Thermal mass flow gas measurement has been around for many decades, but like any long-accepted technology, it's accompanied by some equally long-term nuisances that everyone came to accept as unavoidable. Most notably, thermal mass flowmeters use metal RTDs encased in organic potting compounds, but these wetted sensors cause the signals they acquired to drift as they're heated and cooled, and expand and contract over time. Plus, they typically only measure flow in one direction, can't detect reverse flow when needed, and their associated electronics can be complex and difficult to use and service.
Fortunately, these headaches are largely cured by Endress+Hauser's new Proline t-mass F/I 300/500 thermal mass flowmeters with a completely new design for a all-metal sensor that's free of drift, and imparts long-term stability for measuring pure and mixed gases. It also uses Gas Engine software and dataset for flexible, selectable programming and measurement of 22 gases, as well as mixtures of them with up to eight components. Also, if build-up or even condensate droplets accumulate on the sensor, or a pulsating flow occurs, they're detected by Endress+Hauser's self-diagnostic Heartbeat Technology, which generates an alert or alarm.
"We're using a new pressurized sintering and co-extrusion process with very tight tolerances for our RTDs, and it's giving us a compact and solid mass with respect to their temperature, pressure and heat," says Adam Booth, flow product marketing manager at Endress+Hauser. "This means no potting compound is required, which enables t-mass flanged and insertion flowmeters to have a fully metallic, 'dry' sensor with uniform thermal expansion that eliminates all drift, and is easy to remove and reinsert for easy cleaning in case of fouling."
Beyond its enduring stability, t-mass F/I 300/500 ensures ±1.0% accuracy with ±0.25% repeatability, even when process and ambient conditions fluctuate. Low-pressure and low-velocity gas flows can also be measured easily due to their 1,000:1 turndown. They can perform at process temperatures up to 180 °C (356 °F) and pressures up to 40 bar (580 psi).
Because gas flows don't just slow, but sometime run in opposite directions, t-mass F/I 300/500 can also perform optional, bi-directional flow detection, measurement and totalization. "Where typical thermal mass flow devices measuring in one direction employ two RTDs to check ambient temperature and added heat, t-mass employs a third RTD to identify flow direction," adds Booth. "This can help in cleanroom applications that periodically reverse flows, or in comparing performances between facilities."
In addition, t-mass F/I 300/500 was developed in accordance with IEC 61508 and SIL 2, it can also serve as the preferred system in safety applications, and clearly categorize and immediately indicate any device or process errors in accordance with NAMUR NE107 requirements. Similarly, if the flowmeters encounter liquids or flood conditions while operating, they're reported to be the first thermal mass device that complies with NEMA 6P and IP68 submergence standards, which allows its sensor to be submerged up to 1 meter.
For increased flexibility during configuration and operations, t-mass F/I 300/500 possesses local display, web server, WLAN and operating tools, such as FieldCare and HART handheld terminal, and digital communications inclusing HART and Modbus RS485 protocols. These connections give users direct access to all diagnostic, configuration and device data without added software or hardware. Finally, t-mass F/I 300/500 stores data using the HistoROM concept, which ensures data security before, during and after servicing. All calibration data and device parameters are stored securely on the HistoROM module, and are automatically reloaded following maintenance.
Booth reports the 300/500 program was launched in 2017 to simplify the electronics and ease the engineering of several Endress+Hauser product categories, so they didn't require special hardware or software. Components joining 300/500 also increase device flexibility, achieve Class 1/Divison 2 compliance, add UPSs and configurable I/O, and have WLAN-enabled displays that can link to laptops, tablets PC and smart phones. "We started with Coriolis flowmeters a few years ago, and just finished integrating ultrasonics with 300/500," says Booth. "Since mass thermal flow just gained its new sensor, we decided it was a good time to add them, too."
For more information, visit https://www.us.endress.com/en
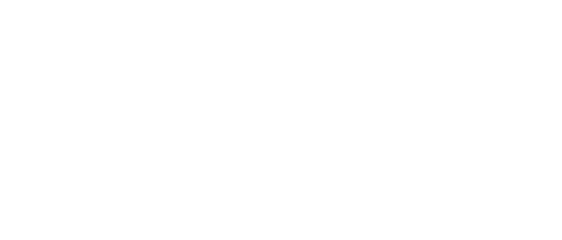
Leaders relevant to this article: