AT ONE TIME, the major purpose of a process simulator was to train operators. Simulation technology has come a long way since then. Today, simulators are beneficial during a plants entire lifecycle from initial design through construction, control system development and startup, and onward, all the way to replacing the control system many years down the road.
Barry Hu, a process engineer at Genencor International in Cedar Rapids, Iowa, is using Mimic simulation software from Mynah Technologies to ease his facilitys update. "Mimic has been a tremendous troubleshooting and training tool for us as we migrate our automation platform from RS3 to DeltaV," he says. The plant produces industrial enzymes using fermentation. "By using Mimic to simulate our fermentation batch processes, I was able to detect problems in batch programming and control algorithms that would have caused production loss. The operators were comfortable with the new system because they trained on Mimic for three months before it came online. We were prepared to dump three batches during the start-up, anticipating glitches in the new system and the new programs. We dumped none. Mimic simulation cut our start-up time by at least three days, and saved us tens of thousand dollars in raw material and utility costs."
Simulation pays for itself, it seems. Process simulation can be applied through each significant stage in a projects lifecycle, says Mike Lane, an engineer with Autopro Automation Consultants, a systems integrator in Grande Prairie, Alberta, Canada. Through a series of successive steps, from concept and design through training and operation of the process, simulation can generate return on investment. The cumulative effect of ongoing cost savings and improved operating rate can be substantial, and typically returns the initial simulation investment within the first year of operation. It will continue to contribute to our profitability on an annual basis.Simulation Progress
Simulators used to be just for training operators, says Gregory McKim, director of operator training simulators and services for SimSci-Esscor. Today, a simulator is often part of a larger project, usually a DCS upgrade, where not just operators need training, but I&C personnel as well. In addition, part of the drive for simulators is their control checkout capability. This is often used as an economic justification for buying the simulator.
The use of operator training simulators (OTSs) has increased in recent times, he adds. Five to 10 years ago, every simulator project was for a plant that already had a well-established control system and operating procedure. Now, most DCS upgrade projects have a requirement for a simulator as part of the overall program.
Sometimes simulation is required, says Glen, a control engineer with a major paper company. Were building a greenfield plant in Brazil, where the people who will be running it have zero experience, he says. There are half a dozen other mills in the region, and every one used simulators to train operators. So, when we contracted to buy a DCS for our new mill, we made simulation part of the deal.
Patrick Rossi, process automation project manager at Mead Johnson in Zeeland, Mich., adds, Our plant is very integrated, and somewhere around 50 production and clean-in-place process unit operations must function both synchronously and asynchronously. Work instructions are embedded in the control system to create a seamless operation. Quality assurance, field connections, and automated sensors are brought into the control system. Lean staffing forces us to use technology to help train people. Operators have standard operating procedures they must sign-off on before being allowed to work. Simulation gives us the means to prove that operators are trained in automation before theyre turned loose.
Chuck Marsh, senior project engineer at Siemens Energy and Automation, says several trends are driving increased use of simulators. Because of the Brain Drain, many of a plants most knowledgeable resources from operations, maintenance, and engineering are transitioning out of the workforce, he says. Operators are being asked to do more with less formalized training time, and there is pressure on engineering personnel to reduce costs, avoid unplanned downtime, minimize disruptions to the process, and reduce installation and commissioning times.
Were witnessing significant growth in customers using simulations, says Jim Siemers, educational services manager at Emerson Process Management. As customers examine their businesses for profit opportunities, theyre increasingly looking toward operational efficiency. Simulation technology provides measurable results.
Training is still the crux of the matter, he adds. Operators have received more interest in the last few years. Knowledgeable plant and production managers realize the importance of simulation in the design and implementation phases of their projects, and so theyre training their operators on scenarios and procedures to reduce incidents related to operational errors. Our customers want a process-specific simulation operated with their graphics and courseware to help educate their entire staff, not just operators. A recent customer used its DeltaV OTS purchase to train its entire operations department to facilitate effective communications throughout the department when discussing the process.
Marsh says not everyone is convinced. Orders typically come from companies that have already incorporated simulation into their production lifecycle, he says. For companies that havent yet discovered the benefits of simulation, the seemingly higher upfront cost is often a major obstacle. In some cases, simulation capabilities are added to a project as an afterthought. Unfortunately this typically doesnt result in the best ROI.
Some engineers have discovered that working with an OTS is a career-enhancing move, says Randy Wagler, process performance solutions product manager at Honeywell Process Solutions. The simulator custodian, sometimes a junior engineer, often becomes extremely valuable to the organization, particularly when he or she has participated throughout the OTS development period with the simulation vendor, says Wagler. This individual becomes familiar with all the major plant systems. For example, the training support person will become familiar with the plants design, dynamic behavior of process equipment, control system implementation, and operating procedures. Normally, these disciplines are handled by specialists like process engineers, control engineers, and operations leaders. These skills are rarely found in one individual. Consequently, after the turnover of the OTS, its specialist normally gets reassigned to other higher-level positions where this knowledge can be leveraged during startup.
Simulating Design
Peter Henderson, process performance solutions product manager at Honeywell Process Solutions, says plant design has changed over the years, and simulation is necessary from the beginning. Plant design is rapidly evolving from steady-state design to a complete assessment of the plants behavior and bottlenecks throughout the entire range of operation with dynamic simulation, he says. This proves equipment capacities will provide sufficient performance at alternate operating conditions outside the normal design case. Engineering contractors have recently been doing engineering studies for equipment rating, instrument specification, time constant, valve- stroke times, safety assessment, and control strategy development. Control system vendors are applying control system emulation prior to acceptance testing to eliminate many of the errors that might not be uncovered prior to initial operations during commissioning. The benefit of this is lower commissioning costs and faster plant startups and earlier profits.
Siemers says using simulation to prove the design of a process is almost always used in new refineries and other oil and gas projects.
Simulation is far more prevalent and accepted in the refining and oil and gas industries than it is in power generation, agrees McKim. Many petrochemical companies maintain staffs of performance engineers that use steady-state design tools in conjunction with or in addition to dynamic simulation to perform sizing/optimizing studies. Dynamic simulation in the power industry is most often used for design studies, of duct implosion, for example, by engineering and procurement contractors (EPCs).
Jose Maria Ferrer, business consultant for Aspentech, says simulation is often used when proving complex designs. Wherever you have a compressor network, or a novel design, or a more complex control strategy, dynamic simulators are used about 80% of the time, he says. Knowledgeable plant and production managers realize the importance of simulation in the design and implementation phase of their projects, and are leveraging that realism to train their operators on scenarios and procedures to reduce incidents related to operational errors.
In some cases, dynamic simulation works especially well when vast amounts of historical data are available from similar processes, such as liquid natural gas (LNG) plant design. Honeywell developed an LNG simulator based on operating data from 10 LNG plants to ensure the model was accurate. This helps plant design engineers optimize equipment design, familiarize operators with the plants dynamic response, and help prepare them for plant operations.
Having a specific simulator available for a process makes it easier on the engineer responsible. An important component is the experience and ability of the process engineer preparing the simulation of the process and control models, says Henderson. Its rare to find an individual with the detailed knowledge of the process design, control strategies, and operating philosophies for complex LNG plants.
When a company wants to build a similar plant, using a simulator on an existing plant can help. For example, Absolut Vodka in Sweden wanted to build another plant, but wanted to make sure its new distillery would produce vodka with exactly the same smell and flavor as the existing plant. The firm used a simulator to investigate how every process variable affects product quality.
Absolut used an HYSYS simulator from Aspentech to build a model of the existing plant, run tests and simulations in the model, and compare the models results with data from the real plant. The companys engineers found that changes predicted by the model occurred in the real plant. Armed with this added assurance, Absolut built its new plant.
Simulators can be used during the design phase to check out HMI displays (See Figure 2), process logic, and software upgrades. Doug Taylor of Concept Systems, a systems integrator in Albany, Oregon, uses simulation techniques to work out what operator interfaces should look like before an automation project starts. Customers often have a hard time visualizing the optimal operator interface for a new control system, so Concept's engineers mock up functional human interfaces using simulation technology, says Taylor. Though this simulated interface could be used for operator training, Concept's customers seem to always prefer doing operator training on the actual machinery.Mike Lane, another systems integrator, worked with a simulator at a Weyerhaeuser paper mill in Canada, and he agrees with Taylor. The most significant benefit was the ability to stage and verify graphics, he reports. In previous years, there was no way to compile or test graphics. This forced us to conduct all graphics testing and debugging during commissioning, and sometimes during plant startup. The ability to conduct this work offline was judged by the project team to be adequate justification for using Shadow Plant.
Rossi adds, We use simulation for initial training on major changes in software programming, and to wring out the software logic before we deploy it into the process. Our results have been quite positive. If we can train the operations on 90% of the what-if scenarios they may run into, we're golden.
Managing Change
Glen, the paper company engineer, cautions that you have to keep a close eye on the contractors when using a simulator to avoid getting bogus information. Consulting engineers rarely have all the right information at the beginning of a project, such as valve sizing, pipe sizes, flow rates and other critical information that affects the simulation, he says. Whats more, as various contractors are involved in the construction of a plant, not everybody talks to each other. Typically, we give them specs, which include a simulator. The simulator finds design problems, so we expect the real controllers to match the simulation parameters. To make a simulator work well, you have to manage the suppliers closely, so any design or equipment changes are incorporated into the simulator, and any changes called for by the simulator get relayed to the contractors.
Ferrer adds the OTS provider must protect itself. The design suffers changes as the project develops, he says. To prevent this, the OTS supplier establishes dates to freeze the project data. After that, every change has an extra charge, as it requires rework. Sometimes changes such as valve sizing or location are suggested by the operators during training sessions or control studies. This is good because its better to discover mistakes before startup.
As with any project, accurate information is essential to the overall success, adds Siemers. Change management is essential to prevent unnecessary delays and cost overruns. Effective, timely, and accurate communication is the best defense against this type of scenario. Users can prevent this by taking proactive steps to establish clear lines of communication for all project participants, and conduct regular change audits.
McKim adds, An emerging trend is to combine steady-state and dynamic simulation with front-end engineering design (FEED), in which design and analysis tools share connections to a common design database.
Henderson agrees. I wouldn't call it bogus information, but there are several phases through the engineering process where design and equipment information is refined, he says. FEED data is all theoretical performance around the design basis. You wouldn't build an OTS on this data, but you might create more focused simulations to dynamically visualize and validate design assumptions. During the detailed-design phase, EPC vendors will update the FEED design, and update equipment performance with information from selected vendors.
These issues are normally handled in the OTS design phase to align with customer expectations. In older plants, the data may not exist or wasnt updated or maintained during years of plant transformations. The original heat/material balance may no longer apply. In this case, the OTS project may need a new simulator design basis.
Standalone vs. Connected
Simulators fall into two broad categoriesstandalone and connected. A standalone simulator operates completely independent of the process control system. A connected system provides simulated inputs (sometimes called stimulated) to an actual control system.
Ideally the process control system and training system exist on separate networks, says Siemers. This is a key advantage of a training simulator because it removes the potential risk of upsetting the process on which the operator is training.
March adds, We see our customers using simulators in standalone mode most frequently. With the modular approach to simulation, process dynamics and system response can be accurately represented even in an offline manner. This ensures theres no possible disturbance to the live, running process.
In our case, a simulator is a real control system thats the same as the one running the machine tools on the manufacturing floor, says Gary Highley, product manager at GE Fanuc Automation, which makes simulators for discrete automation applications, such as machine tools. Ladder logic to control a machine function and parameters for testing servo systems can all be adjusted. Its a standalone system thats been slightly modified, so it doesnt have to be attached to the machine tool, and all of its various switches, motors, and valves operate. These simulators can run the same programs and ladder logic as on the shop floor. A range of scenarios can be trained for, tested, or developed. It can safely test scenarios you wouldnt dare try in a real manufacturing process.
Siemers adds, Control modifications required for plant operation can be verified for proper operation on the simulator, and then implemented in the plant. Customers who have taken advantage of this type of testing and pre-startup training have had excellent first-time start-ups. Eliminating extra start-up days through manufacturing control system checkout using a fully rigorous dynamic model is a common justification for buying the simulator.
Opto 22 also has a hard simulator. The SNAP Ultimate I/O Learning Center is a fully functional, complete package of hardware and software that provides everything needed to learn and train with Opto 22 Ethernet-based technology, says James Davis, application engineer. You get to configure I/O points, read and write to those points, create flowcharts as part of a control strategy, and build a graphical user interface. And you can test the hardware and the strategies you create using built-in LEDs, potentiometers, temperature probes, voltage meters, and other instrumentation.
Ed Kirk, assistant professor of the regional occupational program at Palomar College in San Marcos, Calif., uses an Opto 22 system to help teach air conditioning, refrigeration, heating, and controls at the entry level. I use simulation to set up and demonstrate how equipment works, he says. This process includes graphic displays of any process I can develop. This system allows for changes in operation with real-time displays of whats happening to the equipment. Ive adapted things like single-phase fan controllers with a temperature input to be directly controlled by an analog output module instead of the temperature sensor. Ive have gotten to a point where its difficult to tell the difference between simulation and real-world applications.
Really Real Simulations
The difference between standalone and connected systems also can get a little hazy because its sometimes possible to connect the standalone to the process control system. Many simulators run on standard PCs under Windows, so you can connect them any way you like to nearly any kind of hardware, including a control system.
Nearly all DCS manufacturers offer virtual stimulation controller software (See Figure 3 below) that simulates one or multiple controllers running on a single PC, explains McKim. This virtual system then connects to a simulator process model via a cross-reference table that ties model points to control system I/O points. The advantage of the virtual control system is that it runs the exact same control code that a real controller does, reduces the amount of hardware, and most importantly integrates seamlessly with DCS HMI stations. This is the most effective simulation of the DCS because the system behaves just as real controllers would, and the operator interface is identical to that in the control room.
The Plant Simulator uses a Virtual Stimulated representation of a control system. A standard PC is running controls simulation, HMI, and the Simulator Process Model. Source:Invensys
ngineers can review these runs in an accelerated mode the next day, and review the performance of the control logic. Weve had virtual cells run connected to control systems for two to three weeks without stopping. We think truly testing a control system prior to installation is one of the best benefits of this technology.
Siemens can do this too, but Marsh says they dont see it very often. With the SIMBApro and SIMIT simulation packages from Siemens, a hardware simulator in a PCI card can be used in conjunction with an engineering station or a dedicated simulation station to test the actual response of the control system. One large food and beverage manufacturer uses this package with its PCS 7 system to test new recipes. The cards are connected via Profibus to an actual hardware controller. The card then simulates the actual electrical signals and dynamic response that would be generated by their remote I/O and smart instrumentation.
Some external simulators can force variable changes in the plant historian, thereby simulating inputs to the process control system. Some DCS vendors supply simulators that can run in either mode. In some cases, you can buy a PC-based software version of a large-scale DCS, so you can simulate your entire control system in a PC. In short, if you have a standard DCS, you can probably purchase several different simulators, ranging from a simple OTS to a full-bore dynamic process simulator.
Bringing up the Simulator
Though simulation software is widely available and 10 times more capable than it was a few years ago, that doesnt mean its easy to set up. Tom Badura, electronics project engineer at a Midwestern plastics manufacturer, says hed like to use simulation, but doesnt have the resources. Although the chemical processes in our plant would be complex to simulate accurately, much process and control system training simulation could be developed without truly simulating the process, he says. This can be done using the functionality of the control system and HMI packages. Unfortunately, we dont have the manpower and time to develop even this limited simulation. Weve used vendor-developed simulation for operator training when installing a new control system. This training had limited success partly because we werent able to dedicate technical or management resources to the training program.
Thats certainly a problem, but you have to give vendors credit for trying to simplify. For example, FEED techniques allow users to establish one database for the control system and simulator. Its even possible to import P&IDs into a simulator. Protocols exist for exchanging this data between software applications like simulations and drawing packages through a common database, explains Henderson. Control system vendors are providing soft-control environments that can be integrated with simulators. This allows actual plant control and logic configurations to be downloaded from the plant directly into control components integrated with the simulator. These data exchange methods eliminate effort in data manipulations and entry during the initial model development and subsequent model updates as the plant design changes. Many steady-state simulators also have the ability to generate the process flow diagrams (PFDs).
Siemers adds, Mimic simulates the process input and output parameters of the DeltaV control modules using DeltaV Simulate. We use the actual configuration by importing the DeltaV.fhx files. The simulator simulates the process equipment mathematically, reads the outputs from DeltaV, applies the dynamics and writes the inputs to the system.
McKim says, Most of SimSci-Esscor's simulators use virtual stimulation controls with DCS database files, graphics, and other data exactly from the real control system, without translation or emulation. In addition, they offer connections for nearly all major DCSes, including Foxboro, Triconex, Emerson Ovation and Delta V, ABB Industrial IT, GE MkVI, Honeywell, Metso, GE Fanuc, and many other DCS and PLC control systems.
As with all systems, theres an administrative effort required to configure the system and support the simulation environment, says systems integrator Lane. The effort and skills required are different from those needed to configure and support a DCS. Training from the vendor will usually be required. Our experience at Weyerhaeuser was that about one effort-month was required to configure the test system. However, during times of peak software testing, administering the system and assisting users conducting tag loads and testing was nearly a full-time job.
In process control, nothing is easy or inexpensive. Operator training simulators certainly appear to be worth all the trouble, especially when they can save time and money during commissioning and startup.
Latest from Asset Management
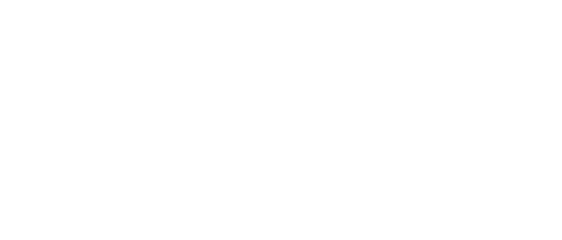
Leaders relevant to this article: