Despite the worst economic downturn in more than 70 years, Emerson Process Management's executive vice president and business leader, Steve Sonnenberg, reported that his company is reconsidering its technologies, focusing even more closely on how users actually use its solutions, and is releasing dozens of targeted products based on these reassessments. The results of this bravery might be some of the most ground-breaking and useful products ever introduced in process control and automation.
"Frankly, automation suppliers have not designed products built around the actual ways projects are executed and the ways plants are run," explained Sonnenberg. "Advancing products features are important, but designing products around how people use them is critical. I'm so excited about this week because Emerson Process Management is introducing one of the most important advances in process control in the past decade or more. And I don't simply mean the products themselves, but also the way we're approaching new product development. So, I'm proud to introduce the first of many products designed with you in mind—the new Delta V. Now things might not look that much different from where you're sitting, but I can assure you it is the biggest advance in control system I/O since the advent of bus technology. Maybe bigger."
Sonnenberg delivered his welcoming keynote address on the first day of the 2009 Emerson Global Users Exchange on Sept. 28 at the Gaylord Palms Resort and Convention Center in Orlando, Fla.
Despite the severity of the world's ongoing recession, Sonnenberg reported that more than 1,600 people are attending this year's exchange, and that the week's agenda includes a record number of presentations and short courses. "I think the theme of ‘Engaging Minds, Amazing Results' is excellent because it speaks to the power of engaging the thousands of years of experience and knowledge of the people at this conference and applies this collective knowledge to issues that you're individually experiencing today," said Sonnenberg. "The purpose is then to translate this knowledge into amazing results when you bring these ideas back to your respective companies. This is the secret to the success of this Exchange."
However, the overall economic events and challenges in late 2008 and the first three quarters of 2009 have been daunting, to say the least. " Most of us have experienced the worst downturn of our careers," said Sonnenburg, while saying the worst should be over. "We feel our business is beginning to bottom out, and that 2010 will be a year of slow recovery," he said "We continue to manage overall costs to enable us to invest heavily in product development, acquisitions and customer support activities." He noted the new Fisher Flow Technology Center that can accommodate up to 36-in. lines sizes and pressures up to 3,500 psi, successful completion of the Qatar Gas II project, which is the world's largest LNG project, and for which Emerson was the main automation contractor, and th acquisition of Norway-based Roxar this past April as examples of that.
To implement and operate its upcoming projects and processes, Sonnenberg reported that the company is launching numerous products at this week's Emerson Global User Exchange. These include a variety of new wireless devices; Foundation fieldbus functionality for SCADA applications from the company's Remote Automation Solutions group; a new version of AMS Suite Asset Portal, a web-based interface for plant asset management; and Micro Motion Division's new Insertion Liquid Density meter, which provides improved accuracy when measuring corrosive acids and alkalis.
Sonnenberg added that what's most rewarding about Emerson Process Management's new products is the difference they make in users' jobs and lives. "For example, one of our customers operates offshore platforms in the North Sea, and one of their work practices was to manually measure annulus pressure of the wellhead at every eight-hour shift change," he said. "They tested out wireless monitoring devices and recently outfitted their platforms with comprehensive wireless monitoring for pressure and other variables. This gives them much more accurate and timely data, and most importantly, it improves safety for the workers."
However, despite these and other successes, Emerson Process Management still had many other challenges to meet, according to Sonnenberg. "In my first year as business leader, I had the chance to travel the world and learn about our customers' pain points and how the recession had affected them. This gave me a personal context for the research we do each year to understand how our customers use our products, and how we can provide solutions." he explained. "We've heard that companies' demographics are changing. There's a knowledge void created by retirements and downsizing immature markets, and there's a shortage of skilled workers in developing countries. Plant jobs also have become less specialized and more generalized."
For example, Sonnenberg reported that he recently met a young CEO at a Middle Eastern petrochemical company that was planning a major expansion. However, he said that many of his operators had little automation experience, and so he needed products that didn't require much process experience. Likewise, Sonnenberg added that a senior manager at a large German chemical company told him that his plants also were upgrading, but that much of his automation expertise was leaving due to retirements and downsizing. He said their main automation objective was to ‘drive the car, but not build the car.' This means Emerson should be responsible for providing our customers with a nice, smooth and safe ride. The technology under the hood isn't as important as knowing if there is an issue. And, if there is an, issue when will it become a problem, and what can be done about it?"
Sonnenberg explained that the process control and automation field has made many advances over the years, but that it might have paid too much attention to product features and to little attention to the reality of how products actually get designed into plants and how they're used there every day. "The truth is most of the automation technologies developed in the past 30 years weren't developed based on work practices. They were developed based on features," said Sonnenberg. "Don't get me wrong. Process control technologies are incredible advanced. Our industry has come a long way in the past 20 years, and we should all be proud of it. However, the vast majority of our advances have been around technology features without considering how users interact with those technologies and how these products are used."
We're looking not only at how we can enrich our products with more features, but also how we can reconsider technologies based on how you used them, he said. "There is a genuine science behind this. It seems simple, but designing products that have more technology and more features, but are easier to use and eliminate work is actually pretty hard."
By taking the best capabilities of Delta V and making them better, Sonnenberg reported that users will be able to:
- Have control system hardware that lets them finalize their I/O design once they finalized their process design;
- Significantly reduce the need for change orders;
- Eliminate spaghetti wiring;
- Prevent the need for miles of multi-core cabling;
- Reduce thousands of hours or labor in landing I/O;
- Give users the flexibility to change their minds without getting penalized.
Perhaps the main tool enabling these gains will be Emerson Process Management's Characterization Module (CHARM) electronic marshalling modules, which it's also introducing at the this week's Exchange event. Located at the heart of the firm's new Delta V S-Series, CHARM modules allow users to add I/O as needed.
In addition, the new Delta V also is offering a Device Dashboard that prioritizes and simplifies its display on the few primary tasks and status indicators that plant operator use and need most. Likewise, Emerson also has completely redesigned the interfaces to its field instruments and is launching more than 50 new Delta V and AMS screens that take much of the complexity and hassle out of routine tasks that users deal with each day in their field instruments.
"This overhaul of our new product development process puts features second and usability first. This process reinvents the relationship between technology and people," said Sonnenberg. "We call this human-centered design, and I can promise you this is just the beginning. For Emerson, this will be a way of life. It's already become a part of our DNA.
"In fact, we've created the Emerson Human Centered Design Institute, and its sole job is to guide the thinking and hands of our product development teams to make sure we build product based on improved usability. We've already put more than 60 product development teams through intensive training on this discipline, and it's incredible to see how this thinking, this science is improving the usability of our products. We've already established more than five years of product roadmaps that will be driven by this new process."
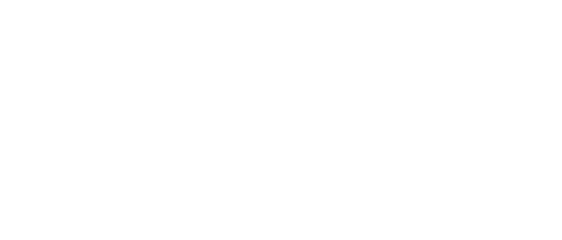
Leaders relevant to this article: