AND THE number one reason to migrate your control system: “(1) You need to update your collection of hats and jackets.” Well, so say the ControlTalk Boys, Greg McMillan and Stan Wiener. Ah, but is that new collection of hats and jackets worth the hard work of determining when and how to upgrade your control system, and whether to go with your current vendor or seek a new one?
Once upon a time, you installed a shiny new control system for your plant. You loved it, and it worked pretty much as you expected. Over time, though, just like your car, you’ve seen new models, and those new models had features and functions that you’d really like to have, and that can’t be found in your current system. Just as with any product, the further you get away from the warranty period the higher the failure rate, and the faster the failure rate grows.
Eventually, parts become difficult to obtain, and very pricey, if you can get them at all. The vendor tells you the product is so old that it isn’t officially supported anymore. Now management tells you that they want you to connect your control system to the business enterprise. You call your vendor, and they laugh at you.
”Migrationitis”
If this sounds like your predicament, you aren’t alone. You have a new end-users’ ailment called “migrationitis.” You now have to figure out how to migrate from your existing system to a new one, select a new vendor, possibly select a systems integrator to do the work, and make sure that you neither lose data and functionality you have now, nor cause the plant to shut down while you make the changes necessary to migrate your system.
“We found that our analog turbine control system was one of the top three causes of trips and transients,” says Marlon Dempsey, instruments and controls engineer for Duke Power’s Oconee Nuclear Station (Seneca, S.C.). “This was primarily because its components presented a single point of failure.”
During the 1990s, consolidation of the automation industry’s vendors made the situation even more difficult for end-users, especially when it came time to upgrade their control systems. Some systems were basically red-headed stepchildren to their new vendor-owners.
Roger Bailey, head of ABB’s systems business, is blunt about the issue. "To be honest," he says, "until System800xA was introduced last year, I think many of our employees were reluctant to admit that the Mod, Harmony and other products were really ours because they didn't know how we were going to handle legacy systems.”
It took a significant management shakeup at ABB to solve this problem. Bailey says of ABB’s staff, “Now they know, and I think you’ll see a change." And not a moment too soon. End-users like Wintershall, Germany’s largest crude-oil producer, were being courted and wooed away, because of the ease with which ABB’s competitors could apply FUD (fear, uncertainty and doubt).
Other vendors haven’t been as publicly forthcoming as Bailey, but most large system vendors and even a few second tier suppliers have had similar issues. One major software control system has changed ownership three times since 1990, and changed its name twice.
Migration Road Paved with Good Intentions
Dinesh Paliwal, president of ABB Inc. and global head of ABB’s automation business, said in early 2005, “60% of all potential systems business is upgrading and migration in ‘brownfield plants.’ ” If ABB understands this, you can bet the other vendors do too. At the Honeywell Users Group (HUG) meeting in June 2005, Kerry Sartain, of Georgia-Pacific, co-chair of the User Input Subcommittee (UIS) told CONTROL that one of the most valuable things the HUG has done has been to keep Honeywell focused on producing deep and detailed migration plans from older TDC systems to the latest Experion products, (See Figure 1). “It isn’t enough to say we can migrate from a TDC2000 to an Experion PKS,” he said. “The details have to be clearly worked out as well.”
The operators' console may be the pretty part, but it is what is between the console and the field instruments that makes or breaks an upgrade.
Back in the day, Honeywell’s Geismar, La.-based properties were part of Allied Chemical. Now that they belong to Honeywell, it appears that migrating from legacy systems to Honeywell’s Experion PKS systems is gong swiftly and simply. Earlier this year, Honeywell Geismar’s hydrofluoric acid works replaced a 1990s legacy system with a new Experion DCS system in 24 hours, using the facility’s existing wiring. In addition, since Honeywell also makes security systems, as Bill Lessig, Geismar’s plant manager, showed in his presentation at HUG, it was simple to interface the control system to the plant security system and the plant safety system. The point of Lessig's talk was that the integration of process control, building automation, and security systems was the driver for his project. Integration is the key, he noted, because it offers:
- Risk reduction,
- Better preparedness,
- Proactive response,
- Lower total cost of ownership (TCO) due to having one vendor,
- Easier training, and
- Cost savings due to the ability to share data.
"It may not seem like it, but it is an extremely powerful tool," Lessig adds.
…Except When It’s Not Easy
Duke Power had a much harder choice, since the existing controls were provided by GE, the continuing vendor of its turbines. When GE announced it was phasing out support for its analog control systems, Duke Power had no choice but to look for another vendor. GE offered Duke digital control options, but after a thorough review, Duke chose a redundant control system from Invensys Triconex. “The controller is triple-redundant,” Dempsey says, “so we no longer have a single point of failure.”
Dempsey goes on to describe an important new benefit. “And the box is qualified with the Nuclear Regulatory Commission (NRC) as a safety-related application that can help keep core from melting if there’s a problem. This is several safety levels above what is required for turbine control, but when you consider that the turbine can trip the entire plant, it makes sense to go for the highest quality,” he says.
Sometimes it’s far easier to stick with the controls vendor you have. Dynea UK Ltd. (Mold, Flintshire) upgraded the control system for its urea-formaldehyde (UF) resins and adhesives process. For example, Dynea chose ABB for the new system, based partly on its strong relationship with ABB and, previously, Alfa Laval, which supplied the original SattCon system on site.Rick Hirons, Dynea’s plant engineer, says, “We worked with Alfa Laval for 10 years, and in all that time, we never had a problem. Because ABB is using the same engineers, we were happy to award them the contract to update the SattCon system.” Dynea found that ABB also had features that they needed. “One of the major benefits of the ABB system is that it includes batch management software,” Hirons says. “This allows Dynea to produce a more consistent product based on the ability to call up stored recipes.”Another important consideration for migrators is how to maximize the value of the existing installed infrastructure. Dynea, for example, is interfacing all its existing HART equipped field instruments and control valves to ABB’s new control system. This will allow Dynea to use other new plug-ins to the ABB system, such as alarm management systems, computerized maintenance management systems (CMMA) and asset management systems (Maximo, Mettler-Toledo, Matrikon), without having to convert or replace field systems and wiring to Foundation Fieldbus or another digital field wiring system.Don’t Forget the Second TierAs our senior technical editor, Rich Merritt, pointed out in his recent article (“Second-Tier Systems Replace Legacy Controls,” CONTROL, Dec. ’05), it is often far less expensive to upgrade with a second-tier controls supplier than to stick with the Big Boys.In another article, (“Choosing an Enlightened Control Path,” CONTROL, Jan.’05), plant manager Yin Zuwei reported on Wuxi Dong Tai Fine Chemicals Ltd.’s upgrade from analog standalone loop controllers to a modern distributed control system. “The bids we received were all for small to medium-scale solutions,” he wrote, “such as ABB’s S900, Honeywell’s Plantscape system, DeltaV from Rosemount (sic) and MTL Open System Technologies’ MOST Matrix system.”“We selected the Most Matrix system,” he continued. “We found the system we selected was comparatively cheaper than the DCSs from other companies, especially in Division 2 areas.” Yin Zuwei isn’t alone.So, What’s an End-User to Do?
Everyone we talked to said much the same thing. First, take control of your existing system, and clearly define the upgrade goals and objectives. Then determine your migration strategy. Then, and only then, start the vendor selection process, knowing that you have the upper hand. As ABB’s Dinesh Paliwal notes, “It is far cheaper to keep an existing customer than to find a new one.”
Latest from Home
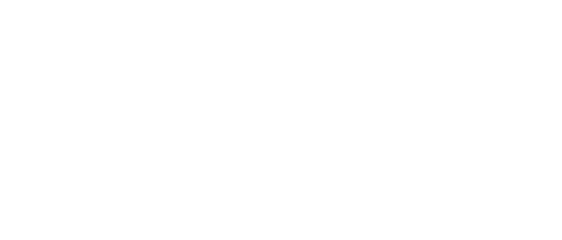
Leaders relevant to this article: