MAINTAINING and replacing the tubes, pipes, and brackets used in traditional process analytical sampling systems can take a lot of time. Just saying it can be a mouthful. Technicians have to check drawings, disassemble the system, remove worn or faulty parts, bend new tubes, rethread pipes, check fitting unions, coordinate I/O components, remount brackets, and complete other application-specific tasks. These jobs typically take two to four hours or more, and even then breaking and reinstalling seals can damage their surfaces, and cause chronic leakage problems.
So, its no wonder that process analytics users long sought a way to make sampling systems easier to repair and reconfigure. However, even though some found and developed a modular solution that allows them to switch out a regulator in 60-90 seconds and doesnt leak later, making it a mainstream reality has produced some unforeseen delays and technical snags on the way to the desired happy ending.
Sampling History
Analyzers were first added to industrial process systems in the 1940s, and theyve progressively evolved from bathtub-sized enclosures into smaller, less intrusive, intrinsically safe packages. However, it wasnt until the late 1990s that some process analytics users, reportedly from U.S. refineries on the West Coast, observed uniform, surface-mount components being used in semiconductor processes, and reasoned that their sampling systems could use a similarly standardized strategy. These semiconductor components include 1 1/8-in. gas sticks and metal o-rings used that help measure gases used in semiconductor manufacturing.
These users formed the New Sampling/Sensor Initiative (NeSSI) with help from the Center for Process Analytical Chemistry at the University of Washington in Seattle. The groups initial, surface-mount strategy was adapted for oil, gas, and chemical processing applications by the ISAs SP76 committee, and became the basis for the international ANSI/ISA-76.00.02 standard for sample flow control, conditioning, and analysis, which was released in 2002.
The modular standard requires compliant sampling systems to be built onto a standard substrate from closely-joined, 1.5-in-square manifolds with 0.110 sample-transfer ports, which are attached with four Allen wrench screws. These metal Lego blocks allow users to switch out components from different manufacturers without having to switch out a whole sampling system.
Another of NeSSIs physical advantages is that it can perform all same functions of a 30x60-in. legacy sampling system in a 16x20-in or 12x16-in space. This can add up to a lot of savings in refinery that may have dozens or hundreds of sampling systems, and where a square foot might be worth $1,000, depending on its location. In addition, a 1-sq-ft legacy valve system can be replaced by a 1.5x3x3-in NeSSI valve.
Ive been working with sampling systems since 1969, and NeSSI is the biggest advance in process analytics in the past 50 years, says Bob Sherman, an ISA fellow and industry specialist for process analytical systems at Circor Tech, which manufactures modular, NeSSI-compliant devices. Whenever people move from legacy sampling systems to modular substrate systems, they find they can optimize filters much more easily, for example, and achieve many new and far more efficient capabilities.
Student teams had 45 minutes to use a box of substrate components, including Circor Techs µMS³ modular substrate sampling system, to assemble this and other functional modular sample conditioning system during ISA Expo 2005s International Student Games in Chicago.
NeSSI is cheaper to build and cheaper to own. Its reliability is greater, and it delivers more operating and safety credits than traditional analyzer systems, says Jeff Gunnell, lead specialist for process analytics at ExxonMobile in the U.K.
The Communications Race
Since it was first conceived and started development, NeSSI has been organized into three successive generations. Generation 1 covers the mechanical components, which were first available in 2001-02. These include flowmeter switches, regulator valves, filters, and other devices. Dave Veltkamp, senior research scientist at CPAC, says NeSSIs emergence has helped reinvigorate the fittings companies, such as Swagelok, Parker Hannifin and Circor Tech, which modified traditional valve systems to serve in surface-mount settings, and also began making the substrate onto which the surface-mount components fit.
Generation 2 covers and is seeking to define how electrical signals and power are delivered to NeSSI devices. These tasks include how NeSSi should build multidrop networks and how to communicate temperature and pressure signals. However, the biggest stumbling block has been how NeSSI should define its communication network. Several candidates have been evaluated, and each is developing the necessary modifications to be used in NeSSI sampling systems.
When we released Generation 2s specification in 2002, we thought CPACs NeSSI steering committee could simply tell people what communications network we wanted to use, and that all NeSSI developer would have to use it, says Veltkamp. However, once we looked at what was available, we found that nothing met all of NeSSIs requirements. So, were being more pragmatic now, and were letting the users and vendors decide what bus they want to use. The component vendors have agreed to support whatever bus the users request when working with NeSSI or when they order a system.
We got a bit ahead of ourselves by saying that NeSSI systems had to be intrinsically safe, but we didnt look hard enough at what we had to do make this a reality. So, NeSSI has languished some because of this lack of an available intrinsically safe network for NeSSI to specify.
So far, Veltkamp reports that CANbus does much of what NeSSIs end users want to do, but end users want an intrinsically safe network, and CANbus isnt intrinsically safe yet. So, CAN in Automation is working with NIST on coordinating and designing an intrinsically safe bus for NeSSI. The two organizations are testing a draft specification, but it will be about a year before they can release an intrinsically safe bus for NeSSI.
Similarly, Foundation fieldbus (FF) is intrinsically safe, but Veltkamp adds its chipset was too big for NeSSIs existing, physical footprint. Profibus hardware also was too big because it uses the same chipset as FF. Emerson Process Management recently offered to release it chipset for NeSSI to vendors that want to use FF for their NeSSI systems.
Meanwhile, Siemens reportedly is planning to use i2C in its NeSSI devices. This is a short-haul, board-to-board communication method thats usually used to communicate within individual devices. However, i2C may actually need less renovation than other communications buses to work with NeSSI devices, according to Veltkamp.
Though it might seem like the large process control vendors are seeking to establish proprietary holds on NeSSIs communications methods in the same way theyve perpetuated proprietary fieldbus standards in recent years, Veltkamp says its unlikely that NeSSi will succumb to these forces because its end users decide what functions they want, and its up to the vendors to meet those demands. For example, NeSSI mechanical requirements already are settled in Generation 1, and vendors will likely have to comply with the open standards that users will want to see included in Generation 2.
Besides including electronic device description language (EDDL) communications in its specification, including FF and Profibus, Veldkamp adds that NeSSIs developers also plan to interact with OPC and wireless technologies.
When everyone finally settles on implementing Generation 2s communications, NeSSIs developers plan to work on Generation 3, which is a wish list for building a platform for getting microanalytical devices on NeSSIs substrate. Though no specification has been developed for Generation 3, it eventually will allow lab-on-a-chip capabilities, bolt-on NeSSI spectrometers, and other advanced devices and capabilities.
Gaining Momentum
NeSSIs supporters say the good news is that sales of its components are more than doubling every year, but the bad news is that they expected much larger, faster sales increases given NeSSIs huge benefits and potential savingseven though NeSSIs components initially cost about 20% more than traditional tubing and brackets. Despite all of NeSSIs demonstrated advances and benefits, however, many potential end users reportedly remain reluctant to try it. This might be the result of users traditional if it aint broke, dont fix it attitude, and that fact that many of them (and most of the rest of us) are still like the two little boys in the legendary Life cereal commercialI aint gonna try it. You try it.
End users hesitance on NeSSI also may come from the feeling that its benefits are just too good to be true. Efficiency gains of a few percent or even a fraction of a percent can produce big savings in process applications, and so users can probably be forgiven for viewing comparatively huge, double-digit improvements as somewhat unreal.
We had our own system integration company several years ago, and the first modular system we put in was for cleaning up samples, and reading vapor pressures on a gasoline blender. The refiners technician said his application was just going to break our new modular components, but eight weeks later he was asking How many more can we get? These components became a de facto standard for them, explains Sherman. The question potential users have is does NeSSI have staying power, or is it just another flash in the pan? Over the last six months, I think were beginning to reach critical mass.
Sherman adds that one major refiner previously required its technicians to go out and read rotometers and pressure gauges, and couldnt use legacy flow controllers and pressure transmitters because they had too many leaks and required too many adjustments. This refiner now uses mass flow controllers and NeSSI-based pressure transmitters that report directly to its control room, which means technicians only need to go out if an exception report is generated because the system isnt operating in range.
In fact, NeSSI may be on the verge of making exactly the big leaps in adoption its fans desire because there are reportedly several requests for proposals (RFPs) for several hundred to several thousand NeSSI systems in projects likely to be built soon. For example, ExxonMobil reportedly plans to add NeSSI-enabled 150 GCs and 300 continuous gas analyzers to a nine-plant chemical complex that its building in the Singapore area. Likewise, a major, unidentified, Gulf Coast-based hydrocarbon producer reportedly also will soon issue an RFP for 3,500 to 5,000 modular sampling systems.
In the first quarter of 2006 (1Q06), ExxonMobil specified that NeSSI is the preferred way to do new construction in plants with sampling systems, which take uniform sample from a process stream, present them to an analyzer, and return them to the process, add Veltkamp.
Still, even though hundreds NeSSI devices have been operating successfully in the field for several years, many traditional users wont give up their doubts. Even when users are putting in a NeSSI system, they still say, I know its going to fail, so we want to wait and see what the failure mode is. And, two years later when the NeSSI system hasnt failed, they still say, Were still just waiting until it fails.
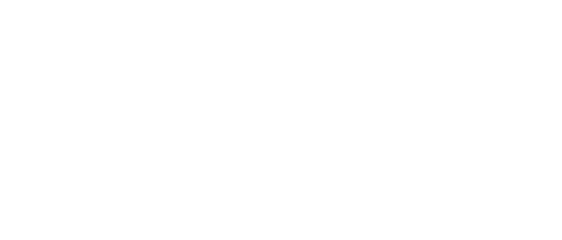
Leaders relevant to this article: