How can we harness the strengths of Millennials to further our profession?
Things got even better when he took me to one of the office windows a few days later and pointed at a group of very tall columns. He said, “That’s the high octane unit, and it will be yours for the next couple of years or so. You will transfer control of those columns to a DCS, and implement advanced controls on them to improve their safety and efficiency.” He went on to tell me that I would have all the resources of the company available to me, but I was the lead and had to decide what resources I needed and when. My jaw dropped in awe of what I was being told to do, but also due to the confidence the company had in me. All I can say is, at the end of those two years, I’d learned so much not only about control, but also how to manage and work with people.
I wonder if we have the same level of confidence in today’s Millennials, and do we give them enough support? Or is it that we’ve run down the support systems so much these days that the support infrastructure is in their mobile device of choice?
The advances in control technology that happened in the late 1970s and all through the 1980s attracted many young engineers to the profession, but the advent of the Internet and other technologies has turned their attention away from manufacturing, and we’re still feeling the effects today. At its peak in the mid 1980s, the control team at the petrochemical plant reached about 15 people. Today, I wonder if most major manufacturers have 15 control engineers in the whole of Europe.
The arrival of new technologies over the past decade has given young engineers a huge career choice, and those choosing a career in manufacturing seem to be few and far between. So where are those “columns,” those innovative technologies and challenges to bring them back to the automation industry? The clock is ticking, and we need them to join our industry sooner rather than later, while there is expertise to train them. But how do we do that and play to the strengths of both generations?
We hear about the Millennial generation wanting it all and wanting it now, but they feel they can get it all now through their mobile device, and in addition, they can communicate with their peers any time of the day or night.
Are the Millennials any different than we were? They have the same desires but more tools at their fingertips, and quite frankly more knowledge—they are digital natives. How can we harness their strengths and ours to ensure the profession goes forward strongly?
Also read: Automation companies prepare younger generations to replace retiring employees
I believe we’re back where I was in the late 1970s, at the start of a new technological revolution. We have mobile devices, wearable technology, the Internet of Things, wireless, cybersecurity, big data, apps and so on. These will revolutionize the process industries in the hands of the Millennial generation.
[pullquote]Standards are now playing a bigger part than when I was younger. Every large company had its own standards back then. These days, engineers rely on standards committees as their extended community, and again, having access to these standards via today’s technology makes them even stronger than before. It’s interesting to note that an iPhone is the same and has many of the same apps no matter where in the world you use it. Let’s encourage the younger generation to join the standards committees and freshen them up. ISA101, the standard for Human Machine Interfaces, was just released, but we are starting a new working group to investigate the impact of mobile technology on HMI design.
Our job is to sell the profession to the Millennials. Large companies need to attract them by offering strong careers and having the faith in them that the petrochemical company had in me all those years ago. I challenge my peers to find every opportunity to explain our jobs to young engineers, mentor them, and encourage them to look at a career in automation. Rather than taking my word for it, I discussed this with some Millennial friends, relatives and colleagues and found their views insightful.
On recruiting and retaining Millennials: “Everyone wants to attract the best talent. But none of us are going to be able to compete with Facebook, Google, Microsoft and NASA, just to name a few. But people who might want to be automation engineers are likely to be more pragmatic than into a sexy name on the door.
“Having high pay and benefits is very important to hiring talent, but I presume that’s already been tried. I actually like the way researchers tend to recruit talent, through internships. I recommend cultivating the attention of a professor that’s visible in a relevant field, and offer internships to that professor’s students. The idea is to cultivate a relationship that is mutually beneficial—the professor gets funding to work on areas that interest him, and the student gets exposure to problems that are relevant to automation. Even if there are no universities nearby, students may travel far for an interesting (paid) summer job. Later, when the student graduates, you might get first shot at their attention. The best method is to hire many interns at once, who will work together and who are interested in automation together. If your company has more money than talent, this method seems to work best. In addition to a good reputation, creating your own cohort of interns will help boost the environment in the workplace and create excitement.
“I’m familiar with a lot of software startups, and they all find it easy to recruit young, talented people. Part of the solution is the cohort situation I already mentioned. Exciting startups also offer paid happy hours, free lunches and other amenities on-site. Their young people are led by a charismatic and experienced professional, who makes them excited to be at their job. Young people are always looking for the next job. They’re aware no one tends to keep jobs for very long these days, so having a way to quickly promote young people so they have some real responsibility is very important to retaining talent. If the way forward is clogged by incipient retirees, that’s going to be a problem for retention.”
On technology: “I think the adoption of mobile devices across our industry is really underwhelming. The amount of time I spend on my phone or tablet off the clock hugely overshadows the time I spend in front of a computer. I understand that there are certain tasks that are more suitable for a computer, but mobile devices are such an important complement to the desktop experience. I see some wearable concepts (like Apple Watch) that our competitors put out, and even if the idea might not be totally thought out, it’s really refreshing that they’re looking forward with technology. I think we need more of that. I understand that it’s a difficult balance because our industry has so much at stake in terms of reliability and safety, but I really think that kind of forward thinking appeals to the younger generation.
“Today’s technology can greatly help in this job. It can be useful in demonstrating ideas and concepts during meetings, but it can also help in continuing work while users are on the move such as during commuting.”
On aspirations and rewards: “Over the next three to four years I expect to be in a group of engineers in a supported role, but after this initial period, I’ll be responsible for my own tasks. In five to 10 years, I see myself in the same industry but not particularly with the same company. I hope to be taking on a managerial role within this time period.
“Money is definitely a big part of having a rewarding job for me, but being given responsibility and a challenging job role helps in feeling worthwhile and that I’m a useful part of the company I work for. Also, I feel that as a younger engineer, receiving feedback on my work and recognition when I have performed well is very valuable to help in my progression.”
On the older generation: “I feel that older engineers are a useful asset and can be very helpful. While on my intern year working for a major engine manufacturer, a talk with my manager (older engineer) could halve the amount of time required when troubleshooting problems.
“One thing I try to do is give presentations at universities and engage younger engineers through the institutions I belong to such as ISA, U.K. Institution of Chemical Engineers (IChemE) and the Institute for Measurement and Control.
“Our industry portrays an image a little like going to your grandparents’ house—old, but stable and not too exciting. But grandparents can be cool too. We need to freshen up the image of our industry, and sell it to the young engineers in ways that Silicon Valley learned long ago.”
What other things can we do? Please write to me at [email protected] and I will compile your responses into a follow-up article. We need to keep this item front and center because the clock is ticking, and even the youngest Baby Boomers won’t be in the workforce much longer.
Homepage image courtesy of Stockimages at FreeDigitalPhotos.net
Latest from Home
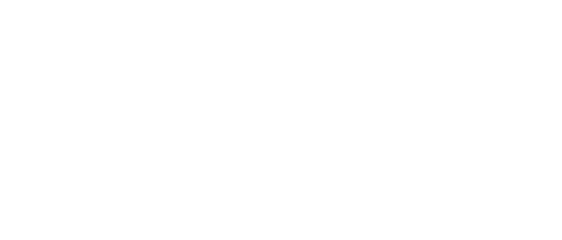
Leaders relevant to this article: