Ask the Experts, is moderated by noted process control authority Béla Lipták. Béla is also editor of the Instrument Engineers Handbook (IEH). Preparation of the 5th edition of the handbook requires three co-editors. If you are interested, send in your resume. To ask a control question or to join our team of experts email [email protected].
Q: I work in a nuclear power plant, and I am reading in your handbook that a d/p level transmitter with a reference leg caused the Three Mile Island accident. You say it can indicate full, when the reactor water level is low. Can you explain?
George Farnsworth
A: At Three Mile Island, the reactor core overheated, and this heat caused the boiling of the high-pressure water (the moderator in the reactor). While water is a moderator, steam is not and, therefore, boiling eliminated the moderator and speeded up the nuclear reaction, eventually causing the partial meltdown of the core. The operators did not know that the water in the reactor was boiling and, therefore, the quantity of water remaining in the reactor was dropped because the heat also evaporated the water in the wet leg on the high-pressure side of the d/p cell. (Figure 1) Having steam at the same pressure on both of its sides, the d/p cell detected a zero difference, which indicates a high water level in the reactor.
I might note that I have seen in other industries similarly unacceptable level detectors giving false readings if the water is boiling.
Béla Lipták
Q: What would be the result if the pressure signal of outlet steam instead of steam flow rate is incorporated in a three-element control loop?
A: The three-element level control systems operate on a mass-balance basis: Flow of feedwater in is set equal to steam flow out, biased by the level controller to trim out any error between the two flow measurements. Steam pressure does not measure flow and is independent of flow in the steady state. It has been used as a transient correction for shrink and swell, but normally is a controlled variable.
If the steam is fed to a turbine, first-stage turbine inlet pressure is sometimes used as an indication of steam flow because it varies linearly with flow to the turbine.
Greg Shinskey
Process Control Consultant
A: Fundamental to boiler control is the use of the pressure signal to forestall a boiler explosion by limiting the firing (fuel) rate and by the use of the steam-flow rate signal to anticipate the water level in the boiler and thereby prevent burn-through or flooding of the steam header.
Boilers typically are qualified for service with a specific control regimen by local safety authorities using existing codes and the insurance carrier for the installation, who often imposes additional restrictions. No changes should be contemplated or made without consulting them and gaining their prior approval.
Combining the pressure signal with the steam-flow signal, using an appropriate algorithm, permits the more precise computation of the steam rate in units of mass per unit of time. Since most boilers operate at a near-constant pressure, the set pressure is assumed when the steam-rate signal is calibrated in units of mass/time.
Otto Muller-Girard, PE, FISA.
A: Throttle pressure often is used as feed-forward for over fire, but each boiler has its own characteristics. Steam flow increases as a result of drooping pressure, so they are related. But the flow change, acting as feed-forward, is fasterno capacity.
Stephan Gaertner
[email protected]
Q: I just read your e-book on distillation control and optimization. It is interesting to see refining deny the need for accuracy in its field instrumentation. What kind of accuracy would be needed on the flow readings for the material balance? Would refiners and the modeling benefit from accurate mass flow?
Pamela K. Quillin, PE
Industry Marketing Manager-Refining
Micro Motion, Inc.
A: The energy saving potential from implementing better control and optimization strategies at our old refineries is very substantial. One reason for the outdated controls in refineries is that no new refineries have been built for 30 years; hence, their instrumentation is a generartion old. In flow metering, that usually means orifices.
It is a mistake to believe that refineries will not be needed much longer. In fact, during the transition from the present oil-based economy to a renewable and clean one, the importance of distillation will actually increase, because the value of the refinery products will rise and also because bio-fuel production also involves distillation.
Reasons why accurate mass flow meters should be considered include the value gained from obtaining accurate material and heat balances, desirable for feed-forward-based optimization.
Accurate flow detection is also important in minimizing the wasting of heat throughout the refinery. Very few refineries bother to recover the heat content of hot bottoms flows or the heat removed at the condensers and reuse it for preheating. Accurate flow metering can provide management with reliable data not only on the waste-heat recovery, but also overall heat and material balances of both the individual columns and the overall plant.
Béla Lipták
Q: Can you advise me on process control system (PCS) management, that is on how the information technology department can be involved and to what extent support the PCS. What should be the level of interfacing of process control systems with business applications?
Amr Aboelela, CISA CISM
Consultant RAS, IT Advisory
KPMG, Qatar
A: The modern control system does seem to be forcing the opposing camps of process control and IT to play well together. To me, the key to success seems to be to have very clear definitions and work practices. Some key considerations include segregation of IP addresses, backup and recovery plans, upgrades, firewalls and DMZs, user account management. There are definitely some synergies with shared duties, but some things are best kept segregated.
The connections to business applications also tend to vary by company, mainly since different companies have very different business needs at times. Increasingly mission-critical information is passed back and forth from the control system to the business systems. Common interactions include:
- Real-time order to plant floor for order fulfillment;
- Links to maintenance systems for work-order and history entry;
- Links to technical information (operating procedures, process documentation, alarm management information, environmental permits, etc.);
- Links to other information (user changes, alarm history, batch history, etc.).
Bridget A. Fitzpatrick
Mustang Engineering
[email protected]
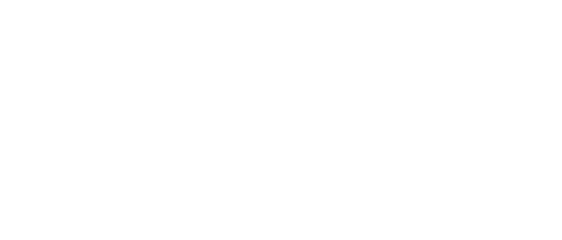
Leaders relevant to this article: