W |
hats the second thing you ask when you see a new piece of automation hardware or software? The first thing you probably ask is What does it do? Or, if you already know something about what it does, you might ask How does it work? Then the second thing usually is: How much does it cost? Its just human nature to ask the price.
When the buying decision is subjective as it is in personal purchases like a new digital camera or a new car, its priceis the right thing to focus on. But purchases of new technology for automation applications should only be for objectively estimated benefits. That means that for automation the better question is Will it deliver net benefits that exceed my companys hurdle rate? If so, it should be installed whether it costs $5,000 or $500,000; if not, then dont buy it.
We often ask the cost question to make a quick analysis of whether we will be able to get it approved. If a level of credibility does not exist in your company that allows new automation with good benefits to get approved, then you have some work to do. Of course there are some companies that will not spend any money on anything regardless of the benefit, but that is hopefully a temporary situation and at any rate that is a different story.
A Short History of Automation
Distributed control systems (DCSs) began to be installed in the late 1970s with most of the installations done in the 1980s. This was a Good Thing. Digital gave much better control than analog and the DCSs gave the operators much better tools to run the plant. This was such an obvious Good Thing that companies often did not require a specific, well-defined justification for their approval.
In many cases, the intent of replacement projects was to just duplicate the analog control functionality so as to not give the plant too much change too fast, but to allow improvements in the future. Most of these systems did deliver benefits that justified their cost, but they often delivered only a fraction of the benefits they could have. And those future improvements often never happened.
In the 1990s many companies realized they were not getting full value from their control systems. Monsanto did a key benchmarking study that showed fewer benefits from DCSs than did other leaders in the industry. The study resulted in more than 120 automation professionals working part time for several years to identify and achieve more than $60 million of new benefits annually with minimal capital.
"Automation projects can yield significant dividends enterprise wide. But returns should not be counted only in dollars and cents terms." |
You may well think you are doing something, but the question is whether you are doing all you can to develop new benefitsnot just doing what is needed to keep the plant running smoothly. There is a whole hierarchy of things we can do and we need to constantly move up on that hierarchy. At the level of maintaining the value from the control system, there are a series of things we can do. At the lowest level, we install the controls needed to run the plant in the initial plant design. After startup, we at least fix those things that are broken so badly that the plant will not run. It is even better if we diagnose equipment periodically and fix those things that are not meeting specifications or retune loops that are not performing well. Even better yet is to practice predictive maintenance so that even small changes in performance are automatically identified and corrected before they affect operations. Smart instrumentation and continuous loop performance monitoring is very good at doing these predictive functions; but for a company to really keep track of their equipment performance they also need a good asset management focus and system as well as a computerized maintenance management system.Virtually every manufacturing operation has opportunities for new benefits from automation and there are several types of activities that can focus on these new benefits. There is a long list of good things to do to improve operations. Often these are called best practices, since some companies that have done them have found that they improve operations (see Sidebar).While these types of best Practices have proven beneficial in some operations, there is no guarantee that they will deliver benefits in your operation and the justification case needs to be fully developed. To ensure that benefit, it is better to start with the benefit in mind. A good approach is to calculate and monitor key values so that it will be easier for automation professionals to determine how to identify ways to improve those key values (possibly using some of the best practices). This approach is known as Dynamic Performance Measure. Another good way to start with benefits is Opportunity Identification and Sizing. This approach identifies and sizes the gaps between current performance and best practical performance. The location and size of these gaps guide automation professionals to develop controls that can close the gaps. For example, if we are operating a unit at 95% conversion but know from occasional experience or laboratory studies that it is possible to operate at 97% conversion, the gap is that 2% of additional conversion and we can put a value on that. Or if we are sold out and know from occasional experience that it is possible to operate at 10% greater throughput than the average throughput we are achieving, then the gap is that 10% and we can put a value on that. Or if we have a 97% on-stream time limited by product changeovers or unplanned shutdowns, then what would be the additional value of operating at 100% on-stream time? If there are no real gaps, there is no reason to add new automation or even to have automation professionals working in the unit since there are no benefits possiblebut it is the rare operating unit that does not have a gap. In applying this approach to more than 100 operating plants, I have only seen one unit where we did not find a gap large enough to justify effort to try to close. With the value of the gaps identified, the automation professionals know where to focus efforts on improving controls. To close the gap you might need additional functionality in existing systems or you might need new systems upgrade of control system but you should always know where the opportunity is and how much.Note the difference between the Best Practices approach and the Opportunity Identification approach. Best practices starts with a solution and looks for a way to justify ita hammer looking for something to hit. Opportunity Identification identifies the opportunity and looks for a method to solve it. Ultimately, the two approaches may converge, but the opportunity identification approach is more efficient and effective.Second, Projectize Activities
Put activities into projects to get all the good management things that projects bring: prioritize against other projects for approval to ensure that the greatest benefits are being pursued; define objectives to maximize the focus of the work; develop measurement methods to ensure that you get what you are shooting for; have a good project definition before detail design is started so that the needs of all stakeholders are dealt with; phase the project so that things get done in the right sequence to minimize changes; rework staffing planning and emphasis to keep the project moving; track cost/schedule control to make sure that you stay on budget and get the project done in a reasonable time; plan for and deal with all the strange things that can and do happen.Third, Financially Justify All ProjectsFinancially justifying all projects is one of the best ways to ensure that the project is really focused on delivering new benefits. While virtually every operation has opportunities from new automation benefits, if you are doing things without a defined justification, you may be doing the wrong things and you may not be doing enough. Some automation professionals complain that their management does not understand automation benefits and will not approve any benefits until they are proven. That is a problem, because it is nearly impossible to prove something until it is installed. However, the methodologies for estimating benefits are well developed enough that good estimates can be made. Of course, every time that an automation professional fails to deliver on promises it fuels the distrust. Still, if only proven benefits can be approved, then the unit will miss out on big savings.Accounting personnel may also not understand automation benefits and often dont trust real-time data. Good real-time data will likely be more accurate than counting the number of trucks, so again, there may be some work to be done. Also marketing personnel may say that they want higher quality but are unwilling to commit to charging a higher price for it. So if there is no expected value from the higher quality then there will be no new benefits.Fourth, Partner
The surprising thing is not that partnering is so seldom done well, but rather that it is ever done at all. Partnering is very beneficial, but it is hard; and benefits usually take some time to appearmore time than management may be willing to wait. If partnering is not working for you, you need to ask if you have done what you should to support the partnering effort.Have there been discussions between the end-user company automation management and the supplier management to set objectives and expectations for the partnership? Have each of the partners assigned a person to manage the partnership and given them appropriate amount of time to do so? Do all of the participants in each company understand the objectives of the partnership and who in their company to go to for assistance with the partnership? Are surveys done on a regular basis to determine levels of satisfaction? Are the partnership managers really resolving issues, and are there regular meetings between the partnership managers?Fifth, Develop Professional Staff
Creating a viable cost-efficient automation system design is challenging. Not only is the scope of automation technology available extremely broad, but the technology is changing and advancing rapidly as well. In addition to the technical nature and ever-changing scope of the control technology landscape, automation professionals must often take responsibility for communicating with individual stakeholders and for the overall performance of the project. Few automation professionals (engineers) learn these technical skills in schoolin fact, professionals in automation have a more varied educational backgrounds than most any other technical discipline. Furthermore, because the automation and process control profession attracts people who are interested in becoming immersed in its complex technology, even fewer are prepared for the communication and leadership roles they must take on to manage automation projects successfully.In the past, most automation personnel learned their trade by working on the job in a junior role for some number of years and continuing their education by taking courses or training sponsored by the company and from technical societies, vendors and other providers. Today, as in most industries, cost pressures on both end users and suppliers have virtually eliminated on-the-job training; and far fewer courses are taken by individuals, except those specifically required to know how to operate or program a specific system. Benefits Even Harder
Delivering new benefits from an automation standpoint is even more challenging since it requires knowledge of identifying and estimating them and developing justificationsreally taking charge of the projectand a possessing a broad enough knowledge of automation to conceptualize the best technology to use.Certification is a way to help deal with these issues. While the basic role of certification is to ensure that people practicing the topic are qualified to do so, a major benefit is to motivate applicants to learn more. Certifications are everywhere today. Even the most obscure specialty in the medical fieldfor doctors, nurses and techniciansseems to have a certification program, and many of these are required by law or required by the hospital or by the insurance company to operate that equipment or to practice in that specialty. Some companies require that project managers hold the Project Manager Professional (PMP) certification. Worldwide, more than 80,000 project managers are PMPs. Outside the engineering and medical areas there are even more certifications. In contrast, designing mission-critical automation systems and designing safety systems to protect the environment and personnel rarely requires any certification or even any specific education. Many states have the Professional Engineer (P.E.) registration but in automation that is required only for some types of electrical design. To date, only a small fraction of automation professionals in the U.S. have a P.E. Some other countries have similar certifications but in most countries even fewer are certified than in the U.S. Regardless, a shift to use the P.E. as the certification for all types of automation work is not always practical. There are serious geographical and technical scope limitations with the P.E. relative to automation; and, because of the engineering educational requirement for the P.E., only a fraction of the people working as automation professionals today could qualify).A new certification developed by ISA, Certified Automation Professional (CAP), has the right scope to deal with these needs. It focuses not just on the broad technology of automation but also on the identification of benefits, justification and execution of the project.The best of best automation practices1. Replace control systems when they are obsolete (The term obsolete should really be retired because as long as a system will do the task it was installed to do it is not really obsolete; and systems can be maintained almost indefinitely at some cost to do that task. The real best practice is to replace control systems when there is a defined benefit to do so.) 2. Install smart sensors and valves in critical areas.3. Fix the control valves (Studies of control valve performance often indicate an average of more than one problem per control valve). 4. Tune your controllers and get them operating at the highest design level.5. Put advanced process controls such as model reference controls on unit processes that are difficult to control. (The book, Advanced Control Unleashed, is loaded with good things to do with advanced process control.) 6. Install an asset management system. 7. Install a scheduling system to optimize product runs and make changeovers faster. 8. Make data more widely and easily accessible. Install and integrate plant data with MES systems.9. Integrate plant inventory and production information with business systems. For supply chain scheduling, make to order vs. make to stock. 10. Install a work-in-progress inventory system using live data to give accurate real time cost accounting information. Improve ability to determine delivery dates. Install functionality to do equipment performance monitoring. 11. Standardize hardware, software, and communications across the company. Vernon L. Trevathan, P. E., PMP, has worked in process automation and project management for more than 40 years, mostly with Monsanto Co. in engineering and manufacturing management positions. He is an ISA Fellow. He currently consults and teaches in project management for automation; and he may be reached at [email protected].
Latest from Home
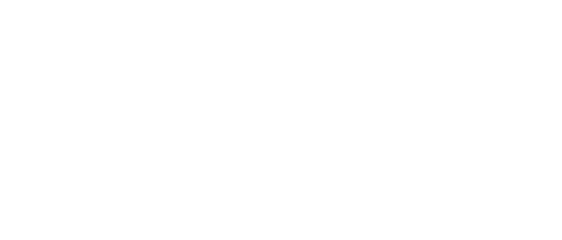
Leaders relevant to this article: