When it costs less to replace a legacy system than it does to maintain it, that legacy system is history. So it was in Upstate New York. The Water Resource Department in the town of Tonawanda, N.Y., just north of Buffalo, operates and maintains hundreds of miles of water and sewer lines. Each year millions of gallons of water drawn from the Niagara River are treated, distributed, collected and cleaned to serve the townĀs 80,000 residents.Ā
Software from Iconics replaced software from Intellution when the cost of supporting the legacy system got too high.
Windows Woes Cured at Canner
The legacy control system at McCall Farms in Effingham, S.C., was based on ĀwhiteboxĀ PCs and an older Microsoft Windows 95 operating system that was no longer supported by Microsoft or the control system vendor. It tended to ĀcrashĀ when operators entered production line changes, causing process data to be lost and production to stop. Legacy systems that crash usually get replaced.
McCall Farms produces a variety of canned fruits and vegetables under the Margaret Holmes brand, and distributes them throughout the southern U.S. in major national retail stores and major supermarket chains. Its canning process is continually moving with minimal allowances for equipment downtime and wasted product. Plus, according to a McCall Farms mandate, all products must be canned within ten hours of harvest.
The canning process starts with fresh fruits and vegetables bought from farmers across the southeastern U.S. Each type of produce has its own unloading area where it goes through a series of wash tanks for thorough cleaning before being sent to a blancher.
St Johns River Power Park (See Figure 3 below), located on a 1900-acre site in northeast Jacksonville, Florida, is a coal-fired generating station owned jointly by Jacksonville Electric Authority (JEA) and Florida Power & Light Co (FPL). It has two 640MW units, each with a Foster Wheeler drum boiler and a General Electric tandem compound steam turbine-generator. The plant uses a variety of domestic and foreign coals, as well as 20% petroleum coke.
Legacy control systems at Units 1 and 2 at St Johns River Power were both upgraded.
Even the biggest PLCs can run out of steam, and need to be replaced or upgraded. At Bonlac Foods Ltd., a food processor in Tasmania, Australia, a PLC-5 was running at its capacity, and could not expanded to handle more equipment. Bonlac processes milk arriving by tanker from dairies and produces a range of powdered milk products. The plant was controlled by a network of Allen-Bradley PLCs communicating with each other via a DH+ link. The plant also has a number of large Profibus valve networks.The wet process area was originally controlled by a PLC-5/80E that was out of memory and I/O capacity. The ladder program consisted of over 12K rungs of ladder code, comprising control of drives, valves, 17 PID control loops and 200 control sequences. All these were controlling routing and cleaning of milk lines and silos, where each line must be rinsed, caustic washed, rinsed, acid washed and rinsed again before use.The plant required the addition of 30 more Profibus-linked valves and associated equipment. Since the existing PLC-5/80 --the largest Allen-Bradley PLC-5 model-- was completely full, no simple expansion was possible. After reviewing the possible upgrade/replacement options, including adding another Allen-Bradley PLC and dividing the logic between two controllers, SoftPLC was chosen. The SoftPLC offered the choice of a drop-in large capacity single PLC replacement that would easily interface with all the existing equipment, networks, PLC controllers and Citect SCADA system. Another huge advantage was that the configuration of all the other equipment did not need to be changed in any way.Ā Using tools supplied by SoftPLC, the Allen Bradley ladder logic was imported to SoftPLC with minimal user intervention. Then, the new 30 Profibus valve controls were added to the system, along with the existing seven racks of SLC-500 I/O. The system was upgraded with minimum disruption to the process; in fact, the plant continued production throughout the upgrade. From Homebuilt Controls to PLCs
Exopack is a manufacturer of plastic bags located in Tomah, Wisc. Its production line evolved over the years, using a variety of different equipment and controls. The setup to run a new product was very time consuming and wasted a lot of bag material. If the line was stopped, it was difficult to restart and wasted more material in scrap. Industrial Automation, a systems integrator in LaCrosse, Wisc., was asked to come up with a solution to consolidate the varied controls and make the line easy to setup and run.The bag making process starts with large pre-printed rolls of plastic film. The web is threaded from the stock roll over a pressure sensing roll and then to a web guide and folding device. After leaving a folder, the folded material enters a fin seal system where the open side of the web is heat and pressure bonded. The seal is inspected as it leaves the fin sealer and defects are marked with an ink spray unit. The web then travels through the first nip roll and dancer system, and is directed to the bag gusset forming sections of the line. Here the bag web is rotated 90 deg. as it proceeds to the gusset forming section. To facilitate the twist, the bag web is filled with air that is trapped between two web nip points. Near the end of the bag twist section the bag sides are heated and then the bag pleats (gussets) are formed on either side of the bag tube. Upon leaving the gusset section final nip the bag web is again collapsed with gusset folds formed on both sides of the web. Next in line is the pull roll nip and drive system that is used to pull the bag stock tube to this mid point in the production line. The auxiliary equipment section includes a mixture of electromechanical devices that create the gusset tacks, corner tacks, and vent holes in the bags.Ā This system requires eight temperature controlling PID loops. The last section of the production line is the bag bottom seal and cutoff machine. This machine serves as the master speed and timing reference for all upstream devices. Freshly cut bags exit the machine by a conveyor that empties to a second perpendicular conveyor for bag stacking. By manipulating the exit conveyor speeds, good exiting bags are stacked in groups of 10. Any bags identified as defective earlier in the process are stacked together with different conveyor spacing.ĀBecause the production line is very long, and required many PID loops, we chose to divide the control system into two control enclosures,Ā says Herb Burfield, manager of Industrial Automation. ĀWe used two Automation Direct D2 PLC systems to control the line, a 10-in. EZ-Touch touch screen as the primary point of operator interface, and a 6-in. EZ-Touch touch screen as a secondary point of operation.ĀThe primary HMI includes operation prompts, alarms, setup screens, maintenance screens, device test screens, and graphical history display screens. The secondary HMI contains normal run operation screens and limited device setup screens. The end result of the above applied automation is a production line that can be setup and run from a cold start in minutes with very little scrap material. ĀPreviously, startup could occupy most of a shift and waste rolls of material,Ā notes Burfield. ĀOnce started, the line can now be stopped and restarted at will without creating any scrap. Depending upon product the production speed is 30% to 50% faster than possible prior to the automation and bag quality and consistency is improved.ĀLegacy DCS to Redundant Controls
Crawfordsville Electric Light & Power in Crawfordsville, Ind., wanted to replace its legacy Bailey Network90 DCS because it was old, parts were hard to come by, and it could not support CEL&PĀs increased need for operation and performance data. CEL&P called upon Advanced Boiler Control Services in Orland Park, Ill., to help them put together an integrated system to control two 21 MW turbines. They decided to install a fully redundant Matrix control system from MTL-Most.The Matrix system has a backup controller for redundancy, connects to third-party devices via Modbus Ethernet TCP/IP, and uses a Wonderware system for the HMI and plant historian. An integrated, centralized development environment in Matrix coordinated control engineering development for process control and IEC 61131-3 programming languages, including design implementation, documentation and maintenance. Project documentation is automatically maintained in an as-built state from the initial engineering phases through subsequent system modifications.
Latest from Home
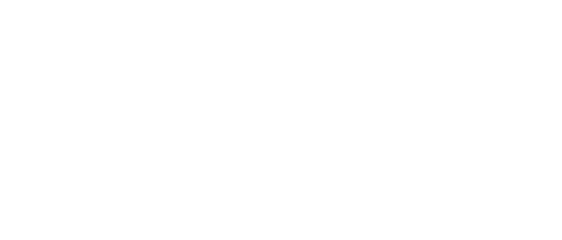
Leaders relevant to this article: