The recent publication of IEC TR 63082-1:2020 “Intelligent Device Management – Part 1: Concepts and terminology” in February and subsequent adoption by ISA at the end of April is one more tool developed to help the control community make better use of the capabilities existing in their already installed systems.
This initial document in a planned series on intelligent device management (IDM) addresses the ‘why’ of asset management as it pertains to industrial intelligent devices (IIDs). Part 2, presently under development as a planned international standard, will describe ‘what’ is necessary, and then subsequent technical reports (TR) will provide details on the ‘how’ to implement the ‘what’ in Part 2.
IEC 63082-1 describes intelligent device management concepts and terminology to describe the basic concepts of how intelligent devices can be managed and an overview of how this device management works throughout the facility lifecycle without implying a particular asset management tool or set of tools. The concept of an IDM program as a way to manage the activities associated with intelligent devices during the facility lifecycle is suggested as an approach to achieve goals across multiple internal and external stakeholders.
As devices continue to evolve to transmit more data digitally, they deliver more benefits to users as well as offer the potential for simpler deployment, improved operation and reduced costs. Intelligent device data delivery standards (the various industrial network protocols) define what each data point looks like in terms of descriptors and terminology.
This proliferation of intelligent devices has also resulted in an increase in the volume and complexity of data, requiring standards for identifying errors, diagnostic codes and critical configuration parameters, leading to better process control, higher efficiency, lower energy use, reduced downtime and higher-quality products.
Unfortunately, most installed, intelligent devices are only used to perform their primary function of providing the process variable.
All of us are likely familiar with the term GIGO (garbage in, garbage out) with reference to control practices. Asset management is one way to prevent GIGO from happening with your process by allowing one to predict, in real-time, the quality of signals to and from your field devices and, ultimately, your ability to control your process.
To meet the challenges and capture the benefits of IDM, all stakeholders, such as engineering firms, operating companies and service and equipment providers, need to understand their role in proper implementation and use of the tools and support systems for intelligent devices.
Overcoming complexity
The primary challenge of IDM is its perceived complexity. Digital communications and auxiliary functions can maximize the value of the device. However, the lack of standardized work processes and available skills at a site are a challenge for dealing effectively with the potential complexity of IDM and fuel the need for the above standards.
Achieving the full benefit of IDM requires a lifecycle approach in a structured environment that's established during the design and before operation of a facility. Existing or new facilities without IDM infrastructure can require hardware and software upgrades. Traditional tools such as gap analysis can help determine the need for hardware and software modification, new work processes and retraining personnel. With IDM infrastructure in place, facilities can be made to perform better with lower risk, while new facilities can be designed, constructed and operated in a more efficient fashion.
IDM-based work processes also provide opportunities to improve data management, workers’ knowledge, maintenance of work processes and diagnostic messaging. The net result of asset management is to provide improvement in functionality, accuracy, reliability and total cost of ownership by giving personnel the time to optimize practices to improve safety and efficiency of the manufacturing/production process.
Latest from Asset Management
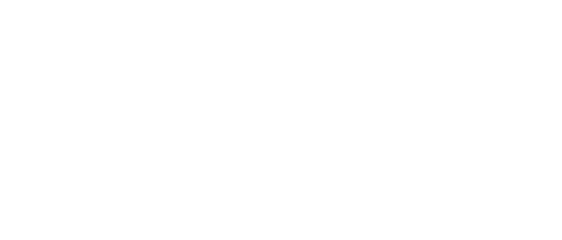
Leaders relevant to this article: