“My co-presenter, William (Butch) Taggart from Murphy Oil could not be here, because he’s cleaning up the damage Murphy Oil suffered from Hurricane Ike, and his own house,” said Emerson’s Sean McCormack, of the Emerson Hydrocarbon and Energy Industry Centre, in Calgary, Alberta, “so I’m going to do the presentation for both of us.”
Murphy Oil had experience with DeltaV for the basic process control system for several of their other platforms in the Gulf of Mexico, so when it came time to select a BPCS for the Thunderhawk platform, DeltaV got the nod.
The Thunderhawk Field is located in Mississippi Canyon Block 734 in the Gulf of Mexico. The Thunderhawk platform is a stand-alone semi-submersible floating production unit with an estimated capacity of 45,000 barrels a day with expandable capacity to 60,000 barrels a day.
Typically, on previous Murphy platforms, DeltaV has only been the basic process control system, with other vendors providing the Safety Instrumented System, or SIS, and the ESS, or Emergency Support System (the fire and gas safety system).
However, on some of the other platforms, Murphy had noted problems with the integration of the safety system with the BPCS, including unexplained and dangerous OPC failures, and they also had severe equipment footprint constraints on the Thunderhawk, because it is a semi-submersible platform.
So the decision was made to award Emerson all three systems: the Process Control System (DeltaV), the Process Safety System (DeltaV SIS), and the Emergency Support System (ESS) as a single vendor.
Currently, the Thunderhawk Project is the largest DeltaV offshore installation, and the first DeltaV SIS installation in the Gulf of Mexico. “There are 1400 I/O points and 103 Logic Solvers in the SIS system,” McCormack said, “and integration with the BPCS (Delta V) information is seamless. There’s no need to map data or use an OPC server to read/write between the PCS and the SIS. This, of course, provides easier integration between the BPCS and SIS and removes a potential point of failure that Murphy engineers were already concerned about.”
McCormack continued, “Using DeltaV and DeltaV SIS also allowed the engineering team to use the same easy-to-use engineering tools and operator interface for both the safety and process control system. And there was a significant cost saving associated with reduced footprint: fewer cabinets.”
“We were able to accommodate 448 installed and future I/O points with marshalling in one system cabinet,” McCormack said. “Crosswiring between cabinets is eliminated. We were able to integrate marshalling and I/O in a single cabinet with a footprint of 78”H x 32”D x 63”L.”
Due to increased I/O and undefined vendor packages the EPC increased the I/O by 24% on the ESS system. With no available room in the MCC I/O room a remote panel was added to the production deck of the platform.
“The ability to install a remote panel with minimal impact proved an adaptive solution to this issue resulting in reduced project capital,” McCormack noted.
There were also significant I/O Type changes. Where other systems require a change in card and a rewiring of the I/O, the DeltaV allows “I/O Type” to be changed in software. On the Thunderhawk Project 32 tags changed I/O Type in the ESS system. This flexibility saved significantly in project costs.
“The addition of the remote ESS cabinet on the production deck meant that the cabinet was not in a climate controlled atmosphere,” McCormack said. “The ambient Gulf of Mexico temperature can reach 40°C / 104°F. That’s hot.”
It is nowhere near the high end specification for temperature for the DeltaV SIS, however, so it would seem that this wasn’t going to be a problem.
Not so fast, McCormack noted.
“Dave Brown has written a whitepaper entitled Effects of Heat and Airflow inside an Enclosure. It discusses how mean-time-between-failure (MTBF) numbers are based on Mil standard specs of 25°C / 77°F. For every 10°C / 18°F rise above this amount, the MTBF cuts in half. Although equipment can be rated much higher, like 60°C / 140°F, its likelihood of failure rate will increase,” McCormack said. “On a safety system reduced MTBF is not an option. The Thunderhawk heat dissipation calculation for the ESS remote cabinet revealed the internal heat dissipation of the components plus the ambient temperature would give an operating environment of 52°C / 125°F.”
McCormack said that the whitepaper is clear that if the hardware is operated at elevated temperatures then you can expect higher than normal failure rates. Interpolating between the heat calc data the platform would see an MTBF of 4.7 years on the remote cabinet equipment.
For best long term reliability, then, McCormack noted, the system should be installed in 25°C / 77°F ambient temperature, allowing for excursions up to the rated operating temperature to not significantly affect the MTBF, and that the device will continue to work as expected in the elevated temperature range. Prolonged operation in the elevated temperature range will lead to premature failure of components, but this could take years of operation.
“However,” McCormack said, “note that restoring the operating range does not restore the MTBF completely. You should consider that for each year the device is operated at the elevated temperature, you are consuming multiple years of the MTBF projected life. For example, if I run the device at 35°C / 95°F for one year, it is like running it for two years at 25°C / 77°F. If I restore the temperature to 25°C / 77°F, I have aged the device by two years and can expect 48 years of life, more or less. So if you run the device for 3 years at 65°C / 149°F, and then drop the temperature to 25°C / 77°F, you should not expect an additional 46 years of service but rather maybe one or two more years.”
“After examining the remote cabinet space constraints and evaluating the temperature class of equipment installed on the deck a vortex cooler was added to the remote cabinet with an appropriate purge panel. The capability of integrating a vortex cooler with a purge panel resulted in the ability to adequately cool the equipment within the cabinet at a reduced cost compared to typical refrigerant based air conditioners,” he said.
“In planning the I/O, the key to success was assignment of I/O based on individual safety instrumented functions and logic groupings,” McCormack said.
“Properly assigning the I/O to the logic solvers is an integral part for future expansion and not being limited by the system capacities,” he said. “The architecture of Delta V SIS allows the user to concentrate on individual SIFs and each Logic Solver becomes a home for the SIFs assigned to it. This is very different from the traditional safety system which involves placing hundreds of SIF’s in a central logic solver. When the SIFs are assigned to the logic solvers and the I/O assignment is completed based on the SIF allocation the end user will not be limited by the system capacities. A complex fire and gas safety system can be achieved without nearing the system capacities as long as the front end planning is performed.”
“In addition, proper I/O assignment will decrease secure parameters being passed from SLS to SLS.”
The Thunderhawk FAT (Factory Acceptance Test) was comprised of both the SIS and PCS FAT and all interaction was fully tested between the PCS and SIS. As Delta V Simulate was not an option in version 9.3 for Delta V SIS all I/O was physically hardwired to simulators. Although much time was spent wiring the simulators to the I/O, this gave the customer the confidence to see the system being completely tested from the input, logic and output. In order to expedite the FAT checks the customer’s Cause and
Effect Diagram was dynamically linked to check the cause and effect against the simulator. Once this was performed for the group logic the customer relied on the cause and effect in conjunction with the simulator for the logic checks.
A significant project innovation in the Thunderhawk FAT was using Delta V Read/Write functions in Excel, which allowed the cause and effect to be dynamically linked simply by entering the parameter path and then conditionally formatting the cells to change color based on the parameter status. This expedited the FAT with regards to the SIS Logic checks and allowed operations to perform a 1:1 comparison of the cause and effect with the simulator.
This was a global engineering project. The Emerson Team for Thunderhawk was comprised of Emerson Hydrocarbon and Energy Industry Centre – HEIC – Calgary Alberta, Canada, Fabcon – Certified SIS Panel Manufacturer St. Louis Missouri, USA, Puffer Swieven – PCS Panel Fabricator and FAT Facility
Houston Texas, USA and the EEEC – Emerson Engineering Export Centre Pune India. The Thunderhawk Team in Pune developed the standard library modules to be used for the PCS and SIS programming based on the customer defined inputs within the Facility Control Specification (FCS).
This led to another innovation, doing acceptance testing by Webex. A Webex was performed in order to test the modules developed by the team in Pune. A meeting was held in Houston at the client’s office to review and test the functionality. With the Proplus located in Phne the client was able to Webex and take remote control of the Proplus. This allowed the customer to send start and stop commands and interlock tripconditions in order to test the various modules. This resulted in the client being able to interact directly with the programming performed in a remote location and provide feedback to the programmers. The end result of performing the Webex was expediting the signoff of the library module testing and any changes were incorporated by the team in Phune and retested the next day.
Currently, Thunderhawk’s control systems are undergoing SAT (Site Acceptance Testing) prior to moving the platform to its permanent location in the Gulf.
Latest from Home
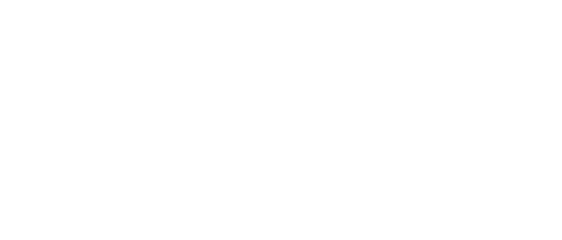
Leaders relevant to this article: