communicates with the controller via redundant ControlNet," said Dieball. "This I/O connects to servo position controllers used to set the variable geometry, fuel valve and steam valve. It also provides an interface to existing voltage regulator, generator protection, vibration monitoring, fire and gas detection and engine instrumentation."
The steam turbine control had similar hardware to the gas turbine control, but was much simpler. Most of the steam turbine control was mounted in the control room.
"Scheduling was where the complexity of the project came," said Dieball. "Tri-State wanted to minimize downtime during installation, so a phased approach was implemented to ensure power generation during the project. There were four phases: gas turbine, steam turbine, HRSG control upgrade, and balance-of-plant control system plus plant HMI."
In the first three phases, the new control system needed to communicate to the existing balance-of-plant controller and plant HMI. "The hardest part of the project was interfacing to the older systems to continue to generate power during each phase," said Dieball.
Why Rockwell and EthosEnergy
"EthosEnergy demonstrated to us that they have a turnkey solution for our gas turbine packages," said Richard Rhoads, plant manager at JM Shafer Station. “They adopted the Rockwell Automation platform, with its massive installed base that was proven in use and would be supported for longer than the life of our plant assets. It gave us the confidence that they would be able to deploy their solution in a timely fashion and minimize our risk. It was clear to us that they had a process that would accomplish that.”
EthosEnergy completed the project on time while meeting Tri-State requirements for continuous power generation. The new control system improved the plant ramp rates from 20 MW/minute to 30 MW/ minute, which enabled Tri-State to take advantage of rapidly changing market demand driven by wind generation.
"A lesson learned is that the ftServer required extra work related to network bandwidth and memory allocation," said Dieball. "It’s important to pay attention to memory consumption when using a thin-client HMI system, and Rockwell Automation has many resources to help deal with it. Their software tools also made it easy to provide data, and to monitor the network in real time to detect breaches or unauthorized access, which helped manage NERC compliance."
Imagine the training manual for a 300 MW power plant run by five different manufacturers of controllers, suggested Dieball. "I wouldn't want to write that manual or be a technician responsible for keeping the plant running," he said. "Upgrading to a single-manufacturer control system by Rockwell Automation was a huge advantage in terms of training."
Tri-State specifically commented on the RSLogix 5000 environment, the user-friendly tools, and the large library of function blocks available to them. "With the training we provided, they were able to tackle any mini-projects that came up without outside help, as well as system changes when needed," said Dieball.
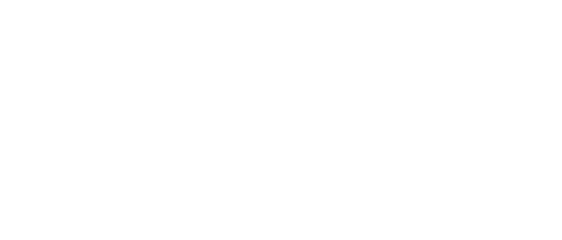
Leaders relevant to this article: