By Kristen Barbour, Product Marketing Manager; Pepperl+Fuchs (FDT Member Company)
Many automation projects use digital fieldbus technology as the preferred platform for control and instrumentation. Because of this, most experienced fieldbus users and installation contractors would agree that installation and commissioning practices have a significant influence on the long-term quality of fieldbus communications. Today, users can embrace advancements to installation and commissioning practices with FDT Technology.
A well-executed installation is a valuable tool in protecting plant operations. Over time, any number of negative factors can compound and degrade communication signal quality, resulting in network instabilities and unplanned shutdowns. To keep your facility proactive to minimize problems in the field, having a healthy physical layer to transmit this information is critical. Physical-layer equipment with FDT Technology is available and provides leading-edge diagnostic features. These benefits allow transition to a fully automated network test and reporting program, reducing time and cost for construction and commissioning by optimizing the test process and baseline report generation resulting in a large reduction in capital expenditures. This allows today's installations to rise to the demands of a competitive marketplace and achieve online status faster with the goal to keep projects moving and on schedule.
Traditionally, determining the quality of the fieldbus communication signal has required a high degree of technical knowledge and sophisticated electronic equipment. Loop check procedures, includingd checking cable continuity, testing resistance and capacitance, analyzing signal level and noise, etc., were time-consuming and labor-intensive manual endeavors. FDT has changed all that, and can reduce the start-up node commission time by up to 80% when compared with traditional analog installations. "This is a big change in maintenance culture," says Seah Ooi Kiat, head of instrument engineering in the manufacturing department at CSPC, a joint venture between China National Offshore Oil Corporation and Shell Petrochemicals Co. Ltd. in Nanhai in southern China. "In the past, maintenance actions were often taken too late, usually after problems had occurred and been recognized by plant operators. Now, using the latest technology, the maintenance technician can check, on a daily basis, those devices that have issued a warning of a potential problem and decide on corrective action before any potential failure occurs."
One of the primary reasons FDT Technology has become so popular in the marketplace for process and factory installs is the means to faster commissioning resulting in a reduction in start-up costs and maintenance procedures. This, in turn, makes the facility more effective for plant personnel to maintain plant assets. Operational data validating life cycle benefits at DOW Tarragona, were recorded during revamping of its cracker. The facility experienced a 40% reduction in commissioning time, and an 80% time reduction for last-minute modifications and resolution of typical instrument start-up problems. With FDT's diagnostic DTMs available for components, users of the technology reap the benefits of choosing best-in-class devices; achieve faster and accurate online diagnostics; gain the ability to perform self-test routines; and acquire ease-of-use over the life cycle of the facility with fewer trips to the field.
In today's economic times, keeping the plant up and running is essential to staying ahead. Predictive and preventative measures have become an important and critical element, and FDT is the secret to success―an easy-to-use tool for commissioning and monitoring with embedded knowledge of how and when to react to these changes. With reductions seen across the board for installations involving FDT Technology, it's no wonder this technology is rapidly being adopted around the globe.
To read more on FDT Technology, please review our previous articles submissions at: www.fdtgroup.org/na. For questions, email [email protected].
Latest from Home
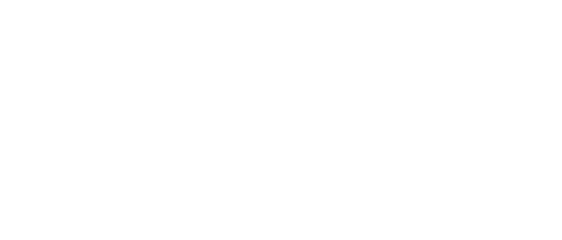
Leaders relevant to this article: