By Mike Spear, Editor-at-large for sister publication Chemical ProcessingINCREASING PRICE competition is forcing chemical companies to reduce capital and operating expenditures, and, of course, do it without compromising their plants reliability and performance. Easier said than done, perhaps, but the New Sampling/Sensor Initiative (NeSSI) for delivering process samples to analyzers can help make it happen. Since it began about five years ago, NeSSI has driven the move to modularize and miniaturize process sampling systems. Presently operating under the Center for Process Analytical Chemistry (CPAC) at the University of Washington in Seattle, NeSSI started as a group of equipment manufacturers and operating companies. The group initially sought to build on a standard for modular, surface-mounted systems in the semiconductor industry. It was modified for use in the oil, chemical and petrochemical industries by the SP76 working group of ISAthe Instrumentation, Systems and Automation Society. In 2002, the resulting design became the basis for the international ANSI/ISA-76.00.02 standard for sample flow control, conditioning and analysis. This modular standard basically requires compliant sampling systems to consist of a series of close-coupled, 1.5-in.-square manifolds, each carrying one of the components fastened to the substrate with four hex (Allen wrench) screws. Saving Sugars Cubes
NeSSIs potential savings were first quantified in 2000 by an ExxonMobil team, which reported that plants switching to NeSSI could save 40% on their sample transport and conditioning system, and eliminate the need for climate-controlled housings. It also projected a 35% savings by reducing sample volumes, as well as carrying and purge fluids, and by requiring less maintenance and support.After the field experiences with Generation I NeSSI systems, we now have a solid platform to build on, says Jeff Gunnell, lead specialist for process analytics with Scotland-based ExxonMobil Chemical. There has been one round of iteration [in design] since 2001, and these systems work fine in the field within a realistic operating window. ExxonMobil has 30 modular systems installed, including two sites in Baytown, Tex., and one in Sarnia, Ontario, Canada. These systems sample hydrocarbon process streams, and are approaching Best Practice approval status at ExxonMobil. Were considering them for some major projects, and that could mean huge numbers of systems, adds Gunnell.ExxonMobil adds its modular sampling systems come from two of the three main vendors supplying substrates and other flow components for ANSI/ISA-76.00.02-compliant systems. These are the Instrumentation Division of Parker Hannifin, Swagelok, and Circor Instrumentation Technologies.
FIGURE 1: UP ON BLOCKS
NeSSIs potential savings were first quantified in 2000 by an ExxonMobil team, which reported that plants switching to NeSSI could save 40% on their sample transport and conditioning system, and eliminate the need for climate-controlled housings. It also projected a 35% savings by reducing sample volumes, as well as carrying and purge fluids, and by requiring less maintenance and support.After the field experiences with Generation I NeSSI systems, we now have a solid platform to build on, says Jeff Gunnell, lead specialist for process analytics with Scotland-based ExxonMobil Chemical. There has been one round of iteration [in design] since 2001, and these systems work fine in the field within a realistic operating window. ExxonMobil has 30 modular systems installed, including two sites in Baytown, Tex., and one in Sarnia, Ontario, Canada. These systems sample hydrocarbon process streams, and are approaching Best Practice approval status at ExxonMobil. Were considering them for some major projects, and that could mean huge numbers of systems, adds Gunnell.ExxonMobil adds its modular sampling systems come from two of the three main vendors supplying substrates and other flow components for ANSI/ISA-76.00.02-compliant systems. These are the Instrumentation Division of Parker Hannifin, Swagelok, and Circor Instrumentation Technologies.
In Swageloks MPC system, devices, such as valves, mount on substrate modules containing specialized channel and flow components.
All three companies report theyre making inroads into the process analytical market, and claim doubling sales each quarter. There is a consensus that NeSSI has arrived, says Dave Simko, Swageloks marketing resources manager. Companies using NeSSI systems have shown that the cost savings are real. Although component cost is higher, savings in design time and manufacture generate 30% net savings.Swageloks Modular Platform Components (MPC) system (See Figure 1 above) consist of fluid-control components, including shut-off, needle, metering, toggle and check valves, and filters, which are mounted on a substrate layer of 1.5-in.-square modules containing specialized channel and flow components.
About the Author |
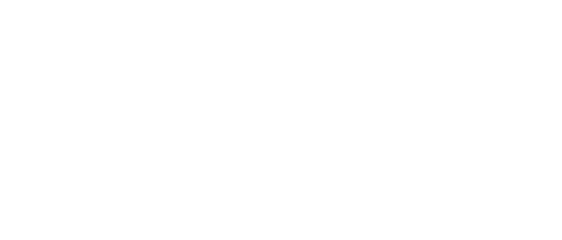
Leaders relevant to this article: