By Rich Merritt, Contributing Editor
To build an AM system, you can buy software packages that fit your application—such as fieldbus diagnostics from Vendor A and a CMMS package from Vendor B and condition monitoring software from Vendor C—and install and integrate them for a fraction of the cost of buying an integrated AM system from one vendor. But can you really do it yourself? Will you spend hundreds of hours on it? Let’s see what’s involved.
Can YOU Integrate It?
Dr. Peter Martin, vice president of strategic ventures at Invensys Process Systems (IPS), says, “Five years ago, I’d have said no. However, connectivity today is better than ever. With OPC, ISA 95, MIMOSA and the Open O&M standards, packages that comply can go together much more easily. In fact, IPS often uses AM packages from other vendors.”
Mike Lamping, technology leader at Procter & Gamble, Cincinnati, Ohio, agrees. “My experience is with Rockwell Automation’s AssetCentre and its predecessor, Rockwell Software Maintenance Automation Control Center (RSMACC),” he explains. “RSMACC required Rockwell’s assistance to set up, mostly because of IT and security components that had to be configured. Once the system was running, it worked well as long as nothing changed. RSMACC required a domain controller and expected to be part of a domain. DCOM was also an issue and required modification, which is not a typical user function.
“On the other hand, AssetCentre was easier to install. The network components are more straightforward, and it doesn’t require an IT person to help set up. The task of configuration isn’t trivial, but it’s not difficult either, so a user could do it. We didn’t do condition monitoring with either package, although my suspicion is that the more functionality you want, the less a typical user will be able to do on their own.”
Martin agrees. “The real question is not whether you can do it yourself. It’s whether you can make everything operate efficiently in support of your business. That is an entirely different question.”
For example, IPS worked with Dynegy Midstream Services, Tampa, Fla., on pushing its equipment to full capacity, which was defined in specific terms. The team then integrated SmartSignal’s machine diagnostic software with real-time performance measures—Active Factory, Suite Voyager, Avantis AM and Predictive Maintenance solutions—to monitor progress. The system gathers data from a DCS, multiple data systems, and uses hardware and software from GE, Westinghouse, Rockwell’s Allen Bradley, Caterpillar, Solar Turbines and WonderWare, then sends it over a radio telemetry link and various LANs via protocols, including WINCUU, Suitelinks, Modbus Plus and OPC. It all fits together somehow.
IPS calls its method for accomplishing this Dynamic Performance Measures (DPM). Here’s how the maintenance part works. A threshold is set for each device. If the cost element and corresponding confidence element exceed the threshold, a report is generated that alerts maintenance engineers. Reports are passed to Avantis via InFusion object technology. From Avantis, work orders are generated to the maintenance department to handle according to severity.
Steve Furbacher, Dynegy’s former president, says in such a performance-oriented approach, the organization’s top level would still set company strategy, but lower management and worker layers would be empowered to determine how to reach those goals. This includes selecting and using appropriate tools required to produce necessary decision support information.
Figure 1 shows how this strategic decomposition is playing out at South Africa-based Sasol Infrachem, a global fuel and chemical producer. Frik Van Niekerk, business manager syngas and utilities for Sasol Infrachem, says, “The DPM methodology has allowed us to optimize not only our processes but also their financial contributions at the lowest possible operating level.”
Eric Olson, instrumentation device management product manager at ABB, adds, “Users could, with the right tools, and with a limited set of goals, set up a small AM system on their own. Some users may simply want to monitor a small number of devices such as transmitters or valve positioners without any need for interfacing to higher level CMMS or ERP/MES applications.”
In fact, some AM solutions don’t even need integration. “Because MTL's Fieldbus Diagnostics use H1 communications and device descriptions (DDs), there’s no added cost to set up the diagnostics and obtain the data,” says Ian Verhappen, director of industrial networks at MTL. “FDT and EDDL technologies are two standards-based solutions for representing data in a meaningful way. They allow manufacturers to assign parameters in a logical fashion and provide varying degrees of data interpretation.”
Bumps in the Road
Though users can set up some dedicated AM packages easily and inexpensively, this road isn’t always smooth, according to Dave Jones, automation engineer and IT administrator at Ash Grove Cement, Overland Park, Kan. “I’m implementing FactoryTalk AssetCentre,” he explains. “I completed the installation phase of AssetCentre myself without any significant problems. I installed a new server on the network with an existing FactoryTalk Directory/Transaction Manager server, and things went together nicely. My only issue so far is an apparent activation problem with AssetCentre Server. I may have to call U.S.-based product support and get it resolved.”
Because he’s both an automation and IT expert, Jones is more capable than most. Still, he doesn’t foresee any major problems getting it to work, and thinks AssetCentre has a lot of potential for expansion. However, he doesn’t think he’s the one to do it. “As far as integration with an MES, CMMS or ERP system (we use Avantis), heaven help me. I’m sure we would need outside help. It’s never simple.” Jones notes that problems may occur when you move outside a limited, dedicated area.
“Customers can certainly install technology without vendor assistance, but they often need an external change agent to help them along,” adds Broussard. He says a successful AM system requires a fundamental change in plant culture, which is very difficult for one engineer to bring about. This is where an outside vendor of other “external change agent” can help convince operations, maintenance and management that integrated AM is the way to go.
AM Vendors Lend a Hand
As expected, every AM vendor says you need their help, but this is one of the times they may be right. “Our experience has been that a common failure mode for many customers is they don’t take a holistic approach to the overall AM program,” says Bart Winters, senior marketing manager for Honeywell Process Solutions. “They start with one problem area, and then move to the next. They sometimes do not consider the overall work processes and information integration needs. Consider someone that starts by focusing on mechanical integrity. They select their own package, while the rotating equipment group picks another package, and in the end these two systems don’t work together.”
Working with a DCS vendor is probably the easiest way to go. “DCS vendors offer useful packages for interrogating HART/FF/Profibus networks, and these packages are relatively easy to integrate with their control system,” says Phil Murray, principal at Feedforward Inc., a system integrator in Marietta, Ga. “Can users set up AM systems on their own? I believe that vendor or integrator help in installing the system is necessary,” he adds. “However, once the system is installed the end user is fully capable of using and maintaining the tool.”
Most AM vendors seem to think you can implement an AM system’s bottom machine-diagnostics layer, but that you should leave the rest to the experts. And, getting it working is only part of the problem. Six months later, you need to show management that its investment and faith paid off. AM vendors can help you set up a system that not only diagnoses problems, schedules maintenance and optimizes operational effectiveness, but also documents everything and prepares reports.
A systems integrator experienced in AM can help, too. “You don’t necessarily need expensive ERP consultants to implement an AM system, but you do need outside help,” says Chris Jones, VP of Business Solutions at Maverick Technologies, a system integrator in Columbia, Ill. “We take a consultative approach and ask, ‘What are the drivers and what are we trying to achieve?’ Defining those issues and challenges, and incorporating that into how we implement and design an asset management system is the real value.”
Joe Maukonen, director of MES solutions for RoviSys, adds, “The biggest problem we see is the end user often selects technology based on features, rather than first identifying and documenting user requirements, then evaluating which technology best meets the user's needs. This is where the SI can provide significant value. Having experience with asset management projects in a variety of industries and applications, the SI has seen what works and what fails and has developed an awareness of best practices.”
What Does AM Cost?
“A good rule of thumb is that the software is one third of the cost, vendor services are a third, and customer resource investment is a third of the total project cost,” says Honeywell’s Winters.
“In Yokogawa’s case, the cost to implement our Plant Resource Manager Device Maintenance Management System software is less than $35,000 for up to 3,000 field devices with condition based predictive diagnostics,” says Amit Ajmeri, technical solutions consultant at Yokogawa. “The cost includes the hardware, software licenses, installation and basic configuration. Added costs for GE Energy System1 integration for vibration analysis, interface with Maximo CMMS software, incorporation of documents, and custom diagnostics can increase the scope and price accordingly. This is where labor for asset management may start to become much more than the hardware and software.”
While AM labor cost is nowhere near that of ERP systems, some consultants still charge $200-$300 per hour. By comparison, what’s your labor worth? If you’re earning $90,000 to $100,000 per year, your cost to the company is about $100 per hour. Consequently, the question is how many hundreds of hours can you afford to devote to learning all the AM software you have to deal with?
So, the answer to the original question is, yes, you can do AM by yourself. However, the remaining question is, can you afford it?
Levels of Asset ManagementERP, CMMS & Enterprise Asset Management Systems – Responsible for the work management, parts ordering, logistics, finances, etc., associated with the work. Asset Strategy Management – Responsible for determining the best way to maintain the equipment. In this space we see Risk Based Inspection (RBI) software packages for fixed equipment (piping & vessels), Reliability Centered Maintenance (RCM) and FMEA applications for rotating and electrical equipment. These work processes identify the failure modes and strategies to detect and mitigate failures, feed scheduled maintenance activities to the CMMS system for execution, and drive the actions of the condition monitoring applications (i.e., what to monitor). Condition Assessment and Performance Management – this is typically the domain of process automation vendors. Software brings in process and condition monitoring application data to ascertain the current condition and status of the various assets and inform appropriate plant personnel as needed. These packages can interface to the CMMS to create work orders automatically. Condition Monitoring – Various condition monitoring technologies have been developed over the years to monitor for conditions indicating a degradation in performance or pending failure. For rotating equipment,technologies include vibration monitoring (wired, portable, & wireless), thermography (infrared), oil analysis and operator rounds. For fixed equipment, technologies include corrosion monitoring, ultrasonic and inspections. Instrument assets have traditionally been monitored via periodic field calibration checks and with loop performance monitoring software. Today, with the advent of smart devices, intelligence built into the devices can report on potential problems. Source: Honeywell |
Latest from Asset Management
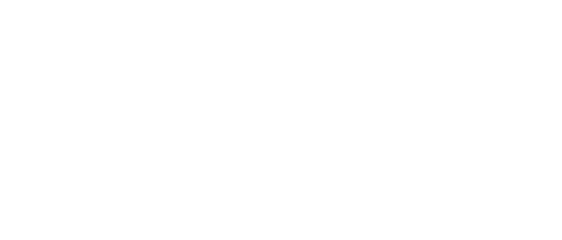
Leaders relevant to this article: