By Jim Montague, executive editor
Check our Batch Manufacturing Guide, click here.
Tim Dunlap isnt a coffee-slinging barista, but he probably makes more Frappuccino than anyone else on Earthabout 13,500 gallons per day.
Thats because hes the engineering and maintenance manager at the Dairy Farmers of Americas (DFA) plant in Mechanicsburg, Pa., which brews, blends and bottles Starbucks-licensed coffee drinks for distribution by Pepsi USA throughout the eastern U.S. To keep up with demand, Dunlap says the plant underwent a major expansion two years ago, from 600 bottles per minute on one glass line to 1,400 bottles per minute on two lines.
Wed always been automated with PLCs, but we knew we couldnt double our production with the proprietary controls, ActiveX screens and jumper panels we had before, says Dunlap. So we put a team together with the plants staff, our system integrator, GES Technology, and DFAs Dairy Systems to install an 800-bottle-per-minute glass line. The new line uses Rockwell Automations RS View and some ISA 88 integration, which was very standardized and easier to add onto. This allowed us to change code and modify screens as needed. GES had to write some code at the beginning, but now we can select among automated flow path changes.
To change products, we used to have to make both mechanical and software changes. Now, we only have to make software changes. ISA 88 and RS View also verify critical time and temperature on the lines and help us document performance too. Even adding new flavors in the future wont be a big capital expense.
Happy Days
So, everybody loves batch, and its not because theyre all getting cookies, cupcakes or Frappuccino. The 12-year-old ISA-88 batch standard and its revisions have pretty much solidified its position in the process control world, and now potential users increasingly are calling on suppliers to include it in their solutions.
ISA-88 has matured to the point that its going through revisions to comply with ISA-95, says Tim Stout, process systems department manager for Matrix Technologies, a CSIA-certified system integrator in Maumee, Ohio. The standard is widely accepted enough now that customers are talking about it and want to use it, so vendors are providing platforms, toolkits and software for them. Weve written a lot of ISA-88 concept software, and the tools just keep getting better, which means its also easier for us to put together projects with these controls. Standard batch functions and tools are becoming the glue that everything else attaches to. At this years World Batch Forum meeting, we learned that batch concepts are being applied to continuous processes and at the packaging level. Batch is even standardizing relationships between process, control and IT people because it gives them all a common language.
Why It Works
Batch is different than process control in how its set up and programmed. Batch lends itself to a more modular software design, so if you create the right blocks, you can rearrange them for different applications, says Hunter Vegas, of Avid Solutions Inc., a system integrator based in Winston Salem, N.C. If you do it right, you can save lots of time and money because the same piece of code can be applied to all three reactors in an application, instead of having to rewrite code for each phase in a recipe.
ISA-88 Physical Model
Source: Applying S88, Batch Control from a Users Perspective by Jim Parshall and Larry Lamb, ISA, publisher.
The Basics
Similar to any process control initiative, a batch projects organizers and developers also must evaluate the overall business goals served by their application, assess what equipment their existing facility already has and decide what it will need for their plan to succeed.
Basically, continuous processes typically run without stopping, while batches are turned on and off. Distributed control systems (DCS) typically scan every 200-500 milliseconds, while batches need scan times of 100-200 milliseconds, according to Kam Yuen, product manager for GE Fanucs Proficy batch execution system. He adds that GE Fanucs new Proficy Process System combines these DCS- and PLC-based capabilities, and can use modular, reusable software function blocks to create batch sequences and set up phases more easily.
Theres a big difference between even a simple batch program that can be hard-coded into a PLC and a complex batch system that needs to handle 30 to 40 different products and doesnt have a fixed path. Users must think of all their applications stop scenarios and plan for all their contingencies, says Todd Stauffer, Siemens Energy & Automations Simatic PCS 7 marketing manager. These days, many users want to do both simple and complex, and they want to use the same software to do it. Luckily, ISA-88 and its extended definitions describe how developers should organize their software code. (Figure 1)
Lingering Reluctance
Despite batchs growing acceptance, some potential users are still hesitant about trying it, especially if theyd only been considering a simpler type of automation. Ladder logic is still the king in terms of comfort. I think 80s% of the code we see is ladder, and the remaining 20% is IEC formats like sequential function block and standard text, says Craig Bransfield, engineering manager at Automated Control and Technical Services, a CSIA-certified system integrator in Bakersfield, Calif. When I pipe up and tell customers there are ISA-88 programs and models they can use, most get that deer-in-the-headlights look. But once we get them to try ISA-88, they say, Wow! This is great! It just takes awhile to get them to that point.
Bransfield adds that users are initially worried about new batch methods because they dont know if their staffs will be able to respond appropriately. Theyre concerned that the guy who has to come in at 2 a.m. on Sunday will be able to respond quickly and safely, and ladder still gives that warm fuzzy feeling that they can do it, adds Bransfield. Were very sympathetic to these worries, and so well spend half a day showing people on a laptop how well batch programs work until the concept sinks in, and theyre willing to rely on it.
Once batch is adopted, Bransfield reports that ISA-88s common jargon and handshake protocols can help increase users comfort level. If I walked into an application that someone else built years ago, and they used ISA-88, I would know just what to look for, he says. Its very comforting for customers to know that we can respond that well.
Background Benefits
Experienced users say knowing how ISA-88 originated can help rookies understand it better and enable them to develop future solutions to meet the unique needs of their own applications.
More Pressure, LESS STRESS
AstraZenecas Ann Lindholtz uses ABBs System 800xA to increase vessel pressure, continuing a drug process and recipe in its batch protocol.
Rob Purvy, senior consultant with Siemens E&As process automation division, explains, Batch approaches have changed along with technological advances. Were now living in a more Windows-based society, so thats meant changes for batch too. Before the mid-1990s, we did inflexible, monolithic batch code programming. This situation shifted when users began defining recipes in their PLCs or controllers. Then ISA-88 was able to separate equipment-control from recipe-development definitions. ISA-88 also gave everyone a common, flexible language for batch applications. Now chemical engineers can make flexible recipe changes and push through new products more quickly. As a result, ISA-88 is widely accepted, and users want to put in ISA-88 systems.
For example, Air Products plant in Wichita, Kan., recently completed the first of two phases of a migration from a 20-year-old continuous process control system to a Siemens PCS 7 (DCS) with Simatic Batch management software. The first phase was at the facilitys South Plant, a hydrogen reaction facility, specializing in polyurethane curing agents and additives (Figure 3). It normally produces 35 products, but can make up to 250 products.
The project team needed only 18 days to complete the new installation, which controls 75 unit vessels and 50 equipment modules. During the outage, the team installed the new PCS 7 system, made sure more than 2,500 I/O points were transitioned and tested the Simatic Batch configuration for production sequencing. Plant manager Ramon Lopez reports the new software will increase his plants capacity and improve visibility of its processes.
We now have a more precise way of making our chemicals, and it will be consistent, shift after shift, hour after hour, says Lopez. This reduces raw material costs. Being able to operate the equipment consistently all the time also will reduce maintenance. Reducing downtime by 5% is a big improvement. The Wichita plant has reduced material, labor and field installation costs by about 30% after one year of operation.
Branching Out and Up
Batch applications are evolving rapidly, moving into some new and unexpected areas, such as packaging, and even beginning to form links with the enterprise level, thanks to a working group combining ISA-88 and ISA-95 committee members. In fact, Dawn Marruchella, batch product manager at Emerson Process Management says efforts are underway by several non-batch industries to come up with ways to apply ISA-88 and ISA-95 methods to their own applications.
Other industries are finding that they must find standard ways to communicate, and then integrate with higher levels, says Marruchella.
Some companies are even building standards for their own software based on how ISA-88 does it, and then building a library of standard modules to reduce project work.
For instance, A-CTS Bransfield reports that he applied an ISA-88 batch design to help rebuild the co-generation engine at small, 500-kilowatt power plant operated by Crimson Resource Management in Castaic, Calif. The plant uses natural gas from its oilfield to produce electricity. I chose to arrange the generator and its engine as a batch design, but the one difference was that this application keeps the batch in a running state. Usually a running state has an endpoint, but this does not. It just makes power until the operator tells it to stop. This application has nothing to do with a traditional batch, but it was still highly adaptable to it.
Similarly, Dr. Carl Lawton, of the University of Massachusetts Lowells Bio Manufacturing Center (BMC), reports that his facility is optimizing its pilot plants new batch bioreactor with help from Invensys Foxboros InFusion solution. The center received $50 million in initial state and other financing and is expected to receive hundred of millions more as its missions and projects multiply as part of the Massachusetts Life Sciences Initiative.
There hasnt been a lot of process control in biopharmaceutical manufacturing yet, and so the joke is that potato chip makers are more advanced than us, says Lawton.
Lawton adds that one overall effort in his field is to get away from using the typical 1,000-gallon, stainless-steel vessels to focus on short-run, pilot production that can confirm proper process development and resolve commercial production issues. This allows developers to reduce costs of their initial engineering runs, and conduct more of them. For example, Lawton BMC has been working with Nova Biomedical, Waltham, Mass., on a joint glucose feedback control system. Though also still in the pilot stage, this project could improve several biopharmaceutical manufacturing processes.
Big time batch
Air Products plant in Wichita, Kan., uses Siemens E&As PCS 7 and Simatic Batch software to improve product consistency, reduce downtime and maintenance costs, and gather historical data.
We can use the system were building now with InFusion to make good laboratory practices (GLP) materials, and then move into good manufacturing practice (GMP) areas, adds Lawton.
In addition, AstraZeneca recently rebuilt its 20-year-old beta blocker pharmaceutical batch plant in Sodertalje, Sweden, and implemented a batch protocol-focused system controlled by ABBs System 800xA and SattLine system based on eight System 800xA servers (Figure 2). AstraZenecas new automation system includes batch and information management modules incorporating functions for batch production, modelling, execution, batch control and reporting for traceability and GMP-based validation.
From here we can control the entire plant, says operator Ann Lindholtz, from AstraZenecas control room, where she uses her signature to approve increasing pressure in a vessel to 265 kPa by opening a valve. This continues a pharmaceutical process according to its recipe in the applications electronic batch protocol. Batch not only rocksit rules.
Check our Batch Manufacturing Guide, click here.
Tips for Engineering a Batch Project
The following recommendations for successfully implementing a batch project are from Tips and Tricks to Applying S88 Batch Standards to Chemical Plant Batch Systems by P. Hunter Vegas of Avid Solutions Inc. in Winston Salem, N.C.
Do not try to learn batch on the fly. Decisions you make now will haunt you for the life of the system. Find someone who has successfully programmed similar systems, and check beyond initial references with whoever is maintaining the batch system your candidate installed. If the project budget is tight, consider hiring your candidate for a few days to help lay out the general recipe structure and phase definitions.
Select a few products representative of the required recipes. Lay them out using sequential function charts (SFCs), and note the number of parallel phases. Also, remember the puzzle-piece phase technique. Does it make sense to split up a task into smaller pieces? Once the basic phase function is determined, identify the required phase parameters. If a phase needs different parameters in different recipes, consider creating one phase that uses all the phase parameters and dummy out the unused ones.
If setpoint ramping or stepping is required for reactor heating/cooling, consider creating a reactor profile phase (RPP), rather than making a heating/cooling phase with built-in ramping. RPP runs parallel to the heating/cooling phase and is mode synchronized with it. As RPP runs, it writes setpoints to the heating/cooling phase. This lets developers use the same heating/cooling phases for all recipes.
A recipe often requires verification that raw materials are available before starting the charge phase. Rather than programming this function into your charge phases, create a weight-check phase with a minimum and maximum allowable range for a weight or level. If the reading of interest isnt in range, then the phase goes to hold.
Now the phases can be programmed with minimal rework. Issues to consider at this stage include:
- Consider remote versus local mode for valves and pumps. Nearly all control systems have Remote/Local modesor sometimes Manual/Auto and even Cascade modesfor valves and pumps. Generally, the valve orpump is controlled by the computer in one mode and by the operator in another. Sometimes the valve or pump has a mode, where it can be controlled by either. Some designers require operators to place each device in Remote or Cascade mode, or the batch wont function. Others allow the computer or operator to move valves. Its crucial to handle the modes cleanly in programming. If all the valves and pumps must be in Remote/Cascade mode, check this before starting the phase. Force the phase to hold if a required valve/pump mode is incorrect. If the control system allows computer or operator control, then the pump and valve status should be monitored, so the phase will go to Hold if a valve or pump changes state unexpectedly.
- Reset valves on every restart. A typical material charge phase will allocate the header, reset the totalizer, close all valves on the header, open valves as necessary on the header, start the pump and begin monitoring the totalizer, valve positions and pump status. If the phase goes to Hold, then on restart, the phase should follow the same sequence as the initial start without allocating the header and resetting the totalizer. Instead of programming the restart sequence in the Restart Logic area of the block, include a Restart bypass on the header allocation and totalizer reset and rerun the phase Run logic from the beginning. That way theres only one logic set to maintain in the phase.
- Delay reading and writing report parameters. Many phases write report parameters at the end of the phase to track actual charge amounts versus setpoints, etc. If the phase does this, its best to delay a few seconds after the charge is complete before obtaining the final totalizer value. This will capture any dribble flow.
- Add lots of phase messaging. Theres nothing more frustrating than a batch control system that lacks phase messaging or has useless phase messages, such as Phase on Hold. It doesnt take much effort to add lines in the phase to indicate whats going on as the logic proceeds, and its critical that the phase logic tells the operator why it went to hold. Youll get fewer 2:00 a.m. calls if you give the operator tools to troubleshoot and correct his problems!
- Keep phase programming simple! A large, unwieldy phase may be a logic masterpiece, but make sure its not a nightmare to troubleshoot and modify.
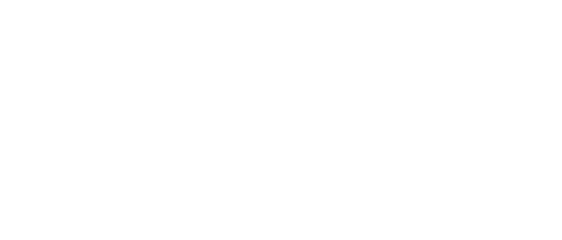
Leaders relevant to this article: