S |
ometime in the next year or so, companiesĀ are going to release control products that will change the landscape of automation and process control. These changes may be the most dramatic to hit our industry since 1975, when the introduction of distributed control systems (DCSs) completely upset the analog control apple cart, threw the established control industry into turmoil, and caused dozens of old, slow-moving control vendors to fail. By the time the DCS trend had swept the industry it had helped create a whole new set of control equipment suppliers.
The biggest difference now is that in 1975 Honeywell caught the rest of the industry with its pants down when it introduced the TDC 2000. This time, severalĀif not allĀof the control vendors have their R&D āskunk worksā busy creating new distributed intelligence products, so itās likely most will come to the market at about the same time.
Essentially, a new type of control system is coming down the pike, and it promises to save you millions of dollars in hardware costs, provide access to the most advanced control and monitoring software at a fraction of todayās price, eliminate security problems, and allow unattended process plant operations. Whatās more, it will be better suited to solving your problems than todayās overly complex systems.
āThe great thing about the control business today is the equipment and software is finally evolving to the point where we can make the solution fit the problem,ā says Edward Bullerdiek, control group leader at Marathon Ashland Petroleum in Detroit. āIn the past we've always had to make the problem fit a usually imperfect solution. The user community knows how this ended upāusually not well.ā
Two technologies are involved: one at the bottom of the control pyramid and one at the top. One begets the other.
The Dream Begins Here
With sensor networks, all you need is a $50 mote and an A/D converter. Hardware cost: $100 or less. If the vendor embeds a mote into the transmitter at the factory, the added cost is incremental; about $5. Micrel (www.micrel.com), for example, is offering its RadioWire RF Transceiver to OEMs for $4.50 each. Then, any processor with a DCS or ERP program that wants to see the pressure value simply calls up the IP address of the web server in the sensor and reads it with a conventional web browser.Ā āThe concept behind motes is not unique,ā says Robert Jackson, PXI Product Manager at National Instruments (www.ni.com). āAn example would be a computer with a wireless connection or radio modem.ā He likens them to the transducer electronic data sheet (TEDS) āsmart sensorsā defined by IEEE 1451.2-1997. āThe key is that applications for smart sensors and motes increase as the cost and size of processors decreases. With the trend for faster and cheaper processors unlikely to reverse, it is important for process control applications to support PC-based technology. Motes will not replace all sensors, but smart sensors will play a role in specialty applications.āĀ FIGURE 2: THE WAY WE ARE
Such a concept shakes the very foundation of the process control and automation industry, which is based on charging huge amounts of money for the specialized hardware, software and services traditionally required to acquire data from sensors and transmit commands to actuators (See Figure 2). Motes, sensor networks and pervasive computing threaten to replace all that infrastructureĀfieldbuses, proprietary networks, redundant networks, intrinsic safety hardware, cable, conduit, I/O boards, data acquisition hardware, enclosures and so onĀwith inexpensive wireless devices.Ā
May the Force be With You
Control equipment vendors can rest easy for the time being, because motes are a few years away. āIn three to five years, pervasive computing applications will start to dominate the technological market, much like the telecom industry dominated in the late Ć¢ĀĀ90s,ā predicts Dr. Stewart.Ā
At present, the only functioning mote systems we know about are in laboratories, research facilities, semiconductor fabrication plants, and a ship. BP, for example, has outfitted one of its oil tankers with 160 motes to measure vibration in the shipās pumps, compressors and engines. At Intelās Ronler Acres semiconductor fabrication plant in Hillsboro, Ore., vibration engineer Mick Flanigan is working with motes and vibration sensors. Itās all still in development, Flanigan says, but the results are promising.Ā
āWe are monitoring pumps, compressors, and other plant facilities equipment with vibration sensors,ā he reports. āEach machine has from 1-12 vibration sensors, and each sensor has a mote. The motes report via wireless to a central Stargate wireless processor, which converts the data from up to 12 motes and transmits it to a PC that runs Rockwell Automationās ENSHARE asset management software.ā
Flanigan reports that they have 210 sensors installed on 40 machines so far, and will eventually equip about 3,000 machines. The cost to equip a machine with six sensors is about $750 for the vibration sensors and about $250 for the motes, Stargate modem and enclosures, or about $1,000 per machine. To do it with conventional equipment would cost āabout $8,000 per machine,ā Flanigan estimates.Ā
The technology is not quite ready for prime time, though. You can buy the necessary hardware easily enough, but better hardware-to-software integration is needed. āWe are probably a year away from having commercially available network components and the software to tie them to asset monitoring software,ā says Flanigan. āHowever, any reasonably competent engineer can put such a system together today. In my case, the tough part was dealing with the complex vibration data, not the motes.ā
Some automation companies have distributed intelligence projects in the works. āRockwell Automation is working on technologies to propagate control capabilities as low in the architecture as required by the customer application,ā says Rockwellās John Weisenberger, a strategic marketing manager for Distributed I/O. āOver the next 2-3 years, itās likely that the next logical step beyond running many applications on a white box PC will be a migration into the controller rack. Additional functionality will migrate into the devices themselves. This, however, will require development of much simpler system management tools to increase the level of robustness, manageability and maintainability of such solutions.ā
As far as we know, no process control company or software vendor has yet to develop a product. They are mostly still at the talking stage. And waiting.Ā
āStandards organizations such as ZigBee, the 802.15.4 committee, and the Wireless Industrial Networking Alliance (WINA) are all working to make wireless standards and products more appropriate for industrial applications,ā says Hesh Kagan, Consulting Engineer, at Invensys Process Systems. āInvensys is involved with the standards groups as well as WINA, helping to promote the acceptance of wireless solutions.ā
āMotes are a great concept, especially for independent field measurement and reporting devices,ā says James M. DiNanno, marketing manager at Schneider Electric (www.schneider-electric.com). āMotes are a concept for dynamic networks, where sensors talk to each other using embedded RF and smart technology. The addition of mesh networking also helps to create a robust self reconfiguring network topology. The best industrial application for this type of technology is redundancy, to assure reliability and to double-check the information being used before taking a control action which is gated by a master controller.ā
Michael Paulonis, instrument engineer at Eastman Chemical Company, Kingsport, Tenn., thinks motes are mostly hype. āTypically, emerging technologies quickly climb the hype curve and get a lot of, well, hype,ā says Paulonis. āThen, as reality sinks in and issues are exposed, the technology descends into a trough of disillusionment. Some technologies make it out of the trough and slowly climb to a plateau of productivity. I don't see the game-changing nature you describe for wireless distributed sensing and control. Granted, it will reduce installation cost, but that seems much more evolutionary than revolutionary.āWhile we wait for motes and pervasive computing, wireless products continue to make inroads into the hardwired scene. A study by Venture Development Corp. (www.vdc.com) predicts that spending on wireless networks will more than double from the $75 million spent in 2003 to more than $183 million by 2006. While we see little evidence that the hard core process control suppliers are making wireless products, a scan through issues of our companion publication, Industrial Networking, reveals plenty of companies offering wireless Ethernet products and systems.Ā How Low Can We Go?
Motes, wireless, fieldbus, pervasive computing, smart sensors, smart valves, and a host of similar intelligent devices raise the question: How low can we go? How far out can we push distributed control? Technology makes it possible to put an inexpensive processor at every sensor and actuator, and lets them talk to each other. But we donāt need motes to do that: we can do it now with hardwired networks.Ā Systems integrator Ian Verhappen says we are on our way down: āThe trend is to distribute down to the lowest level, as evidenced by research in networked motes,ā says Verhappen, director of ICE-Pros (www.ice-pros.com). āIn the case of fieldbus, field-level control ensures single-loop integrity, minimizing the impact of a single point of failure. If properly designed, a fieldbus systemās only significant point of failure is the home run cable.āLuis Trejo, an engineer for Emerson Process Management Mexico (www.emersonprocess.com), agrees. āI personally think the Ć¢ĀĀfarther down the better.ā The more intelligence is in the basic cell the better for the whole unit, mainly because of improvement in execution times and diagnostics information.āĀ Typically, emerging technologies quickly climb the hype curve and get a lot of, well, hype." This is not suitable for every application, of course. āThis does not mean that you could eliminate the main process controller,ā Trejo notes. āMost projects I have participated in lately include more sophisticated strategies that have information from and output sent to various elements. Multivariable process control, automatic start-up and shutdown are common strategies requested by end users. These strategies have to be coordinated by a central controller.āEven if you have the capability, you donāt have to use it. Jorge Cano Carmona, a process control engineer at MetMex Penoles in Torreón Coah, Mexico, has Foundation fieldbus (FF), so he can distribute control as far out as he wants. āIt is very important to choose when and where to put the control in a smart instrument,ā he says. āIn my latest experience with FF instruments in two ammonia spheres, we discussed where to download the PID: In the controller or in the valve? We analyzed the process operation and choose the controller.āIt was a tough decision. āThe advantage of running the control loop at the valve allows for continuous operation if the controller fails,ā he admits. āHowever, if a failure occurs, most likely it will be the FF segment. It is more common to find a fault in a segment than in the controller, at least with the controllers we are using.ā To Carmona and MetMex then, there is no advantage to putting control at the valve.Verhappen agrees that controllers are more reliable than the field devices. āLook at SIL ratings to confirm that,ā he says. āHowever, if the field devices fail, what do you have to control toāor with? The main impediment to field based control in my mind is that every PID algorithm in the field can be a different type, so that if you migrate control from one device to another, the tuning will be different. Some call it gain, others call it proportional band.āDistributing control to field devices is not a technical or hardware problem. Dave Holmes, marketing communications manager for Emerson Process Management, explains: āIn the case of Emerson, the same algorithms that run in the controller also run in the final devices. This gives us the unique ability to move the execution of the control algorithm from the controller and back again without affecting how the control is executed.āāOne significant advantage to running PID in the final control elements or sensors is the ability to have localized loop control at the process,ā he adds. āShould communications with automation system experience be interrupted, the backup link active scheduler in the H1 segment will continue to maintain reliable control locally.āTwo problems raise their ugly heads when intelligence is distributed out so far:Ā 1.Ā Ā How do devices from different vendors talk to each other? 2.Ā Ā Whoās in charge here?āThe largest issue preventing the widespread adoption of digital control at the field level is interchangeability,ā says Verhappen. āThis means the ability to truly exchange one manufacturer's device for another and get the same functionality. To be truly effective the networks need to be vendor-independent and therefore able to talk to each other, regardless of who makes them and what each one is saying. We still need to find a way to get everyone to agree to a common 'object dictionary' series of definitions. I believe that ISA, NAMUR, and the various fieldbus foundations have a role to play here.āĀ Tom Mueller, director, Asset Optimization Marketing at ABB (www.abb.com) supports Verhappenās assertion. āThe challenge right now, as more intelligence goes to the field devices, is finding a way to capture this intelligence and deliver it from the device to the user in a usable format,ā says Mueller. āThe current standards are not consistent enough to use intelligence from multiple vendors effectively to get to the Ć¢ĀĀnew frontierāāreally taking this intelligence beyond control loops and PID and up to advanced control levels. Many customers have an interest in this opportunity to do much more with their field device intelligence, but they need a way to get this information back in a usable and understandable format.āEven if the information was readily available, who makes the decisions? Steve Lazok,Ā manager of Technical Solutions Support at Yokogawa (www.yokogawa.com) lays out the problem: āThe issue is, not where control executes, but where and how you manage the information and how to interact with control in the field. Where and how does an operator change a setpoint? Where, how, and to whom does device information, like its health, get reported? And then, who fixes any problems and by what means do these problems get fixed?āDiNanno says the basic fault is in the distributed control concept. āThe most notable weaknesses of distributed control are the lack of precise integrated software tools and ways to handle scenario-evaluation and decision-making processes,ā he says. āSince you may deploy many intelligent devices and these can operate autonomously, the number of scenarios and methods to manage and interoperate all these devices can become a very large and complex task. Better tools are needed to help manage these types of conditions in an easier way.āTodd Stauffer, marketing manager at Siemens Process Automaton Systems group, agrees. āTo gather up all these inputs from distributed devices that may not necessarily be on the same physical bus, and provide this data to an embedded controller in a field device in real time without data latency issues is a major challenge, and perhaps out of reach today,ā says Stauffer. āThis is reflected by the trend that while fieldbus adoption has shown an increase over the last 3-4 years, adoption of control in the field in real process plants have been relatively weak.āBut wait! Getting all that data to distributed devices is exactly what motes and sensor networks do! They bypass all the fieldbus segment limitations, data latency problems, and vendor incompatibility issues. If a controller needs a particular sensor input, it just asks the sensor for it. Sensor networks may be the key to advanced control.Ā Making Advanced Control Possible
Control gurus, like our own Bela Liptak, keep telling us that multivariable control is the future. Instead of just dealing with a simple process loop, future control systems will develop models, consider everything thatās going on in a plant, and make control decisions based on many interlocking and interdependent variables.Some industries already rely on multivariable control. āBoiler-turbine control systems must deal with a high degree of process interaction, which requires the system to coordinate many different plant functions, from boiler inputs to generator output,ā says Roger Leimbach, marketing manager at Metso Automation (www.metso.com). āThere are few independent control loops in a power plant automation system. Virtually all critical processes are interconnected, which requires constant communication, especially during load changes. Communication delays cannot be tolerated. Thus, pushing control functions down to the device level is not likely, nor recommended." "There is a magic sweet spot where field control is not most beneficial and where centralized control becomes advantageous."Ā The rest of the world is still catching up to the idea. āProcess manufacturing facilities resemble other complex systems such as organisms, buildings, aircraft, ecosystems, cities and economies,ā explains Lane Desborough, an analyst at Honeywell Process Solutions, Phoenix, Ariz. āWhen there isn't some degree of alignment between the disparate parts of these systems, when they aren't all focused on the same goal, then suboptimal things can happen. This strikes right to the heart of distributed control. Many authors recognize that Ć¢ĀĀreductionist theoryā reaches its point of diminishing returns when applied to complex systems.āHe continues: āLet's say that you have control algorithms in the valve tops and the brains and alarm notifications are distributed out into a thousand places around the plant. Where is the guarantee that these controllers are working toward a common purpose such as making money? How are they coordinated in such a way as to notify the operator, maintenance planner, technician, and engineer only if and when their process performance degrades and is no longer consistent with business objectives?āPaul McLaughlin, director of architecture for Honeywell Process Solutions, adds: āOne argument against extreme downloading of control is that process elements are multivariable dynamic systems. Decisions on control actions for multiple actuators must be undertaken in a coordinated way and based on measurements of multiple, sometimes hundreds of parameters. There are, therefore, good reasons for today's distributed control architectures with their separation of multivariable supervisory and univariable regulatory control. Complete distribution of control isn't advisable. But with technological advances steadily removing barriers to distribution, we can expect that problem and process characteristics will dictate distribution to a considerably greater extent than is possible today.āIt looks like distributing control to ordinary field elements is good only in some cases. āDecentralized control is best suited for basic controls such as plain PID, cascade PID, feedforward and ratio,ā says Jonas Berge, marketing manager for SMAR (www.smar.com). āAlthough it is theoretically possible to do very complex loops in field instruments, the control cycle will get too long if too many blocks are chained in series. There is a magic sweet spot where field control is not most beneficial and where centralized control becomes advantageous.āBullerdiek backs that up: āAny complex process that requires a high degree of coordination, such as batch processes and continuous processing units, will still benefit from centralized control,ā he says. āThe regulatory loops might get pushed out to a fieldbus, but there will still be a reason for centralizing the higher level controls. The rule of thumb will likely be: wide distribution/low complexity equals highly distributed control, and close proximity/high complexity equals centralized control.āIt is safe to say that batch control systems, continuous control, and advanced control of all kinds most likely will require some kind of centralized system to oversee everything. However, this does not rule out the use of distributed control, motes and sensor networks. If controllers need to obtain data from everywhere, why not through a smart sensor network?āOne of the most immediate benefits of being able to deploy many inexpensive wireless sensors across a process is a heightened ability to make inferential measurements,ā says Kagan. āMost process plants today take measurements at only about 10% of the possible points. Although they might get better measurements by taking measurements at more points, running the wiring and connecting the sensors is cost-prohibitive. But if the attachment and sensor costs were low enough, as mote technology promises, you could measure at many more points, giving you a much richer process model to work with.āThrough the Hype Curve SmartlyWhere does all this leave us? āI see this technology following a similar path as that of computing itself,ā says Paulonis. āThe first powerful computers were mainframes. This is like a DCS. PCs might be like single-loop controllers. When networking reached the PC, we saw a huge shift away from mainframes. Perhaps something similar will happen with wireless distributed controllers. However, there were some real problems with managing gobs of PCs. There will likely be similar issues managing wireless distributed controllers as others have already pointed out. We now find ourselves with fewer, standardized PCs, a number of centralized servers doing a lot of work, and even a resurgence in mainframes. Personal computing has gone through the hype curve. Wireless distributed controllers will also. There will be circumstances where wireless distributed control is the best solution, others where centralization of control is a better choice, and yet other applications where the DCS approach continues to be advantageous.āGet Those IT Systems Out of Here!
Itās obvious that all control systems require a central supervisory system to issue maintenance orders, advise operators that things require tending to, tune loops, acquire data, prepare reports, perform advanced optimization calculations, maintain the process historian, deal with ERP software, and otherwise perform the thousands of housekeeping and IT tasks required of a control system.But hereās the kicker: The housekeeping and IT systems do not have to be in the processing plant. They could just as easily be distributed upward to a computer center 6,000 miles away.Ā FIGUREĀ 3: THE CONTROL SYSTEM OF THE FUTURE
- Your IT packages are hosted on servers at secure data centers, which are located close to a reliable source of power and high speed fiber. The data center could be at your corporate headquarters, a vendor such as Emerson, or at a āprocess control center,ā which would house software from multiple vendors, such as Honeywell, OSIsoft, SAP, ExperTune, and so on.Ā
- You can have your own processors at the data center, or you can access the vendorās server hardware.Ā
- You connect your plant to the data center in several ways for redundancy: via a private leased high speed Intranet, commercial Internet, and/or dial-up phone service. Obviously, when you communicate via your own high-speed leased line, security is exceptional.
Data from the sensor network is gathered at your plant by a central device, which communicates with the far-flung data centers. The concentrator device can speak to the data centers using encrypted messages. Commands and set point changes coming back to the plant can also be encrypted.
The advantages of such a scheme include renting instead of buying; freedom from upgrading your software every year; freedom from maintenance costs; no worries about hackers or system security; very high speed network operations; excellent reliability; and redundancy. All this has to be worked out in more detail, but the technology is here to do it all and more. Commercial Internet web sites do it every day.Ā
āThe computing and information management parts of control systems are not bound to physical processes,ā ABBās Hausler points out. āAs an example, many parts of today's systems leverage standard IT technology, and could move this into a shared computing environment or even a rental model. There are significant potential cost advantages to this type of approach.ā
Indeed, costs are an issue. āFor users this could be cheaper,ā admits Lazok. āFor suppliers, cheaper may mean less revenue than if they could sell them, particularly on large installations, where license fees for software may be required yearly.ā
There is no question that IT software vendors oppose any changes to their comfy little world. Selling software for millions of dollars, charging hundreds of thousands to maintain it, and requiring periodic expensive updates is making vendors a fortune. But the IT world is rebelling out there. āThe industryās dirty little secret is that, in many cases, their customers do not really need to install an entirely new CRM or ERP system,ā says Charlie Cooper, executive editor of CNET News. āTruth be told, many probably canāt even use the one they already have.ā
Cooper says a customer revolt is looming, and IT buyers are looking for alternatives, such as open-source software or rent-an-application providers. We wish them luck, because their revolt will benefit our industry as well.
The Next Logical Step
The next logical step is to take engineers out of the process plants, and put them in central command centers, where they can supervise the operation of multiple plants. Server-based systems allow you to do just that. āI believe that you will see significant numbers of unmanned process plants all around the world,ā says Alex Johnson, Systems Architect, Invensys Process Systems. āWe have been seeing it already in gas production plants since the mid Ć¢ĀĀ90s. In general, we will be removing people from the bad environments and running a lot more plants remotely. And I think we are going to see it occurring over networks that are not designed solely for the control system.ā
But that is another article.
Latest from Asset Management
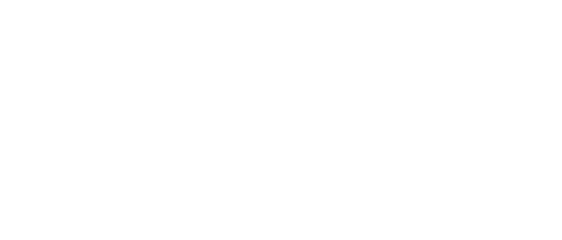
Leaders relevant to this article: