By Scott VanDelinder, Concept Systems Inc.IN THE FOOD processing industry, consistency equates to productivity and quality. Companies that can ensure their production process is consistent and repeatable have a solid basis for expanding their output and avoiding costly quality problems. Achieving higher productivity starts with understanding the process, whether it is continuous or batch-oriented, and that means gathering as much data as possible. In the past, many food processors attacked the data acquisition challenge with clipboard in hand, manually writing down information on process factors such as ingredient weights, temperatures and cooking times. One processor that started out with manual data acquisition is Kettle Foods, located in Salem, Oregon.Kettle Foods makes fried potato chips by weighing potatoes in small batches and dunking them into hot safflower and sunflower oils. Each batch is cooked by hand, carefully tended by experienced chip cooks who stir the chips for even cooking and keep watch to ensure that the chips are cooked to the proper degree of crispness as indicated by their color. While they wanted to continue their hand-crafted cooking process, they felt that their production data collection could be automated to yield positive results: consistent product quality from cook to cook and shift to shift while ensuring compliance with safety and processing goals.In addition to automating the data collection that was already being done, they wanted to capture information that wasnt previously being monitored. With an automated system, they could keep track of operator-adjustable settings and setpoints, and monitor the characteristics of the product throughout the process, starting at the point where potatoes are received at the plant. For example, the system should continuously monitor temperature profiles and recipe parameters, such as the amount of salting.To help assess their needs and put an automated process monitoring system in place, Kettle Foods called in Concept Systems Inc., an Albany, Ore., system integrator. Concept Systems is a Registered Member of CSIA, the Control and Information System Integrators Association, The goal of the system was to interface with existing equipment, while not changing the existing functionality in place. The integration challenge was to provide an interface to older hardware/technology with modern, off-the-shelf hardware, using todays standards. That way, Kettle Foods could get the performance and features available with todays technologies, while reducing the overall investment by using as much existing hardware as possible.Kettle Foods existing hardware configuration included a number of Allen-Bradley PLCs on two separate Data Highway Plus networks. Our reporting solution needed to collect the data from the PLCs via these plant networks and get it to a central database server, which would then be accessible by any client on the business network. One option for connecting the PLCs to the server was to install a communication card in the server which was able to connect directly to the DH+ networks. However, this approach would require the installation of new DH+ cabling between the production floor and the server room, and would require the two DH+ networks to be joined. Also, this introduced potential hardware compatibility issues for future upgrades of the database server. We instead proposed to use an Allen-Bradley ControlLogix Gateway to provide the connectivity between the server and the DH+ networks. FIGURE 1: TOPOLOGY
The PLCs and Data Highway Plus networks existed prior to the isntallation of the new server. The new system plugs in via gateways.
FIGURE 1 shows how the server communicates to the gateway via the Ethernet business network using a network path that already existed. The gateway is equipped with a DHRIO module which provides the connection to the two distinct DH+ networks via separate channels. The DH+ cabling required to reach the gateway location was much less than what would have been required to reach the server room had we connected the server directly to the I/O. Other benefits realized using this approach is the decoupling of the communication hardware from the server (which eliminated the potential hardware compatibility issues), and the ability to easily expand the gateway by adding more communications modules. Kettle Foods plans to add other processing lines (baked chips, for example) to the reporting system later, which may require connection to a third DH+ network.For the database server computer, a solution was needed that would provide not only a good vehicle for the collection and storage of the information, but also a platform that was well supported with easy to use tools for developing reports needed by varied users on the business network.Our solution was to install a rack-mounted PC as the server computer, with a redundant array of disk drives. To collect and display the process information, enabling the evaluation of the performance of critical production assets, we recommended the installation of RSBizWare software, a graphical application suite built on Microsofts SQL Server. The software suite was selected for its flexibility, providing a tool with wizard-driven configuration of data collection points and the ability to create custom transactions for population of user defined data tables. It also allowed the customer to interact with the reports via a web browser plug-in.Another element of the networked software suite, PlantMetrics, provides users with a set of tools to build on the reporting, analysis and management capabilities of the RSBizWare framework. Our system solution also included RSBizWare Historian, a trending tool that captures time series data, and RSBizWare RSSQL, a tool used to commit data to user-defined database tables via event driven transactions. RSSQL is especially useful when collecting a single record composed of several pieces of related data, such as the time, date, storage bin and quality factors for a received load of potatoes.The RSBizWare suite includes a set of tools for generating reports that can include elements such as charts, graphs, and tables. We used the QuickWeb feature of RSBizWare to distribute the reports throughout the organization via a company intranet. QuickWeb allows users to interact with the reports via a web browser without need for additional software on their PC. Using the Web application package, users can call up any of the reports and select the desired time/date range or shift to suit their information needs (See Figure 2).
FIGURE 2: WEB REPORT SCREEN
FIGURE 1 shows how the server communicates to the gateway via the Ethernet business network using a network path that already existed. The gateway is equipped with a DHRIO module which provides the connection to the two distinct DH+ networks via separate channels. The DH+ cabling required to reach the gateway location was much less than what would have been required to reach the server room had we connected the server directly to the I/O. Other benefits realized using this approach is the decoupling of the communication hardware from the server (which eliminated the potential hardware compatibility issues), and the ability to easily expand the gateway by adding more communications modules. Kettle Foods plans to add other processing lines (baked chips, for example) to the reporting system later, which may require connection to a third DH+ network.For the database server computer, a solution was needed that would provide not only a good vehicle for the collection and storage of the information, but also a platform that was well supported with easy to use tools for developing reports needed by varied users on the business network.Our solution was to install a rack-mounted PC as the server computer, with a redundant array of disk drives. To collect and display the process information, enabling the evaluation of the performance of critical production assets, we recommended the installation of RSBizWare software, a graphical application suite built on Microsofts SQL Server. The software suite was selected for its flexibility, providing a tool with wizard-driven configuration of data collection points and the ability to create custom transactions for population of user defined data tables. It also allowed the customer to interact with the reports via a web browser plug-in.Another element of the networked software suite, PlantMetrics, provides users with a set of tools to build on the reporting, analysis and management capabilities of the RSBizWare framework. Our system solution also included RSBizWare Historian, a trending tool that captures time series data, and RSBizWare RSSQL, a tool used to commit data to user-defined database tables via event driven transactions. RSSQL is especially useful when collecting a single record composed of several pieces of related data, such as the time, date, storage bin and quality factors for a received load of potatoes.The RSBizWare suite includes a set of tools for generating reports that can include elements such as charts, graphs, and tables. We used the QuickWeb feature of RSBizWare to distribute the reports throughout the organization via a company intranet. QuickWeb allows users to interact with the reports via a web browser without need for additional software on their PC. Using the Web application package, users can call up any of the reports and select the desired time/date range or shift to suit their information needs (See Figure 2).
FIGURE 2: WEB REPORT SCREEN
A typical report screen, available via web browser, can be customized for the user's information needs.
THE KETTLE FOODS batch processing requires that the installation use PlantMetrics in a non-conventional way. Rather than monitoring the equipment to calculate OEE (Overall Equipment Effectiveness) values, they employ an event-driven data collection scheme to log the process data only when it changes. This method is well suited to a process where individual batch tracking is crucial, the data changes slowly, and it collects operator-modified setpoint values. Using the software to configure this event-based data collection provides the companys engineers with a simple interface for making additions and revisions to the collection settings.The results seen so far by Kettle Foods have been impressive. Production staff can now track near-real-time processing performance in both the cooking and packaging areas. This drives the quality and efficiency goals down to the operator level where real changes can be effected. Engineering can track trends and match production data with quality data to determine root causes of production and quality problems and to determine the impact of process improvements. Downtime between shifts and batches, packaging changeovers, and product has been reduced. Combined, the data acquisition and reporting tools have allowed Kettle Foods to increase its effective production capacity by 10-15%, thereby delaying costly capital expansion.
Scott VanDelinderis a process engineer with system integrator Concept Systems Inc., in Albany, Ore., with experience in the food processing industry. He can be reached at 541/791-8140.
THE KETTLE FOODS batch processing requires that the installation use PlantMetrics in a non-conventional way. Rather than monitoring the equipment to calculate OEE (Overall Equipment Effectiveness) values, they employ an event-driven data collection scheme to log the process data only when it changes. This method is well suited to a process where individual batch tracking is crucial, the data changes slowly, and it collects operator-modified setpoint values. Using the software to configure this event-based data collection provides the companys engineers with a simple interface for making additions and revisions to the collection settings.The results seen so far by Kettle Foods have been impressive. Production staff can now track near-real-time processing performance in both the cooking and packaging areas. This drives the quality and efficiency goals down to the operator level where real changes can be effected. Engineering can track trends and match production data with quality data to determine root causes of production and quality problems and to determine the impact of process improvements. Downtime between shifts and batches, packaging changeovers, and product has been reduced. Combined, the data acquisition and reporting tools have allowed Kettle Foods to increase its effective production capacity by 10-15%, thereby delaying costly capital expansion.
About the Author |
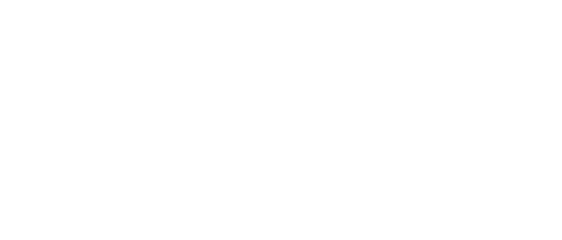
Leaders relevant to this article: