The SECCO complex near Shanghai in China comprises 10 separate plants, with a main ethylene cracker capable of generating 900,000 metric tons per year of feedstock.
Previously, SECCO decided that using an MIV approach would be best for the project. The MIV would work with SECCO to implement the automation and control systems, and help manage multiple international and local engineer-procure-construct (EPC) suppliers for each of the 10 plants.After evaluating several suppliers, SECCO selected Emerson Process Management for its breadth of digital automation, including field instrumentation and systems, and for its experience in managing large-scale projects. Emerson had excellent resources in China, and could call on its global resources, specifically from its engineering centers in India and Singapore, to supplement its local resources.Emerson and SECCO created framework agreements for all EPC contractors to use, enabling consistency across the site for current and future operations. This was vital to achieving SECCOs long-term goals of ease-of-use and reduced maintenance by making sure that every process in the 10 plants was developed consistently.
The complexs digital architecture integrates 10 of Emersons DeltaV systems (See Figure 3 below) with one global historian and remote operations functions. All 10 automation systems are managed from one centralized control room (See Figure 4 below), which is something that wouldnt have been possible without Foundation Fieldbus technology. These Foundation Fieldbus devices and systems provided several advantages, including openness and intelligent asset management. Because the most appropriate instrumentation was selected for each process, not all the devices were available from Emerson. The ability to integrate other suppliers devices really brought out the flexibility of PlantWeb with Foundation Fieldbus because this automation technology is designed around an open, standards-based platform on which industry-wide devices can participate.
Each of the 10 process plants has a Delta V distributed system with I/O, controllers,
and PlantWeb architecture that report to the central control room.
- Increased reliability and accuracy.
- More seamless, richer information, which eases troubleshooting and reduces resources required for maintenance. In fact, SECCO estimates that Foundation Fieldbus will cut its maintenance costs by approximately one-third.
- A means of preparing for the future. SECCO sees fieldbus as a leading-edge, quality technology with natural advantages, which will raise its standards and business practices, and help increase the complexs net profit.
While SECCO knew that a fieldbus approach would save considerable cabling, a conservative approach was taken to devices connected on each segment. Designs were limited to no more than 12 devices, and the average ended up as five devices per segment, where each segment varies between two to 11 devices.
In addition, Foundation Fieldbus enabled performance of basic PID control in the intelligent field devices. The choice was made to locate the PID algorithms at the point of final controlin the valve controllers. This control-in-the-field (CIF) provides the improved reliability of a truly distributed control system. CIF also reduces communication traffic between the automation system and the field devices, further increasing reliability.
Only single-loop control was implemented in the valves. All complicated control, such as cascade and multielement strategies, is done in DeltaVs digital automation system. Control function blocks can be performed in any of the field devices, or in the automation system, since it is an easy drag-and-drop software choice. This easy configuration will save time as we modify our ever-changing plant. In actual application, CIF was implemented with no major problems. The benefits havent been quantified yet, but long-term advantages are expected for the SECCO plant.
Asset Management
The complexs intelligent field devices also deliver process and equipment health information to the AMS Suite in PlantWeb. While SECCO is still discovering the benefits of its asset management system (AMS), it has already proven valuable in key areas, such as the AMS Suite Intelligent Device Manager. This enables range verifying inside the transmitter, while the user sits in the comfort of the control room. Likewise, the AMS ValveLink application is being used to obtain valve signatures, so SECCO can monitor valve status, act to optimize performance, and avoid abnormal situations.
These asset management capabilities will improve the lifespan of the complexs assets by enabling performance predictions, and allowing staff to prevent problems before they occur. For example, its possible to look at information coming from the intelligent valves, and understand changes in the friction coefficients to learn if theres a potential for leakage or early breakdown.
The predictive diagnostics of PlantWeb and AMS Suite will help optimize our maintenance plan, enable personnel to focus directly on problems, improve efficiency, and minimize downtime. Knowing what the problems are beforehand, the staff can schedule maintenance and obtain needed parts. Where there are no problems, the maintenance schedule can be revised to alleviate delays elsewhere. This is a clear advantage over traditional plants that may have to tear down and rebuild equipment every two years, whether or not it is needed.
Importance of Teamwork
The project team was able to meet and beat our projects aggressive schedule because of teamwork. The technical staffs had tremendous rapport, which helped complete the project efficiently and successfully. Emerson gave SECCO a lot of support in the negotiation process, adopting a relatively flexible strategy that allowed us to reach agreements with the various EPC suppliers and sign an extremely efficient MIV contract. Following that, Emerson also provided support during the engineering construction process, which allowed intimate coordination with the EPC suppliers throughout the project.
management and maintenance management software for all 10 plants.
About the Author |
Latest from Home
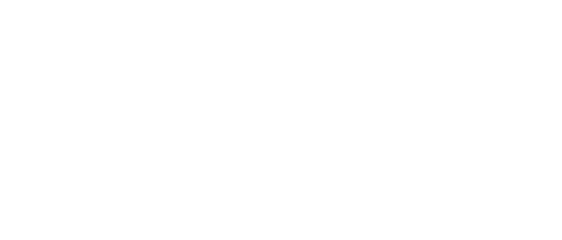
Leaders relevant to this article: