I have worked in the automation industry since 1969. My very first job was as a control engineer for a chemical company, then for a contractor, and then I joined the supplier side of the business and got into management. I've had the benefit of seeing the control profession from three different perspectives. These 46-plus years have given me a deep appreciation for what control engineers do and the value they bring to their organizations.
So why are control engineers often the most unknown and underappreciated engineers in their organizations? I have often called our profession a noble profession. Our work demands the broadest skill set of any engineering discipline—it requires knowledge of chemical processes, mechanical, electrical, electronics, software, networks and IT. In a typical project, the total automation amounts to less than 10% of the total cost, yet it has the most impact on the performance of the process. All the best equipment and process designs are rendered helpless if the controls don't work. But when control is done brilliantly, the operation sings.
Build Better STEM Cells
So why does our work get so little appreciation? Let's look at some of the reasons and also what we can do about it. The awareness challenge for the control engineering profession begins at the university level. There are very few engineering schools that offer undergraduate degrees that relate directly to control—most of us study something else first and migrate to the profession.
Control and System Science had their heyday in the days of the space program. The launch of Sputnik in the late 1950s sent a jolt through engineering schools and perhaps was the last truly significant boost for the concept of science, technology, engineering and math (STEM). The surge in engineers certainly benefited the control profession, but these baby boomers have moved on. The world needs control engineers, and we all can do something to build awareness at the university level. If there is an engineering council at your alma mater, join it and make your voice heard. Get your company or organization to sponsor contests for budding engineers. Encourage your company to provide scholarship funding. We need to get people into engineering and specifically into the control profession.
Most universities have chemical engineering pilot labs. Unfortunately, the state of the controls and instrumentation in these labs is pretty bad. I recently visited one of these labs where the students were using nothing more than rotameters to measure flow! Suppliers should donate the latest equipment to these universities. End-user and contractor engineers should volunteer their time to set up and maintain these labs. We need to expose today's engineering students to control. Stated more simply, the students need to have fun with our toys.
IoT Is Cool and Automation Is IoT
Students today are drawn to the technologies of the Internet, bio-medical engineering, and software. By comparison, process control or factory automation looks pretty rust-belt and old-school. We can bring our profession to life if we change the way we describe it. You hear a lot of talk these days about the Internet of Things. If you stop to think about it, control engineers were connecting up the Internet of Things long before there was an Internet. The venerable twisted pair was the first Internet. Distributed digital control came out in the 1970s and smart field instruments arrived in the 1980s. To paraphrase a country music song, we were doing the Internet of Things before the Internet of Things was cool. The rest of the world has finally caught up with us! What could be more fun for a young engineer than connecting the Internet of Things in process and discrete manufacturing applications?
Tout ROI
As a profession, we are not that great at proving our value, even inside our own organizations. A goodly number of us come to work every day with a not very lofty goal—keep the plant running. This mentality dooms us to only one time to be visible—when control shuts the plant down. All of us need to get on the stump to raise awareness of the value we bring. To raise awareness, we need to translate what we do into tangible benefits and demonstrate those benefits. This means quantifying the results. Get with someone from your accounting group and learn how the company makes decisions. Do your homework on the economic value your work creates. This is not about bits and bytes—it is about running the plant with lower energy, lower emissions, greater safety and more throughput. This is the value we deliver, and it is huge.
[pullquote]I once met with the head of one of the largest refineries in the world. After looking at his watch and scowling at me, his first words were, “I think all automation projects have zero ROI.” While this may be extreme, my experience tells me that there are more of these kinds of people in management than there are true believers in control. Whose fault is that? Ours. We deliver huge business value, but we stay in the comfort zone of technology and don't venture into the business results of what we do.
The control system and its associated field devices are the eyes, ears and brains of the plant. I was personally associated with a project a few years ago that provided ample proof of the value. There were two identical plants on the same site, both of which had some pretty ancient controls and instruments. The project schedule called for modernizing one plant first. Only the controls and instruments were changed. For a year or two, old and new systems were running side by side. The new controls delivered a double-digit increase in output and cut down the number of unplanned shutdowns by 50%.
Use Today's Best Tools
We all need to drive innovation. Our industry is justifiably conservative. However, sometimes that conservatism is way too extreme. I sometimes chuckle when I read technology futurists' predictions for control and automation. Sadly, the vast majority of facilities are not even using today's technology. Once again, that is our fault. The challenge for control engineers is that the perceived risk of “rip and replace” usually kills most projects. You don't need to do a big bang to make a lot of noise. For example, wireless technology enables us to economically install more measurements to get a better handle on performance. Predictive intelligence is in every smart instrument—hardly anyone uses it. Rotating equipment is the biggest source of unplanned shutdowns in most plants. Predictive intelligence can be installed around this equipment. Don't withdraw into a conservative shell. Be the outspoken advocate of the benefits and demonstrate them through a series of small successes.
A few years ago, I was honored to be inducted into the Hall of Fame. My favorite part of the Hall of Fame induction ceremony is the acceptance speeches. It is a true delight to hear these engineers talk about their careers. Their pride is obvious. Every day, across the globe, control engineers come to work with the goal of making something better and safer. They harness technology and combine it with no-nonsense engineering. It is indeed a noble profession.
Latest from Home
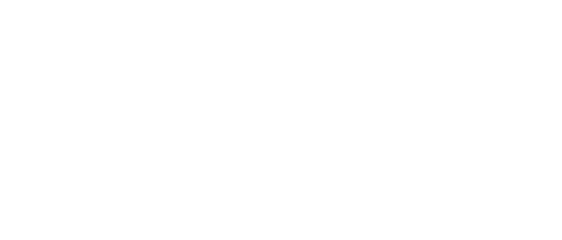
Leaders relevant to this article: