BP and Emerson Process Management continue to collaborate on the application of wireless technology to speed use of the innovative technology for business improvement. BP has expanded its Cherry Point refinery applications, installed Emerson’s Smart Wireless network throughout its tank farm in its R&D facility in Naperville, Ill., U.S., and is making installations at its other refineries around the world.
BP Cherry Point is a 225,000-bpd refinery located in northwestern Washington state in the U.S., and is the largest supplier of calcined coke to the aluminum industry. One out of every six aluminum cans is made using BP Cherry Point’s calcined coke. Smart Wireless transmitters on the refinery’s calciner unit monitor bearing and calciner coke temperatures to help prevent fan and conveyor failure. Fans can cost up to $100,000 to repair, but more important, can be down for up to 10 days with associated production losses.
The 15-transmitter wireless installation, done in 2006, is believed to be the world’s first industrial wireless mesh network, and continues to run reliably while eliminating operator rounds in the field.
Cherry Point has expanded wireless use to 35 transmitters, including tank farm and utility applications, and installation of an Emerson Smart Wireless gateway in the diesel unit to make it ready for wireless devices.
BP’S TANK FARM PROVING GROUND
At BP’s research and development campus near Chicago, a tank farm (pictured above and on cover) provides a venue to try out new wireless functions as they become available. The real-world environment in a pilot-scale operation provides feedback to Emerson Process Management, the wireless network provider, and hands-on experience for refinery management.
“The principal advantage we see around wireless is the ability to accumulate and analyze a much greater array of data than would otherwise be economically possible,” says Mike Ingraham, technology manager for Cherry Point refinery. “Wireless enables us to get more data, more efficiently, more economically than we ever have been able to in the past. We really hope our wireless technology will be a principal tool in maintaining plant availability while expanding our flexibility to meet fuel specs and an ever-changing array of feedstock.”
A second facility, BP Naperville R&D, is a worldclass technology center that includes a recently modernized
tank farm feeding an expanding number of pilot plants that develop processing technology options for BP refining worldwide. “Following the first application of Smart Wireless at BP’s Cherry Point refinery, which BP saw as a success, the company installed a 45-transmitter network at the Naperville tank farm. Operational for about one year, this has provided strong operational experience, and a platform for testing the technology, leading to significant take-up of wireless at BP refineries throughout the world.
“The wireless devices allow our operators to be more efficient, collecting data from one central point as opposed to walking around the tank farm and recording all the values,” says a BP representative. “The other advantage of the wireless devices is that they supply data continuously for recording in our historian, allowing us to see what is happening in the tank farm at any time of the day.”
The Naperville wireless network uses Rosemount wireless transmitters to monitor suction and discharge pressures, levels, flow and temperatures. New wireless functions are installed as they become available, and emphasis is on collaboration with Emerson to expand the capabilities as rapidly as possible to cover refinerywide applications. The real-world environment in a pilot-scale operation provides feedback to Emerson and hands-on experience for refinery management. Options for refinery process optimization and sharing of wireless automation technology are thereby shared globally by the Refining Technology team.
“Wireless is an important enabler for refinery-of-the-future technologies,” comments Mark Howard, commercial technology manager at BP. “It helps us deploy the sort of instrumentation, sensors and analytical devices that we need for condition monitoring to support predictive maintenance, tracking feedstock through the value chain and a host of other applications. Wireless is a very important vehicle for getting instrumentation into places where wired instrumentation would be too expensive or, frankly, not very practical.”
Howard adds, “Looking ahead, we like the move toward standards such as WirelessHART in the Emerson technology. We like being able to access new wireless transmitters as quickly as we can deploy them, and we’re getting very robust operation. We look forward to a greater range of instrumentation becoming available.”
“We value highly the collaboration with BP Refining Technology team,” says John Berra, chairman, Emerson Process Management. “Smart Wireless was conceived through years of research and development that led to Emerson’s pioneering introduction to the market in 2006. Key in this effort was the parallel pioneering effort by BP in its trial mesh installation of Smart Wireless at Cherry Point in that same year. Our combined efforts have, I believe, moved the age of wireless forward at an accelerated pace.”
“We share BP’s important objective of speeding innovation to deliver standard interoperable wireless technology for improved plant reliability, safety and environmental compliance,” concludes Berra.
Croda, CFE LAPEM Win Wireless Innovator Awards
At the Emerson Global Users Exchange 2008, an end-user panel awarded Croda Inc.’s moving railcar monitoring application as “Most Creative” and CFE LAP EM’s temporary power unit monitoring application as having the “Most Significant Business Impact” in Emerson’s Smart Wireless Innovators Application Contest.
Designed to recognize creativity and business value from applications of the company’s Smart Wireless solutions, entries in this first annual contest were from production, manufacturing and distribution facilities around the world. The “innovation” criteria included the extent to which the use of wireless was novel; the identification of previously unknown process issues; the degree to which using wired technology wouldn’t have been possible; and the extent of real operations improvement.
The winning score went to Croda Inc., an international specialty chemical maker, for its monitoring of temperatures in moving railcars at its plant in Mill Hall Pa., U.S. The “business results” criteria included demonstrated dollar savings in operations; installation savings compared to a wired approach; time savings for implementing with wireless; and the extent to which safety or environmental effects were improved.
Scoring highest was CFE LAPEM, a laboratory analysis group within the Federal Electrical Commission of Mexico. LAPEM has five analysis teams that set up temporary measurement facilities at each of 140 power plants. One team’s easy establishment of a temporary wireless network in power plants made it possible to increase its productivity and plant coverage by 10% and to increase annual service revenue by US $512,000.
“We are excited at the great range of wireless applications across industries and around the world that we received,” commented Peter Zornio, chief strategic officer of Emerson Process Management. “The contest unveiled what is really an amazing display of ease of use, flexibility, reliability and business value delivery.”
Wireless Promises Big CapEx Savings
At last month’s Emerson Global Users Exchange, John Dolenc (pictured) presented a detailed study on the potential impact of wireless technology in the construction of a new capital project, in particular, a hypothetical hydrotreater.
Watch for the detailed results of Dolenc’s analysis in the next issue of WirelessNow, where the study will be expanded to include the role of wireless on a fieldbus project.
Boise Boosts Safety Response
Until recently and until wireless, Boise’s St. Helen, Ore., U.S., paper mill did not have a monitoring network for its eye-wash and safety-shower stations, relying instead upon individual radio communications.
So to better ensure the overall safety of both plant personnel and its contractors, the mill explored options to alert the control room automatically if any of its eye-wash or safety-shower stations were activated. That way, operators could quickly dispatch assistance to the station and investigate for possible injuries.
But at an estimated $40,000, the tab to install hard-wired monitors on the eight safety stations was pricey. “We had looked into installing a wired network monitoring system, but it was cost-prohibitive to do so,” Taylor says. “But by installing a wireless network instead, we were able to save about 60% in installation costs.”
Today, when any one of the eye-wash or safetyshower stations at the mill is turned on, Rosemount wireless discrete transmitters in a self-organizing Smart Wireless field network immediately communicate with the mill’s operating system, and the alert is conveyed to the mill control room.
The switches and Smart Wireless Gateway were easy to install and commission. Some of the switches are as far as 200 feet from the gateway. The gateway interfaces with an OPC server, which delivers reliable data to the mill’s operating system. The robust wireless network monitors the switches every 15 seconds.
“Because we have established this wireless network infrastructure,” Taylor adds, “we anticipate that for low cost we can easily add additional transmitters at our mill for use with other applications.”
Latest from Home
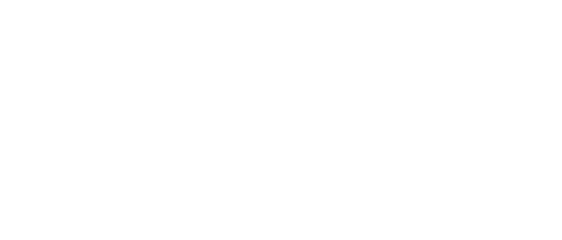
Leaders relevant to this article: