Keith Nosbusch is bullish on the potential for connectivity to transform industry. For the first time in his decade-long tenure as chairman and CEO of Rockwell Automation, he believes the automation giant's vision of The Connected Enterprise can be a game-changer, transforming the industrial landscape. "These are exciting times," said Nosbusch, who set the stage for the company's Automation Fair event this week in Anaheim, California, in his keynote address to assembled media. "The value at stake is enormous."
Automation Fair, the company's flagship customer event, is focused on solving real-world problems and adding tangible value for industry, explained Nosbusch. "What's driving our customers today?" he asked. "We're finding these four value drivers: faster time to market, lower total cost of ownership, improved asset utilization and better enterprise risk management. The Connected Enterprise is focused on rapid value creation across all four drivers."
With 22,500 employees in more than 80 countries and almost $7 billion in 2014 fiscal sales,
Rockwell Automation is the largest company in the world focused solely on industrial automation and integrated control, said Nosbusch. "We have a long history—111 years—of servicing customers with technology innovation, deep domain expertise and a culture of integrity and corporate responsibility. The progress we're making in realizing The Connected Enterprise now is transformational."
"The value at stake is enormous." Keith Nosbusch, chairman and CEO of Rockwell Automation, believes the time is ripe to realize the long-promised potential of the Connected Enterprise.
Secure networks and contextualization of the data helps to create information that can be shared. This results in an enterprise that can be quantified, said Nosbusch. "We're at an inflection point for The Connected Enterprise," he explained. "It's enabled by integrated control and information. To realize The Connected Enterprise, there must be a convergence of IT and OT. Operations technology (OT) is the world of industrial equipment, such as machines, controllers, sensors and actuators. Information technology (IT) includes ERP, finance, HR, logistics, quality and CRM. Critical to the OT side is real-time data that drives control and safety. It's typically acted upon in milliseconds or microseconds."Because many operations need to run continuously 24/7 and cannot shut down for software updates, IT might have a different determination of what's critical. But both IT and OT are critical for the success of an industrial enterprise. And in the past, most approaches to convergence have been expensive and unscalable, said Nosbusch.
"We've made tremendous progress in bringing forward an IT-OT solution through our partnership with Cisco," he said. "This flatter, more open approach delivers a level that wasn't possible with the previous generation of technology, and it enables IT and OT convergence."
Nosbusch noted several major industry trends that help to identify a great opportunity. According to a Rockwell Automation survey conducted with Industry Week, nearly three-fourths of U.S. plants are more than 20 years old, and less than 14% of these manufacturers have tied their machines to the enterprise network, he reported. Further, manufacturing has generated 2 exabytes of big data, according to a McKinsey report. Plants are experiencing losses of $20 billion annually due to unscheduled downtime, and updating obsolescent automation systems will cost industry $65 billion, according to studies from ARC Advisory Group.
These opportunities are perfect scenarios for optimization of production through The Connected Enterprise via the convergence of IT and OT, and it's enhanced by modern trends such as the Internet of Things. "Rockwell Automation and our partners are applying our industrial expertise to realize The Connected Enterprise through processes and business models," explained Nosbusch. "It will unleash untapped value. Modern technologies are helping us to connect smart assets to the rest of the enterprise via a secure
IP-based infrastructure, enhanced by the industrial environment. The data from these smart assets will be processed and analyzed and delivered at the point of most value. That could be at the controller, at the edge or in the cloud."
Rockwell Automation delivers The Connected Enterprise through three core platforms—integrated architecture, intelligent motor control, and solutions and services. "The integrated architecture is highly scalable and capable of differentiating high-performance machines," said Nosbusch. "For intelligent motor control, our entire lineup is enabled by the integrated architecture to speed performance. Solutions and services include consultative design, support and services. We complement and extend these platforms with our partner network."
All integrated control and information start with smart assets, both in the field and in the plant. "In many heavy industries, remote monitoring is enabled by smart assets in the field," explained Nosbusch. "Smart assets in the plant have more computing power available than distributed assets. But the distinctions between smart assets in the field and in the plant are not always black and white."
Distributed smart assets in the field, such as oil pump jacks, tank farms and mine-based conveyors need to be placed where the natural resources are, sometimes inhospitable environments, explained Nosbusch. "Today through technology such as cellular and satellite communications, it's much more cost-effective to enable the management of these assets," he said. "Most remote assets' applications should involve a man in the loop to create real-world insights and decisions for what action to take."
An example of remote asset management is LNG refueling stations, which are forecasted to increase by 60% over the next few years. "Rockwell Automation is working with Chart Industries and Shell on the refueling stations," said Nosbusch. "We are deploying cloud-based solutions for asset management and site performance. Energy markets are expanding, and energy companies are very sensitive to the environment. We're deploying more smart assets to remote locations and optimizing them to perform. The objective of The Connected Enterprise in the digital oil field, for example, is to speed up all decision-making processes and enable innovation in uptime and efficiency. Where should the next well be drilled? How do I get the right personnel or repair parts to support an operation or maintenance activity?"
Plant-wide integrated control and assets include machines, lines, process equipment and controllers, which all generate a significant amount of data. "At one of the world's largest food processors, machines from multiple manufacturers are being connected with a standardized set of functionality," explained Nosbusch. "All machine communications are in real time over the open IP-based infrastructure using CIP, the Common Industrial Protocol. Data centers are in each plant, and the information is shared via the cloud to allow visibility. When complete, a network of over 100 plants around the world will be the core of this manufacturer's Connected Enterprise."
Latest from Home
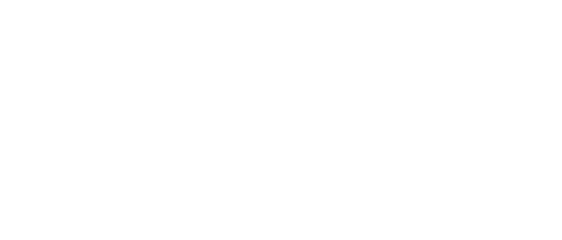
Leaders relevant to this article: