The gross world product was estimated at $65.85 trillion in 2007, and the combined global debt is over $100 trillion. Future generations will inherit not only this debt, but also the melting ice caps, the atmosphere turned into a garbage dump, the nearly exhausted global resources, not to mention our military bases and nuclear warheads that can destroy the planet 25 times over. Yet warheads do not increase our reserves, only the likelihood of energy wars.
Mankind’s overloaded “ship” is sinking, yet some passengers argue that it is just rocking with the waves. Others believe that the leak will plug by itself, or the ship will drift to shore on its own. Still others argue that the leak is small, and there is no urgency to fix it or are sharpening their knives to fight their way get the remains in the kitchen. This series of articles speaks to those passengers who want to plug the hole and do not want our grandchildren to ask, “Why did you not act?”
The road to an inexhaustible and clean energy future is obvious. The third industrial revolution is already beginning: Just as we lead the world in developing the computers, we Americans must find the moral courage and determination to lead this revolution also. The process control profession (the only profession that is capable of integrating and optimizing complete processes) should be in the forefront of this effort.
In this series of articles, I am describing the components of this, the world’s first 1,000- MW solar-hydrogen electric power plant. Below I will describe the electrolyzer that converts solar energy into electricity during the day and uses that to make electricity at night. My invention is to develop the controls and optimization needed to convert this electrolyzer into a reversible fuel cell (RFC), so that the same RFC can be used at a fraction of the present cost to make solar energy continuously available.
Making Solar Energy Continuously Available
The development of the controls and optimization strategies of this new process will be difficult. Yet once we have figured it out, it will serve not only power plants, but also “energy free” households with solar roofs and electric cars. In these homes, the reversible fuel cells (RFCs) will generate hydrogen when the sun is out and will refill the hydrogen fuel tank, reducing the cost of transportation by a factor of three to five. When solar power is unavailable, it will use the inexpensive night-time electricity to make hydrogen to be used at peak periods during the day.
Hydrogen fuel is safe. It is used in space exploration to lift vehicles into orbit. The international space station uses an acre of solar collectors to provide it with electricity.
The main reason why hydrogen is safer than gasoline is its low molecular weight, which in case of an accident, causes it to rise instead of soaking into the ground. Hydrogen technology is well-established, used by industry, but practically unused in power plants.
In January, I was on a lecture tour in India describing the controls and optimization of the world’s first solar-hydrogen power plant. Here I will discuss only one aspect of this new power plant, the way how solar energy can be stored during the day so that it can be made available at night, thereby making solar energy continuously available.
In nature, hydrogen is produced by plants. Vegetation uses sunshine as the energy source to break down water into hydrogen and oxygen. The oxygen is released while a catalyst in the plants (chlorophyll) serves to decompose water and to generate hydrogen. Once water is decomposed, the plants use the hydrogen to react with the carbon dioxide in the air to produce glucose and cellulose.
Therefore, plants emit oxygen while taking up carbon dioxide. Animals and humans do just the opposite. They obtain their energy by oxidizing glucose and cellulose while inhaling oxygen and exhaling carbon dioxide. When the concentration of plant and animal life on the planet is in balance, the atmospheric concentration of carbon dioxide is constant. When mankind overpopulates and its lifestyle also generates more carbon dioxide while plant life shrinks, the balance is upset.
For the last million years the carbon dioxide concentration of the atmosphere stood at 280 ppm. As the industrial age began and the proportion of forests and plant life was, the carbon dioxide concentration of the atmosphere increased to 380 ppm, and soon will have doubled as our carbon footprint further increases. Yet,this balance can be reestablished by using sunshine to make hydrogen and burning hydrogen to meet our energy needs.
Figure 1: I held eleven lectures in six cities on the automation of renewable energy processes
The Electrolyzer
Today, the United States is using some 9 billion cubic feet of hydrogen a day in the petrochemical, food and rocket propulsion industries. Some 98% of the bulk hydrogen is produced by steam reformation of natural gas. When hydrogen is made from fossil fuels, the carbon is exhausted into the atmosphere, and this contributes to global warming.
In 1820, Faraday discovered electrolysis by passing electricity through water and thereby generating hydrogen at the negative electrode (cathode) and oxygen at the positive electrode (anode) of the electrolyzer. Thus he found that hydrogen can be produced from water. If the energy of the sun is used to drive this process (as is the case with plant life) the fuel is free, and the emission is only oxygen. This process is called electrolysis. The electricity for operating an electrolyzer can be provided by a battery (Figure 2) or by solar collectors.
Fuel cells are electrolyzers in reverse: They generate electricity by oxidizing hydrogen into water. Today, both the fuel cells and the electrolyzers are bulky and expensive, but that can be changed by good process control. In the March issue (www.controlglobal.com/articles/2008/073.html) I have described how the size and weight of this combined device (the reversible or regenerative fuel cell–RFC) can be reduced, and how the two devices can be combined into a single unit that can fulfill both functions. Once this is accomplished, and the RHCs are mass-produced, their costs will drop, and our dependence on fossil fuels will be over.
Electrolysis is an endothermic reaction and requires energy to occur (blue arrow in Figure 3), while the fuel-cell reaction, which oxidizes hydrogen into water is exothermic (red arrow in Figure 3). Depositing one mole of any material at the cathode of an electrolytic cell requires 96,484 coulombs (Faraday’s constant). Therefore, it takes 237.13 kJ (224.79 BTU = 0.066 kwh) of electricity to synthesize one mole of hydrogen. When hydrogen is generated at ambient temperatures, the environment contributes 48.7 kJ of thermal energy for a total of 286 kJ.
The weight of one mole of hydrogen is 2 grams, and the energy content of one gallon of gasoline equals the energy content of one kilogram (about 500 moles) of hydrogen. Therefore the electricity needed to obtain the amount of hydrogen, which has the same energy content as one gallon of gasoline, is: 32.9 kWh. [(237.13 x 500 x 0.948)/3,413)]. Naturally if free solar energy generates the electricity, the cost of generation is only the cost of equipment depreciation and the emission is only oxygen. As shown in Figure 2,
It takes the same amount of energy to split water into hydrogen and oxygen as the energy obtained by oxidizing hydrogen into water. The only difference between the two operations is that electrolysis increases the entropy and, therefore, not all the energy needs to be supplied in the form of electricity, as the environment also contributes 48.7 kJ in the form of thermal energy. Therefore, only 237.1 kJ of electrical energy is needed to make a mole of hydrogen from water. On the other hand, in case of the fuel cell operation, the oxidation of one mole of hydrogen will generate 237.1 kJ of electrical energy plus 48.7 kJ of heat. Therefore, when the RFC operates in the hydrogen- generating mode (when the sun is out), it cools, and when it operates in the electricity generating mode (at night), it heats its environment.
There are two types of water electrolyzers: alkaline and polymer (PEM). The alkaline designs can be unipolar or bipolar (Figure 4). In the unipolar design, the anode and the cathode are separated by a semi-permeable diaphragm membrane and are immersed in an alkaline solution. The diaphragm allows only salts to pass through and prevents the gases from mixing. The hydrogen and oxygen that is so produced is dried downstream of the electrolyzer to remove water vapor. These units operate at lower current densities and temperatures and must be under differential pressure control to protect the diaphragm.
In proton exchange membrane (PEM) or solid polymer electrolyte (SPE) electrolysis, the electrolyte is replaced by an ion-exchange resin. These units are compact, provide high current densities, but are more expensive and because of the corrosive nature of the electrolyte, require special materials of construction.
Continue Reading
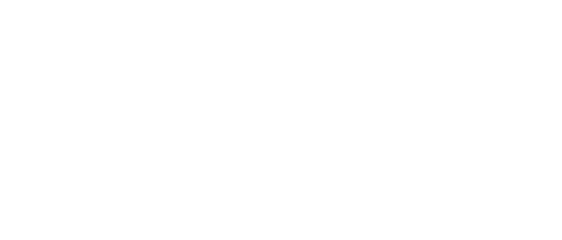
Leaders relevant to this article: