Getting an Organization Ready for S95 – Designing and Implementing Plant Models within Enterprise Applications
Overview:
The S95 Business Case The S95 Architecture Getting Ready for S95 Building the Model The CMMS Model The Microbiology Data Tracking Model The Discrepancy/CAPA Tracking Model The ERP/MRP Model Conclusions The S95 Business Case: There is a need for the Transaction-Based Enterprise Business Applications (e.g. – ERP, MRP, CMMS, EDS, LIMS) to transfer data among each other and to trigger changes of state based upon the Real-Time Control Applications (e.g. – SCADA, PLC, DCS). A cold room temperature alarm triggers. What should happen? CMMS – A Work Order opens to examine/repair the cold room MRP – All Raw Material lots in that cold room transition from Released to Quarantined Discrepancy Tracking – An Investigation is opened LIMS – Material testing is initiated How is this workflow implemented in traditional application architecture models? The S95 Architecture Case: As the need for data transfer grows – so does the number of connections For N Business Applications you will eventually build 2N Database Connections 10 applications leads to 1024 connections This complexity makes application upgrades complicated as everything is interdependent Greatly increases long term costs How is this workflow implemented in the S95 model? As the need for data transfer grows – so does the number of connections But here, N Business Applications you will only eventually build 2N Database Connections 10 applications leads to 20 connections This reduction in complexity lessens the dependencies and makes the system easier to support Greatly reduces long term costs Electronic systems can be used to streamline and optimize business processes but… There is no magic Data Associations need to be built and models need to be developed and implemented. Getting Ready for S95 Example – A batch is to be made on Bulk Process Cell 3 (PC3), MES could answer: Are all of the PC3 instruments calibrated? Are there any open work orders on PC3? Is there pending Calibration/Maintenance work on Utility systems that PC3 needs? Are there any open PC3 Deviations/CAPA’s? Are all of the PC3 users trained on the required procedures? Is there a lot restriction open on PC3? Are there any Microbiology Alert/Actions pending on the PC3 suite ? Take Home Lesson #1 If the native application that holds critical data cannot bracket it by Area/Process Cell/Unit, then you cannot extract Area/Process Cell/Unit specific data Take Home Lesson #2 If the native application cannot extract Area/Process Cell/Unit specific data - than neither can an MES In order for an MES to reach its potential, each of the applications it uses must be aware of the S88/S95 plant model and have queries in place to facilitate MES functions. Implementing a S88/S95 model into business applications can take place long before an MES is built and enhances their use – even without MES. Building the S88/S95 Model Alkermes chose the S88/S95 plant model and looked at Business applications in terms of the model. We launched a core team with the SME of each business application. For each application we asked “How would we want to use this data?” and “What is the deepest S88/S95 layer that we need to go to get that data?” For the most part – almost no users needed to extract data from their apps more granular than the unit level (and many only need it to the Process Cell level) What open deviations are there for: The Plant All Bulk Manufacturing Bulk Process Cell 3 Rinse Vessel on PC3 The exceptions to this rule were the SCADA system and the CMMS system. In both of these cases, granularity was required to the lowest level available in the model.
CMMS |
Microbiology Data Tracking |
Discrepancy/CAPA Tracking |
ERM/MRP |
|
Application Vendor Brand |
IBM Maximo |
Compliance Software Solutions Corporation MIMS |
Sparta Systems TrackWise |
Oracle OPM |
Number of Model Levels Allowed |
Unlimited |
Three – software limitation |
Three - (limited by our UI Implementation not the software |
Three - limited by our Implementation model |
Number of Parents a Child May Have |
One |
One |
One |
One |
Top Level in the S88/S95 Model |
Enterprise |
Site - Each plant has its own instance |
Enterprise |
Enterprise |
Example – a use point valve on a Bulk Process Vessel has the following parents:
It is a Child of Process Cell 3 It is a Child of the USP Water Distribution System It is a Child of the Utility PLC It is a Child of the Electrical Distribution System
Solution – Implement multiple hierarchies within CMMS so that a child can have as many parents as required:
Site Primary Hierarchy – usual S88/S95 Site Building Utility Hierarchy Site Process Utility Hierarchy Site Controls Hierarchy Site Power Hierarchy
Site Primary Hierarchy |
|||||||
Area |
Bulk Manufacturing |
Filling |
QC Labs |
Other Labs |
Product Storage Areas |
Rooms With People |
Mechanical and Prep Spaces |
Process Cell |
Each Bulk Line |
Each Fill Line |
Chemistry, Microbiology, Stability |
Each Group |
Each Major Storage Location |
Each Zone/Floor |
Each Zone/Floor |
Site Building Utility Hierarchy |
||||
Area |
HVAC |
Steam |
Chilled Water |
Hot Water |
Process Cell |
Each AHU |
Each Boiler, Each Pressure of Steam |
Each Chiller, Each Cooling Tower, Each Loop |
Each Heat Transfer Skid, Each Loop |
Site Process Utility Hierarchy |
|||||||
Area |
USP Water |
Process Solvent |
Process Waste |
Aqueous Waste |
Pure Steam |
Compressed Air |
Nitrogen |
Process Cell |
Generation, Storage, Distribution |
Loading, Storage, Distribution |
Collection, Storage, Unloading |
Collection, Storage, Treatment, Discharge |
Generation, Distribution |
Generation, Drying, Instrument, Product |
Storage, High Pressure, Low Pressure |
Microbiology data Tracking Hierarchy |
|||||
Area |
Each Bulk Line |
Each Fill Line |
Routine EM |
Global Impact |
Utilities |
Rooms |
Each Room on that Line |
Each Room on that Line |
Each Room In this Category |
Each Room In this Category |
Each Monitored Utility |
Sites |
Each Room Sample Site |
Each Room Sample Site |
Each Room Sample Site |
Each Room Sample Site |
Each Utility Use Point |
Discrepancy/CAPA Tracking Hierarchy |
||||||
Area |
Bulk Manufacturing |
Filling |
QC Labs |
Product Storage Areas |
Building Utilities |
Process Utilities |
Process Cell |
Each Bulk Line |
Each Fill Line |
Chemistry, Microbiology, Stability |
RT Quarantined RT Released Cold Quarantined Cold Released |
HVAC, Steam, Chilled Water, Hot Water |
USP Water, Process Solvent, Waste, Air, Nitrogen |
Unit |
Each Vessel |
Each Major Component is a Unit |
Chromatography Systems Computerized Lab Instruments Pipettes Meters Balances SCADA Monitored Equipment |
Each Warehouse is a Unit |
Each Major Component is a Unit |
Each Major Component is a Unit |
ERP/MRP Hierarchy |
|||
Area |
Bulk Manufacturing |
Filling |
Product Storage Areas |
Process Cell |
Each Bulk Line |
Each Fill Line |
Each Warehouse |
•
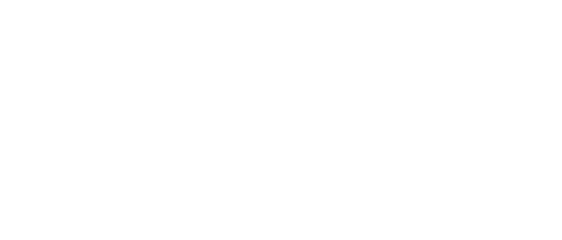
Leaders relevant to this article: