More about cost estimating process analyzer projects
By Gary D. Nichols, PE, Principal Control Systems Engineer, Jacobs Engineering Group
Weāll now address estimate accuracy and cost by project stage, sources of estimating information, types of costs by work breakdown structure (WBS), and types of construction contracts.Ā We recall from the first article in this series that we can break the analyzer project life cycle into five chronological stages (see Table 1 below). We shall confine our discussion in this article to Stages 1 through 3.
TABLE 1: ANALYZER PROJECT LIFE CYCLE STAGES Stage 1 Stage 2 Stage 3 Stage 4 Stage 5 |
For the present discussion, letās assume that Stage 1, 2 and 3 estimate accuracies are typically ±40%, ±20% and ± 5%, respectively. These are sometimes referred to as screening, budget and definitive estimates. (See Clark and Lorenzoni, Applied Cost Engineering, 3rd ed., Marcel Dekker, New York, 1997.) Readers may encounter other stage-dependent accuracies, such as ±60%, ±25%, and ±10%, respectively. Sometimes thereās a higher positive-side than negative-side spread. The point is that the estimate accuracy should become tighter as the project progresses. (See Peters and Timmerhaus, Plant Design and Economics for Chemical Engineers, 2nd ed., McGraw-Hill, New York, 1968, or Kerridge and Vervalin, eds., Engineering and Construction Project Management, Gulf Publishing Co., Houston, 1986.)
Letās now look more closely at why the stage-dependent estimate accuracies become progressively tighter. Stage 1 screening estimates can be very rough, perhaps even as rough as ±100%, because theyāre often used to make āgo/no-goā decisions or to compare alternatives. For example, a concept proposal to add an analyzer system to the trays just below a column feed point for advanced process control may seem like a good idea to operations for controllability and product qualityāuntil the screening cost is five-to-10 times more than expected.
Budgetary estimates in Stage 2 are used to obtain management approval either to proceed with the project in its entirety or, in the case of very large projects, to determine technical feasibility. For analyzer systems projects, the budgetary estimate should include analyzer systems and integrator proposals based on analyzer data sheets, specification narratives and process data sheets specific to the application at hand. Even at Stage 2, estimate accuracy is at risk when the analyzer system estimate is based on factoring, previous āsimilarā projects and extrapolation of experience.
The definitive estimate in Stage 3 includes the total installed cost, preliminary and detailed engineering and design costs up to the time of the estimate,Ā direct materials and labor for all specially engineered and commodity items, and construction indirects. Field construction itemsārepairs, relocation, remediation, demolition, dismantling, decontamination, disposal and start-upāalso must be included if these line items wouldnāt be needed were the capital project scrubbed.
Capital or Expense?
Securities, tax and internal accounting rules dictate whether certain costs are ācapitalizedā or āexpensed.ā Capitalized costs are spread over the life of the analyzer system and depreciatedāsubtracted from revenueāeach year according to certain accounting formulas. Expensed costs are subtracted from revenue in their entirety the year in which they are incurred.
Whether a cost is treated as capital or expense can have a significant impact on the client/ownerās financial performance for stockholders. The decision is generally the domain of the project controls and accounting departments, but the analyzer specialist responsible for estimating should be familiar with how the costs might be classified to be prepared to ask and answer financial and cost-accounting questions during estimate preparation.
In general, tagged/spec items, direct bulk materials, direct labor and construction indirects are capitalized. Repairs, relocation, remediation, demolition, dismantling, decontamination and disposal associated with the construction are usually expensed in the year when theyāre incurred.
Ongoing labor, material and indirect costs for repairs, maintenance and reliability are expensed in the years in which theyāre incurred over the life of the asset.
Research and development cost, preliminary engineering, detailed engineering, start-up and commissioning may be expensed or capitalized depending on such factors as size of the project, whether the work is conducted in-house by the client/owner or contracted to an engineering or consulting firm, and income tax and other tax incentives. Supplier start-up assistance, initial spare-parts inventory and initial maintenance personnel training may be estimated and paid for by the project and similarly subject to accounting rules.
Projects that incorporate analyzer systems may be spread over several years of preliminary and detailed engineering, procurement and construction. Therefore, the analyzer specialist may be asked to estimate how the respective costs will be incurred by year based on cash flow (when invoices are actually paid) and the effects of inflation and supplier cost escalation.
Sources of Cost Information
Cost information for estimating comes from a variety sources. Each has proper uses, advantages and disadvantages.
- FactoringāFactoring is the use of historical costs for similar manufacturing processes or process equipment. The historical cost may be scaled for production capacity, inflation, local costs, improved technology and regulatory requirements. A factor is applied to estimate major outlays, such as foundation work, structural steel, major vessels and equipment, power distribution, instrumentation and so on. Factoring is useful for screening, but the estimator must recognize that analyzer systems are a part of instrumentation thatās more affected by technology, regulatory requirements and the client/ownerās preferences and experience than by production capacity.
- Detailed Engineering and Design āGo-BysāāThese estimates are based on historical costs for the particular analyzer system in āsimilarā applications. For example, a gas chromatograph for measuring the hydrocarbon components in a column overhead is a common application across the refining and petrochemical industry. But the reliability of a āgo-byā estimate can be markedly decreased by the physical location of the analyzer and analyzer house, available utility, power and signal infrastructure, as well as area electrical classification, locations of sample and sample return points, and number of stream components to be measured and reported. āGoing byā the cost of āsimilarā systems is a better method for estimating analyzer system costs and is better than factoring, but best restricted to the earlier project stages because many technical and scope uncertainties are usually still unresolved at this time.Ā
- Formal ProposalsāThis is the best estimating method for analyzer systems because itās based on analyzer and process data sheets and specification narratives prepared and written for the particular application under consideration. The requests for quotations (RFQ) on which the formal proposals from suppliers are based have usually been discussed and approved across the affected disciplinesāthe client/owner, engineers and designers, project management and suppliers. Even if there are changes, the affected parties have established interpersonal working relationships by this time, and a technical basis for discussion and decision-making is in place. A difficulty with formal proposals is that the information which goes into the RFQ often isnāt available until at least the middle of the preliminary engineering stage. This leaves limited time for proposal development and resolution of technical and commercial details before the system must be ordered at the start of detailed engineering, owing to its long-lead status.
- Combination of MethodsāWhile formal proposals from analyzer system suppliers are indispensable for the specialty analyzer hardware, the estimates for preliminary and detailed engineering and field construction usually must be based on historical costs for modifying and creating data sheets, drawings and specification narratives, attending meetings and field walk-throughs, coordinating work across disciplines and administrative costs preparing estimates and schedules. Therefore, the analyzer specialist must be sure that other project team members know that analyzer systems are long-lead items, require more utilities and infrastructure than conventional instruments and may have special construction requirements such as rigging and lifting.
Types of Construction Contracts
Construction contracts are either ācost-plusā or ālump sumā (see Hart, Quality Handbook for Architectural, Engineering, and Construction Community, American Society for Quality Control, Milwaukee, Wis., 1994). These two contract types can conveniently be considered as opposites with regard to total installed cost, schedule, flexibility, required scope accuracy and required estimate accuracy. Assistance from project controls, procurement and the legal department are indispensable to the analyzer or other engineering specialist when developing the construction estimate and contract.
The ācost-plusā or reimbursable contract is generally quite flexible in that the contractor charges a fixed markup for each unit of direct material, direct labor and construction indirect, irrespective of the construction scope. Therefore, field changes generally are billed as if they were in the original scope. The reimbursable contract works best when the integrity of the contractor is high, there is a good working relationship with the client/owner, there is reason to believe that field changes will be significant and the schedule is subject to changes.
āLump-sumā or unit pricing/fixed contracts are economical when the construction scope is very well-defined and detailed, scope and field changes arenāt expected, and the costs and schedule are accurately known. The construction contractor follows the written construction scope in great detail, and bills for work completed per the details. Scope changes and change orders are generally very costly in money and time with the lump-sum contract.
Ā About the Author |
Gary Nichols, PE, is principal control systems engineer with Jacobs Engineering Group. He can be reached at [email protected].
Latest from Asset Management
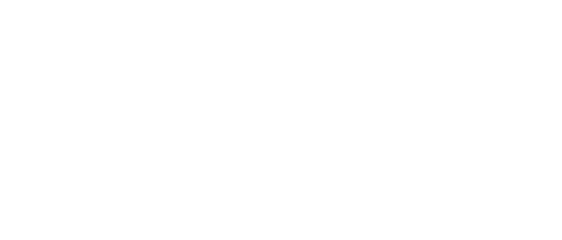
Leaders relevant to this article: