Ask the Experts is moderated by Béla Lipták, process control consultant and editor of the Instrument Engineers Handbook (IEH). Preparation of the 5th edition of the handbook requires three co-editors. If you are interested, send in your resume. To ask a control question or to join our team of experts answering the questions in this column, write to [email protected].
Q: I am trying to choose a suitable flowmeter to measure the flow rate of argon gas. I received a data sheet for one that appears very strange to me. The data sheet says that the flow element was an orifice, and the limits of flow were from 5 Nm3/h to 280 Nm3/h!!! The operating pressure was 21 barg. We are not using the orifice plate flowmeter for this application because its rangeability is only 3:1. I have looked for a flowmeter to cover this large range (56:1), and so far no success! Would you please help me in this regard?
A: The flow measurement range of a conventional orifice-dp cell combination is limited to 3:1. Intelligent dp cells can switch their range to achieve a rangeability of 10:1, but in most designs, the error in percent of actual flow will increase as the flow drops. A more accurate reading is obtained if, instead of range switching, you place two d/p cells on the same orifice, a high- and a low-range one.
If you need a range that exceeds 10:1, you can use several parallel pipe runs of different sizes and open or close as many runs as needed to keep the actual flow always between say 50% and 90% of the maximum flow in the active runs.
My choice for this high-pressure gas flow application would not be to use orifices at all. For a > 50:1 range, I would use one or preferably two Coriolis meters in parallel. If at low flows, you can live with an error of about 5%, one Coriolis meter is enough. Other high- rangeability flowmeter options include thermal (20:1), turbine (10:1), utrasonic (10:1), and vortex (10:1).
Béla Liptak
Q: We have a bubbler application that has a plugging problem. We have tried various configurations of the tip to reduce the pluggingangled, notched, etc., with little relief.
I remember that many years ago in another difficult application another engineer used a dip-tube diaphragm. I believe there were separate diaphragms on the high and low sides, and that the diaphragms had very small holes. There was a very light purge, on the order of 1 SCFH or less, through a dp regulator for each side. This was very successful.
Unfortunately, that engineer is no longer with us. Now Im working for another company, and nobody at that plant can remember where the diaphragm was purchased.
Both applications are not pressure vessels. The new application runs at 20-25 psig.
Can you recommend some vendors for this application?
Jim Becker
Bayer MaterialScience
[email protected]
A: Is the questioner referring to the PMC 1:1 pneumatic repeater design (www.pmc1.com), which I have previously modified to build a submersible variation to replace bubbler tubes? PMC now makes an electronic dipstick version. The same folk also make submersible electronic transmitters. PMC does have a pneumatic dip tube replacement as a standard product.
These units were originally built for the pulp and paper industry (PMC was once the Paper Machinery Company), but I have found them handy in mineral processing units over the years.
Ian H. Gibson
Engineering Consultant
Process, Control and Safety Systems
A: A prominent cause of plugging of bubble tubes is dehydration of the solution or slurry in the vessel by the purge gas. One solution is to hydrate the purge gas in another bubbler of clear solvent before it enters the main bubbler. Another possibility is the use of a liquid purge.
Greg Shinskey
Process Control Consultant
Wolfeboro, NH 03894
A: I do not know where you can get diaphragms such as the ones you mention.
In my experience, however, the smaller the bubble orifice and/or purge rate, the easier it is to get plugging. Large-diameter orifices (I have seen 6-in. diameter bubble pipe tips) are often used in wastewater wet wells with good results. It may take a while for the expanded section to fill and equalize if the purge gas is stopped or the bubbler end uncovered, but the large orifice did work pretty well.
I do remember once seeing a bladder-type pressure sensor setup, but I do not remember the manufacturer.
I will also mention that notches in a bubble pipe tip are often used to make the bubbles release in the best spot with regard to error from liquid moving past the orifice.
Al Pawlowski, PE
ALMONT Engineering
Baton Rouge, La., U.S.
A: It is well-known that plugging problems decrease as the square of the diameter of the dip tube. The problem writer gave no information as to the cause or definition of plugging in his application.
If the problem is salts build-up, then a small purge of the appropriate solvent will help keep the relative humidity high enough to reduce the drying effect of the dry gas. Higher liquid flow rates might wash the salts out.
If the problem is freezing polymers, a few users heat the purge gas and/or use a steam- jacketed dip tube.
At one time, it was thought that a notch in the end of the dip tube caused the gas bubbles to be smaller and thus cause less pressure noise. Note that anything more than a very small notch would result in some difference in dip-tube pressure as the supply flow rate changed. It is very important to be sure that the purge gas supply is ALWAYS at a pressure higher than the vessel. Otherwise, the vessel fluids back up into the dip tube and often stay there. The purge gas flow is controlled by a needle valve, not the pressure regulator, and observed with a small rotameter. If a supply pressure regulator is used, it must be a non bleed type so that if the vessel pressure becomes higher than it should be, process fluids will not enter the dip tube system. Some engineers argue that the constant flow regulator sometimes recommended will open on loss of supply pressure and allow back flow.
Always remember that despite flow sheets and declarations by process people, at some time every vessel and every pipe will be exposed to pressures up to the relief valve pressure or failure pressure, and correlatively, every closed system will eventually be exposed to a high vacuum.
The purge-flow supply rate must be more than enough to overcome the maximum rate of pressure rise in the purge system. Note that this involves knowing the gas volume of the purge system, since the pressure of the entire purge system must be raised.
In extreme cases where no level measurement device except a purged dip tube was reliable and the dip tube always eventually would plug, a number of schemes were used to either permit quick dip-tube replacement or to facilitate drilling out the plug. These schemes usually involved systems of ball valves, packed slip joints and other clever mechanical devices.
Moore Products made several purged remote chemical diaphragm seals. These were used where plugging problems were insurmountable or where purge gas flow into the process was not allowed. They used a simple pressure balance scheme where the purge gas pressure on the dry side of the diaphragm rose to match the pressure on the wet side. Excess supply gas was vented outside the vessel through a vent connection as the purge gas rose above the process pressure.
These have limited pressure and temperature ratings. Installation requires a nozzle large enough to pass the assembly. Some small pressure differences will exist across the diaphragm, and errors may result from these.
Cullen Langford, PE
A: If the installation is in an existing plant, the bubbler pipe itself is usually made and installed by the user. If it is a new plant, the engineering firm designing the plant provides it as a piping item. A few suppliers also exist, such as Campbell Scientific, CR10, Omega Engineering, Kele Assoc., Texmate Inc., Introtek International.
The various aspects of bubbler-based level measurement are discussed in Chapter 3.2 of the 4th edition of Volume 1 of the Instrument Engineers Handbook.
Béla Lipták
Q: I have a device called the Loop Slooth for rapid troubleshooting of ground loops. Information about it is at www.loopslooth.com. It gives a brief pictorial overview of how the Loop Slooth works and has links to the instruction manual and to a paper in the Review of Scientific Instruments. Im interested in finding companies that might be interested in this product.
Paul Bellan
Circuit Insights LLC
A: The best possibility would be with the companies who have related products. Usually their R&D or product development groups are the ones that review concepts from third-party sources and determine their market viability. But certain companies have a policy of developing only those ideas which are created internally.
The Loop Slooth might be of interest to companies like Fluke, AEMC, Elcontrol, BMI/Dranetz, . . .
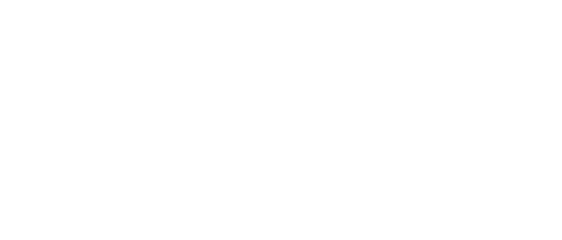
Leaders relevant to this article: