By Dick Caro
I have done a study regarding the use of a combination of variable-frequency drives (VFD) and pumping in flow control. The question I asked many users was "Why don't you use a VFD on an electric motor driving a pump for flow control instead of using a control valve?" Then I had to explain that the VFD converted a normal AC induction electric motor into a variable-speed motor, and it could be used to drive a centrifugal pump at variable speed to change the flow rate in the line, making the control valve unnecessary. This was news to more than 90% of the instrumentation engineers I interviewed. Their next question to me was "Why would I want to do that?"
Benefits
My standard response was that using the VFD/pump combination instead of a control valve had these benefits:
- Dramatic energy cost reduction obtained by elimination of the pressure drop across the pump;
- Better control by elimination of control valve hysteresis or stickiness;
- Faster and more responsive flow control due to elimination of the control valve mechanical action;
- Elimination of a source of fugitive emissions;Ā
- Electricity savings from the improvement in plant power factor.
However, I have yet to be able to confirm all of these benefits from anyone who actually used the VFD in this way.
Barriers
Respondents to my survey said the main barriers to using the VFD/pump are these:
- Tradition. "We always use a control valve";
- The VFD is purchased by a different purchasing agent than the one who buys control valves;
- VFDs have a history of being unreliable;
- Our pumps are not designed to be used at variable speeds and would be too non-linear to use for control;
- We have never considered using an alternative to a control valve.
Analysis of Benefits
If the energy savings were small, then this would be a moot point. However, there are so many liquid flow pumps in processes that pump up to a high head, only to take that energy loss as pressure drop across a control valve, that this source of energy loss may be as much as 25% of the energy used to operate a refinery, paper mill or chemical plant. Then too, if we designed our processes from the beginning with the VFD/pump, we could use much smaller electric drive motors.
There are two factors at work here. We know that flow rate is linear with centrifugal pump rotational speed from the pump affinity laws, which directly addresses the perception of non-linearity in Item 4 above. We also know that the electric power needed to drive the pump at lower speeds to produce the reduced head then required is proportional to the cube of the speed ratio. Therefore, by removing the control valve completely from the flow path, the amount of energy saved is much larger than one would expect. Of course, reduced load on the electric motor means longer motor service life as well.
One of the characteristics of the VFD/pump combination is speed of response. Unlike the control valve that requires time to reposition the plug to change the pressure drop, the electric motor driving the pump will respond within a few cycles of the new frequency to operate at the new synchronous speed setpoint. The speed of the VFD/pump in responding to the new flow setpoint may be so rapid that the speed setpoint may need to be ramped to prevent the hammer effect that may occur in the process-filled liquid system when the speed setpoint is raised.
It is well known that the most often cited problem in tuning of PID control loops is the variable hysteresis introduced into the flow loop by control valve stickiness. The control valve also introduces a lag due to mechanical motion of the valve motor itself. Control loops that have been optimally tuned at plant startup must gradually be detuned as the stickiness of the control valve builds, or the loop may become unstable. In fact, most modern DCSs contain loop auto-tuning software that effectively compensates for control valve hysteresisāup to a point. The loop is gradually detuned, which actually causes the process setpoints to be set to allow for the increased process variability resulting from the detuning of flow and pressure control loops. Today, we seem to accept this kind of sub-optimal process performance, but we can do better by replacement of the major source of errorāthe control valveāwith a VFD/pump.
The benefit obtained from the elimination of fugitive emissions known to originate at the packing of the control valve stem is obvious when the control valve is eliminated. A less obvious benefit of using a VFD rather than discrete motor starters and electrical contactors is operation at a near-linear power factor. The VFD presents itself to the AC power line as a resistive load with a unity power factor. When an AC induction motor is placed across the power line, as in a conventional control valve situation, the induction motor usually presents itself to the AC power line with a power factor that can vary over the range of 0.7 to 0.9, depending on the load and ratings on the motor. This power lag means that the amount of electricity consumed by the plant for each directly wired AC induction motor is its metered electricity divided by the power factor. In many plants with many such directly wired AC induction motors, the electric power utility may require the use of parasitic capacitors placed across each phase of the AC line just to correct the power factor. Parasitic capacitors require considerable investment and are a constant load for the plant consuming electricity. Use of VFDs eliminates the need for parasitic capacitors since they self-correct for power factor within their own circuits.
Analysis of Barriers
To be fair, the use of the VFD/pump arrangement has its negative side as well. Tradition is a powerful deterrent. Textbooks on process control do not teach that there are any alternatives to use of a control valve. Since the pump electric motors and their switchgear are purchased as part of the plant electrical system, it is natural that a VFD replacing motor starters and contactors are considered "electrical" and not instrumentation. These are human-created categories and can be overcome with proper education and executive decisions.
Since the invention of the AC VFD in May of 1967, the electronics required to rectify the incoming three-phase AC to DC and the regeneration of a different frequency AC current has depended upon high power-bipolar semiconductors. High-power semiconductors have evolved over time to become more reliable and more efficient. However, they have not been able to match the pace of development of low-power semiconductors for use in general electronics. Today's AC VFDs all use multiple insulated gate bipolar transistors (IGBT) for each of the three phases of the AC line to regenerate the variable-frequency AC power. Multiple IGBTs are used because the rated power level cannot be handled by a single IGBT, and use of multiple IGBTs provides redundancy when one fails. These are power-handling semiconductors and do fail occasionally due to heat generated within their circuits. Builders of VFDs have compensated by making failure detection and replacement of VFD circuits rapid and easyābut they do fail. Our question is: would VFD maintenance impact flow control as often as control valve mechanical maintenance to overcome wear and stickiness?
AC VFDs do not generate perfect sine waves at the new frequency. As a result, the power supplied to electric motors contains higher frequency components called harmonics that are filtered out by the windings of the AC induction motor. Harmonics can cause vibration in the AC motor windings as well as heat, as the harmonics power component is dissipated by the reluctance of the motor windings. When a new installation is made knowing that a VFD is to be used, motors can be supplied that are designed to withstand the vibration and heat generated. However, in a retrofit installation using an existing electric motor with a new VFD, the motor will be oversized and will probably work at the new reduced speed and power levels in spite of the harmonics and overheating, but should be closely monitored. Furthermore, when that motor is replaced, it should not be with the same ratings, but with a smaller motor designed for use with a VFD.
Conclusions
It seems clear to this author that using a VFD/pump combination to replace the use of a AC line-powered electric motor and a control valve is a superior way to do flow control and reap large benefits in lower energy consumption with better energy efficiency. However, it is not clear that the human factors will be easy to overcome. Our traditions are all bound by use of control valves as instructed by our textbooks. Suppliers of VFDs have not focused on control valve replacement as an alternative in their marketing efforts. Instrument departments have not cross-trained their repair technicians to repair failed VFDs. There is also the potential for improved process control from elimination of the problems of control valves. We are still waiting for a suitable number of users to actually test these factors in real plants.
Dick Caro is president of CMC Associates.
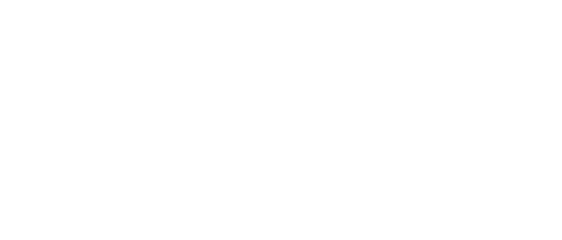
Leaders relevant to this article: