As trends emerge more clearly, we usually can find a few early adopters to help define accompanying benefits. Ian Drazin is electrical and instrumentation supervisor at Potlach Corp., which produces coated printing papers, bleached paperboard and private-label tissue products in North Las Vegas, Nev. Drazin says Potlach went wireless four years ago in its warehouse and production area, primarily to control fork trucks, but he couldnt leave well enough alone.I began redesigning our DH+ and Ethernet networks, connecting them to a field-mounted Allen-Bradley gateway, says Drazin. Once complete, I connected the company LAN to the gateway. Now, from my office, I can route communications through the gateway and gain access to my PLC processors. To make it better, I then coerced my IT department to install 802.11b wireless PCMCIA cards in our maintenance laptops. Armed with such a tool, I could connect to the PLC via my laptops wireless connection and walk up to the equipment I was working on and see input/outputs in real time.Drazin enjoys many benefits from this system, including wireless Internet access. Many equipment manufacturers finally are making comprehensive product information available on their websites, he notes. Maintenance personnel save time if they have immediate access to product drawings, specifications, user manuals, set-up procedures, etc.Joe Markham, control engineer at biopharmaceutical manufacturer Protein Design Labs, Brooklyn Park, Minn., uses industrial Ethernet in his process development group. We have a number of PLCs, operator interfaces and PCs connected via Ethernet, he reports. Ethernet is fast, especially compared to going via serial port out to a KF2 box, and onto DH+. Also, with Ethernet we can leverage the business infrastructure. We have our switches configured, so only selected engineering people can access the control system Ethernet LAN via the business LAN. This lets the engineers connect to the control system components from anywhere, while keeping the LANs isolated.
|
FIGURE 1: HIERARCHY OF INDUSTRIAL CONTROL NETWORKS
One way to gauge the success of a technology is to note how many new products use it. While every product now comes with an Ethernet port, many also come with a Modbus port. Similar to the legendary phoenix, Modbus is rising from the ashes of the destruction that killed off many other networks that first saw light in the 1970s.Why would a clunky network from the Dark Ages of control remain so popular? Bryan Moore, product manager at ABB, says Modbus probably will be around forever. It doesnt require special electronics, any PC or PLC can run it at the serial port, its very low cost, and it supports 256 stations, says Moore. Thats a lot, compared to a DeviceNet or Profibus network.Yes, its slow. But that means it can cover long distances, Moore explains.Yes, its rudimentary. But it has become a least common denominator, adds Moore, like the RS-232/serial ASCII connections of the past. You can always interface to it. Chances are, if you have any old control equipment or instrumentation in the plant, it probably has a Modbus interface. WHAT ABOUT WIRELESS?
Jumping from one of the oldest network technologies to the newest, lets look at wireless. Although some users are wary of wireless, it has taken center stage in the industrial networking theater. Sales are still at entry levels for a new technology (about $75 million in 2003), but market researchers predict good times ahead.Venture Development says the market will grow about 35% annually, reaching $183 million in 2006. Frost & Sullivan projects that wireless sales will quadruple by 2006. A recent IDG. World Expo report goes even further, predicting that the wireless sensing technologies market (including sensors) will be greater than $10 billion by 2010.Many big vendors are jumping on the wireless wagon. The HART Communication Foundation is adding wireless capability to its HART devices, and all the major control vendors are keeping an eye on what wireless is going to mean to process control and automation.Gene Chen, product manager at Honeywell says that Honeywell is an executive sponsor of the three main bodies trying to define a wireless industrial standard. These include the Wireless Industrial Networking Alliance (WINA), ISA SP100, and ZigBee, a consortium of component-level OEMs. Gene Sierra, wireless marketing manager at Emerson Process Management, says that Emerson is working with HART and ISA.Hesh Kagan, director of new technology marketing at Invensys Process Systems, says motes (wireless nodes) and mesh networks are coming. At the low end, wireless sensors use mesh networking with auto-adaptive, self-healing capabilities, says Kagan. Companies such as Millennial Net and Ember are driving standards-based end nodes, radios on a chip, mesh-networking software, gateways and development environments.Venture Development says its data agrees. It reports that mesh networks will grow from a miniscule $6 million in 2004 to $25 million in 2007, a growth rate of 60%.Kagan sees tremendous opportunities for wireless sensors in process applications. Most process plants today take measurements at only about 10% of the possible points. But if the attachment and sensor costs were low enough, as mote technology promises, you could measure at many more points, giving you a much richer process model with which to work.The biggest issue in wireless appears to be the lack of a universal standard. Three groups are working on it: WINA, ISA and ZigBee. Not having a single backbone slows down adoption, says Honeywells Chen. Several cases exist where customers spent resources to deploy wireless networks to support tablet PCs for operators, but found the network wouldnt support wireless sensors. Other customers had the opposite problem when they installed wireless sensors.According to Venture Development analyst Jake Millete, ZigBee looks promising, but vendors are sticking to their proprietary methods. Many vendors feel ZigBee is an excellent solution for a variety of applications, notes Millete, but for industrial applications where a robust network is essential, some develop their own mesh networks. Well see many more ZigBee-based solutions in the industrial market as the standard matures.This trend will have to solve another problem first. Power is a big issue. Wireless device-level network and sensors have yet to take off due to limitations of battery technology and lack of standardization, says Jonas Berge, marketing manager at Smar. Unlike wireless consumer devices such as mobile phones or PDAs, sensors cant have their batteries charged or changed every week. Conserving battery power is therefore very important. Because of the power problem, wireless sensors often transmit less often than wired sensors, and at slower speeds. As a result, wireless sensors are not suitable for control or functional safety, says Berge.Slow response also happens when too much wireless traffic occurs nearby, so the sensor has to wait for the frequency to clear to transmit. No one wants to base a real-time control decision on inputs from a wireless sensor. For the immediate future, it appears that wireless will be limited to monitoring. (See this articles sidebar for a solution to both problems.FIELDBUS FORGES AHEAD
The October 2005 issue of CONTROL includes an account of a mammoth Foundation fieldbus project in SECCOs ethylene cracker complex in China. The DeltaV system from Emerson Process Management involves 10,000 fieldbus devices in 10 plants with 48,000 loops and 166,000 I/O tags. All PID control is performed in fieldbus instrumentation, and overall control and supervision comes from a central control room, where workstations run asset management, loop tuning and maintenance diagnostic software. The installation demonstrates the control capabilities of fieldbus, its ability to handle giant systems, and shows that it actually works.Meanwhile, standards organizations are working hard to make fieldbus easier to use. Of greatest interest are Electronic Device Description Language (EDDL) extensions, says John Yingst, fieldbus systems product manager at Honeywell. This enhancement will provide a common means for device vendors to specify and interact with complex data such as valve signatures. EDDL has the support of the Fieldbus Foundation, HART, OPC and Profibus organizations, and EDDL is expected to make it easier for vendors and end users to implement all kinds of fieldbus instrumentation.Fieldbus systems have been way ahead of the current trend toward remote diagnostics. On-line diagnostics available with Profibus include a status byte incorporated in the transmission of process variable data, explains Fabian Monino, senior applications engineer at Siemens Energy & Automation. This permits a control system to evaluate data and perform alarming if necessary.Fieldbus also can be used in hazardous areas, but it is not considered a safety system, says Yingst. Significant changes would be required to adapt the FF protocol to the requirements of a safety standard. There is an ongoing effort to define a workable Safety Instrumented Systems (SIS) specification. Berge agrees. There are plenty of safety buses for the machinery/factory automation world, but nothing for process, he notes. FF-SIS is under development and already has TÜV concept approval.In addition, Pilz has successfully integrated its PSS safety network with EtherNet/IP, ControlNet, Profibus and Interbus, and it developed a safe fieldbus technology of its own, called SafetyBus p. Lee Burk, training and consulting manager at Pilz, says the Ethernet protocol can be used, but Pilz believes a separate fieldbus should be implemented for communication of safety related signals.
"Supported by the Fieldbus Foundation, HART, OPC and Profibus organizations, EDDL is expected to make it easier to implement all kinds of fieldbus instrumentation." |
Ethernet is probably the most popular network in the world, thanks to its long life and use by all WinTel (Windows/Intel) systems. Just about every industrial network has an Ethernet version, including Foundation fieldbus (HSE), Profibus (Profinet) and our old friend, Modbus (Modbus TCP/IP). Various Ethernet hardware is used by big vendors such as Emerson, Rockwell and Omron. All the various protocols can run on the same Ethernet cable at the same time, and OPC Data eXchange software lets various Ethernet devices read the other protocols.Without OPC, connecting various Ethernets is a problem, because there are so many. Its important that users understand the differences between standards-compliant networks and standards-based networks, says Doug McEldowney, Netlinx strategic marketing manager, Rockwell Automation. Standards-compliant networks, like Ethernet/IP, HSE, and Modbus TCP/IP use existing, unmodified networking components and networking standards to define their solution.Berge puts it more bluntly: If the product specification just says Ethernet or TCP/IP without specifying the application protocol, you can be certain it is proprietary. Every vendor is jumping aboard the Ethernet train, and for good reason: it is dominating the industry.A major factor pushing Ethernet lower in the factory is the increasing use of remote diagnostics and remote monitoring. As a recent Control Design web poll indicates, 47% of machine builders are incorporating web-based diagnostics. At a minimum, products connected to Ethernet provide some level of diagnostics about the product and/or system via Web servers today, adds McEldowney. Also, the ability to leverage web services, in general, opens opportunities to connect dissimilar speaking devices within the enterprise. This area will continue to expand over time with more functionality being embedded deeper in the control systems.OPC is working in that area, too. "We expect to release the new OPC Unified Architecture (OPC UA) spec by the end of the year," says Lee Neitzel, Emerson Process Managements senior technologist and editor of the new OPC UA spec. "The new OPC UA will permit OPC to be used across the Internet. By early next year, OPC applications will begin to communicate seamlessly using Internet communications wherever they are in the world. This will be a significant advance in automation system communications." For users and OEMs, this will be another feature to add to the Ethernet steamroller. For competing networks, it may be another nail in their coffin.
With Wireless, Who Needs Networks?
HERE'S ONE SOLUTION to the power and speed problems with wireless proximity sensors that requires no batteries, operates as many times and as fast as needed, and suffers no delays or interference from other transmitters. Chris Jeffrey, business development area manager at ABB explains that several customers, including robotics, powertrain and stamping companies in the automobile industry asked his firm to help reduce their huge, ongoing costs associated with broken wires and worn/loose connections.Jeffrey says sensor cables are one of the most frequent sources of failure in factory automation. "One automaker was spending about $40,000 per month just fixing wires on one machine," he says. "Wires and connections on robot arms, portable assembly pallets, platforms and anything else that moves will flex and break connections on a regular basis." It sounded like a battery-powered sensor was just the ticket.Alas, replacing batteries, which never wear out on schedule, is just as much trouble as fixing wires. "If you have a machine with 50 battery-operated sensors, they all wear out at different times, depending on how often they are actuated," he says. Perpetually replacing batteries introduces a new maintenance nightmare. "Our wireless proximity switch design target was 10 years of maintenance-free operation, which ultimately means no batteries."ABB developed a system that uses an electromagnetic field inside or around the machine (see Figure 2 below) to power all these wireless sensors. Because power is no longer a problem, the sensors (see photo) can operate continuously at high rates. Each sensor has a wireless transmitter that sends on/off signals to a base station. "ABB uses standard 2.4-GHz radio transceivers in its sensors, such as those used in Bluetooth, but employs a tailor-made real-time communication protocol.FIGURE 2: ELECTROMAGNETICALLY ENCLOSEDPublish-Subscribe in Real Time
ANOTHER POTENTIAL network trend involves the newest real-time networking system for the WinTel platform: the OMG Data-Distribution Service (DDS). This is a publish-subscribe scheme that works with Windows operating systems. It hasnt exactly caught fire, but it shows promise in its ability to make WinTel systems more suitable for networking in an industrial environment.
Many real-time applications must model some of their communication patterns as a pure data-centric exchange where applications publish, supply or stream data, which is then available to any interested application, explains Gerardo Pardo-Castellote, Ph.D., chairman of the DDS Standards Committee and chief technology officer of Real-Time Innovations. These applications include industrial automation and distributed control. The lack of standards in this area forced application developers to use proprietary solutions or develop the infrastructure themselves. With the recent introduction of the OMG Data-Distribution Service for Real Time Systems, there are now COTS products that provide this infrastructure.
In a nutshell, this means the classic way of accessing data remotely in a standard WinTel system, using simple read and write instructions, doesnt work well in real time. An instantaneous response cant be guaranteed in an Ethernet LAN or WAN where computers enter and leave, and links have sporadic faults. The data-centric scheme in DDS, however, provides the performance, predictability and resource control required by embedded and real-time systems.
Kuka Controls recently announced the successful integration of RTIs version of DDS (NDDS) into its VxWin operating system. The combination allows Wind River VxWorks and Windows XP Embedded to run on the same host processor and share data with a publish-subscribe scheme. Operations are unaffected by Windows events, ensuring failsafe real-time operations.
RTI intends to market its DDS product into the industrial space. We will combine our NDDS with new tools for distributed system visualization, analysis and real-time debugging, says Stan Schneider, CEO of RTI. This platform will simplify design, ease development, and improve the quality and performance of real-time embedded systems in industrial automation applications.
Latest from Home
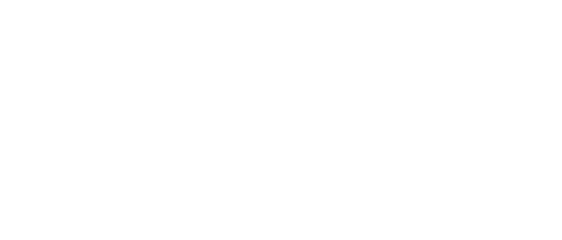
Leaders relevant to this article: