Is the two-wire hurdle going to hold back wide applicability of discrete devices in fieldbus? Clearing the hurdle of two-wire technology—having power and signal on the same pair, or at least the same cable—is an obstacle for many instruments. Coriolis, magmeters, pH, and similar measurements usually require “four-wire” solutions, which was true even before fieldbuses became available for process control. In most cases, we grudgingly accept four-wire solutions because we have little choice, if we want to get the benefits of, for example, a Coriolis flow measurement. But what if that flow was a “critical” measurement? What are the alternatives for that “other” pair?
The beauty of a “loop” or segment-powered device is that you can do all your work for robustness back in the house. You can have redundant power conditioners connected to auctioneered DC supplies, which in turn ride on redundant UPS, if you have the money and the space. You can even get fairly decent diagnostics and fault tolerance on all the components in the chain.
But what do you do about the four-wire device? Do you run UPS all the way out to it? Do you have little satellite, dual-auctioneered DC power boxes? UPS circuits, like any AC circuit, at some point can have so much cable that the 20-amp breaker in the house panel is no longer effective. And, if you have little satellite, diode-auctioneered DC supplies, how do you determine when one needs maintenance? If their failures go undiagnosed, are you any better off?
Thankfully, fieldbus signal diagnostics are comprehensive enough that surviving a “bad” measurement from Coriolis or pH is usually manageable. Most host systems that support fieldbus also can propagate signal status—although some more innately than others—which in turn can at least ensure that no control valve goes full-open or full-shut.
The two-wire hurdle becomes more of a barrier when you seek to apply discrete quarter-turn actuators using fieldbus. To use segment power and achieve an elegant two-wire solution, current offerings have to use a “piezo” solenoid, which can turn air on and off while consuming little power. They have some disadvantages, however, the most glaring is that their tiny orifices and flow paths can plug easily. They also have “memory,” and so they’d rather not sit around energized for many months, which is normal practice in process plants. They also don’t like it when it gets cold.
Nearly all makers of fieldbus-capable, two-wire, discrete positioners have addressed this “memory” issue. We who use them can attest that the present time is much better than the early days, but we’re still concerned, for example, about what can happen after two years. Has anyone had a piezo-actuated solenoid energized for two years straight? Let us know if it closes. We don’t have any that have been “on” for that long, but I haven’t seen any exhibit the “stuck on” behavior we saw in the early offerings.
The plugging issue also is fixable. Users can install an in-line sintered filter, or the manufacturer can make it integral.
However, we’re most concerned about the cold issue. While not a huge worry for users in East Texas, California, or the Persian Gulf, a low-end temperature rating of 10 ºF or more isn’t going to cut it in many places, such as Canada, most of the Eastern U.S., and continental Europe. So far, only one supplier has a two-wire package that has reasonable temperature specs for our climate in western Ohio. We’ll be testing that package this coming winter.
The alternative—using a separate DC power source for the solenoid—brings forth all the issues discussed above. In this case, we’re dealing with a final element, a valve, where our automation system interacts with the physical process. So, the forgiveness afforded by thoughtful fieldbus and device diagnostics on the sensor/measurement end of the loop are too-little, too-late on the valve end. When it fails, in all likelihood the process is impacted immediately as the actuator drives to its fail position, or even worse, if it fails to go to its fail position.
If I have to run a separate pair out for power, why not just use a conventional discrete output point? In my mind, it’s easier and more robust than trying to achieve the same integrity on a field-originated DC power system. Am I going to install satellite UPS systems also? We tried this on some critical analyzers (yes, analyzers) used in a SIL 2 shutdown system. That power scheme has been replaced and I would discourage others from imitating what we did.
Four-wire technologies have serious issues for critical final-element applications. Existing two-wire solutions for solenoid-actuated valves also are less than ideal. As users consider candidates for their fieldbus projects, we need to encourage our suppliers to strive for the robust two-wire technology we apply happily elsewhere.
About the Author |
Latest from Home
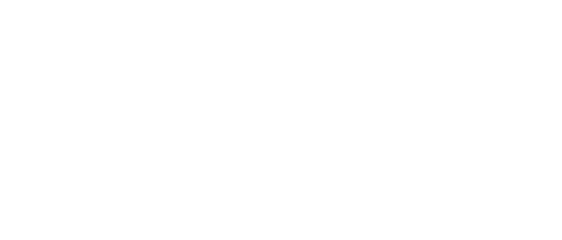
Leaders relevant to this article: