By Annie Sisson, Product Manger – FDT Group
It has been recognized time again that the ability to have open access to device intelligence is essential to enhanced reliability and reduced start-up times. In the area of industrial automation, FDT Technology provides this “open access” with a device type manager (DTM). With DTMs, users can configure device parameters, operate devices via a graphical interface and access advanced diagnostic information from any location. As discussed earlier in, “The Components of FDT Technology: A Basic Introduction to DTMs and the FDT Frame”, there are two types of DTMs available that engage this type of data access: Device DTMs and Communication DTMs. As we explore and discuss DTMs in more detail, be sure to refer back to the previous article for an introduction to these components. So what’s the scoop on DTMs?
Communication DTMs (Comm DTMs) provide the path of communication between the frame application and the end device and are required for any network structure. Comm DTMs are available for different protocols and are provided by the manufacturers of components such as gateways, multiplexers, couplers, etc. For example, a Comm DTM could be a protocol traveling the wire from Profibus to Hart, or it could be physical, such as a linking device from HSE to H1. Comm DTMs really are the “catch-all” for something that is not an end device. One of the key features of a Comm DTM is the ability for nested communication, devices arranged in a hierarchy and interconnecting through different fieldbuses. This allows seamless device data exchange, operation and maintenance via a computer to a higher level of fieldbus, reducing the amount of software and hardware the end user needs to implement compared to other technologies.
A wide variety of global automation suppliers provide DTMs with both their field devices and communication interfaces. We encourage you to take a look at the online product catalog to view the certified device DTMs at www.fdtgroup.org. With over 1300 certified device and communication DTMs available today, automation, maintenance and operations engineers and managers can search and find certified DTMs for their current installed base to maximize the full benefit of their smart devices.
In today’s market, maximizing plant assets is critical for success. DTMs provide a centralized remote access point for horizontal and vertical data flow, allowing for a safer work environment by reducing the number of trips to the field and lowering start-up and commissioning costs. End users such as Chevron, Dow, Shell and Saudi Aramco, among others, are experiencing these benefits of FDT technology and strongly support it. DTMs are “the key driver for smart devices” said Vincent Palughi in a recent article, ”FDT at Chevron.” With over 70 automation users and suppliers as members of the FDT Group, FDT Technology has been adopted around the globe.
For more information on DTMs, please email [email protected].
Latest from Asset Management
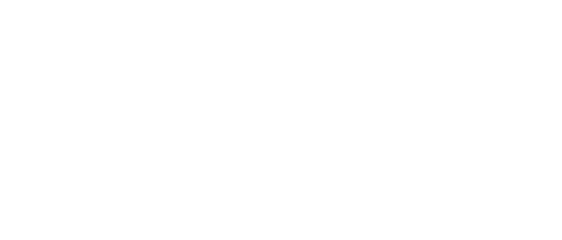
Leaders relevant to this article: