SCADA Provides an Organization with Ability to Monitor, Control Treatment
Figure 1: The four primary subsystems of a supervisory control and data acquisition (SCADA) system are sensors, controllers, communications systems and human-machine interfaces.
Supervisory control and data acquisition (SCADA) provides an organization with the ability to monitor and control treatment, collection and/or distribution processes either remotely or from a central location. Today, many public water and wastewater utilities have installed or are planning to install a SCADA system. While there are a variety of reasons why utilities install SCADA, the primary drivers are to increase efficiency, reduce costs, enhance decision-making and simplify operationsA typical SCADA system consists of four primary subsystems (Figure 1):
- Field sensors such as pressure switches, level transmitters and flowmeters monitor equipment and measure process variables;
- Programmable logic controllers (PLCs) or other smart data concentrators/controllers vary in size from small relay replacers up to large process controllers with multiple input/output (I/O) types capable of executing complex control strategies;
- Communications systems vary widely depending on the application and include Ethernet, wireless Ethernet, licensed radio, spread-spectrum radio, DSL, cable and fiber-optic networks;
- Human-machine interface (HMI) systems typically include a server and several clients. They also can include tablets to support mobility needs, as well as specially designed plant-floor stations.
Most utilities today use SCADA only for monitoring and controlling process equipment. From a control room, operators engage the system from one or more HMI workstations. When equipment starts or stops, sensors measure the change at the field level, and transmit a signal to the PLC, which then communicates to the HMI system, where the graphical elements change color to reflect current conditions. When an anomaly occurs, the same process is repeated, and the HMI system alerts operations staff.
[pullquote]
Besides monitoring and control, many utilities leverage their SCADA system to produce the data for their operational reports. Many organizations manually transfer report data either by retyping or by running a script against the file containing SCADA data., both of which are labor-intensive and subject to translation errors, so there’s an inherent need to connect SCADA to other systems to allow for automated data transfers.
SCADA Requires Security
SCADA systems include computers and other intelligent devices integrated to critical equipment, and performing critical tasks essential to meeting the organization’s operational goals. SCADA is critical infrastructure and must be protected from cyber threats.
Cybersecurity is a serious concern, with ongoing reports of threats and attacks on commercial vendors. Fortunately, most legacy systems are inherently secure by virtue of their design. Many systems are “islands” and have no external connections to the Internet, limited connectivity to organizational users and servers that are physically secured to prevent the introduction of malware from portable media. While this level of security keeps the SCADA secure for monitoring and control, it creates challenges for sharing SCADA data with other systems.
Figure 2: Connecting to business systems through an historian improves security and opens opportunities to leverage process data in applications that pay off by reducing labor and improving accuracy.
There are many ways to address the issue, one of which is to create SCADA connectivity through the historian. The concept is simple: interconnect the historian to receive near-real-time data from the SCADA system, then allow it to be pulled through specific connections from defined business systems through a firewall (Figure 2). In this scenario, data is pushed one-way from the SCADA system, and it remains isolated from the outside world. Organizational SCADA data needs are met by establishing connectivity under defined rules through the firewall and only to the historian.SCADA Data Can Do More
The idea of using SCADA data beyond monitoring and control is not new, and in most cases, it is being done manually. Interconnecting various systems allows for rapid transfer of data with no human intervention beyond initial setup. The value of electronically interconnecting various systems is realized primarily in two ways: labor savings and data accuracy. The savings are derived from improved efficiency because staff will no longer need to perform the manual data transfers or expend time validating data entries.
Some examples of leveraging SCADA data:
Ed Melanson, PE
Vice President, T&M Associates
[email protected]m
Step by Step
A key step in integrating various data systems to bring value to the organization is determining data-sharing needs by system, including specific data flows necessary to achieve operational goals. This effort can be completed in-house or with the aid of a consultant. The process generally includes developing a comprehensive list of data systems within the organization; engaging stakeholders through workshops to discuss data needs; performing field interviews with staff charged with collecting data; interviewing end users to understand their data needs; creating a data flow diagram to document data needs by system; developing a summary report for stakeholder validation; evaluating systems to determine specifics of data transfers (protocols, security, database requirements); developing a list of overall improvements; creating a project scope document, and procuring and implementing the improvements.
SCADA is one of many tools water and wastewater utilities use to meet their daily operational needs. SCADA serves as the backbone of critical infrastructure for monitoring and control, and also is capable of serving as a primary data producer of key organizational data for use by other business systems. Having the ability to link these systems to promote sharing of data provides an organization another means to improve efficiency while reducing overall costs. The up-front process requires planning and analysis, strategic implementation and ongoing assessment, but is easily achievable for most organizations and provides significant benefits.
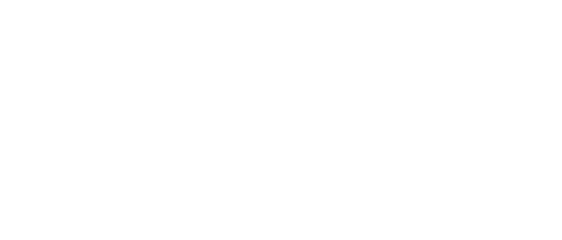
Leaders relevant to this article: