With a new generation of Ethernet-APL products due to hit the process automation marketplace this year, the process industries will finally be able to boast a unified Ethernet architecture that reaches from intrinsically safe field devices all the way to the cloud. Sure, device bandwidth will be much faster, allowing ready access to process variables as well as all that secondary data, but Ethernet-APL will also deliver substantially more electrical energy to those devicesāallowing more memory, more powerful microprocessors and unprecedented capabilities in the digital field.
To help explore what new field device capabilities Ethernet-APL will make possible, Control caught up with Jonas Berge, senior director of applied technology for Emersonās Automation Solutions business.
Q: To start things off, perhaps you can talk a little bit about how much more bandwidth and power Ethernet-APL can deliver to field devices compared to analog, 4-20mA HART or even fieldbus technologies?
Senior Director, Applied Technology, Emerson
A: Letās start with bandwidth numbers. Ethernet-APL runs at 10 Mbps, while HART runs at 1.2 kbps, so Ethernet-APL really is more than 8,000 times faster. And fieldbus runs at 31.25 kbps, so Ethernet-APL is still more than 300 times faster. Consequently, Ethernet-APL can carry lots more data, which enables more devices on a network, and it also enables other types of devices with higher-bandwidth requirements.
And Iām glad you brought up the difference in supplied power because it's important but often forgotten as we get excited about the bandwidth. Ethernet-APL provides not only communication but also power over the same two wires, just like analog 4-20 mA/HART loop power and the bus power provided by fieldbus. For two-wire, loop-powered HART devices, power is limited by the 4-20 mA signal; they must be able to operate on less than 4 mA. This isnāt much, and it limits what types of devices can be powered.
Now, depending on the application, Ethernet-APL provides more than half a watt or even more than one watt of power to a device. Thatās on the order of 10 to 20 times that of a 4-20 mA device. So, devices that previously had to be separately powered can soon be powered over that same single pair of wires. No separate power cable needs to be pulled.
Q: What new sorts of possibilities does this new, higher power and bandwidth allow for existing instruments?
A: Letās continue with implications of the higher power supply. So, 4 mA is sufficient to loop-power many familiar instrument types, such as pressure, temperature, level and some flow transmitters like differential pressure and vortex, as well as liquid analyzers like pH and conductivity. But 4 mA is not sufficient to loop-power certain other types of flowmeters, such as larger pipe-diameter, magnetic and Coriolis meters. Today, these larger meters need separate power.
In the future with Ethernet-APL, many of these device types will be two-wire powered, thus simplifying installation. But even devices that already are two-wired powered today can benefit from the greater power provided by Ethernet-APL. More power means more powerful microprocessors that enable more advanced signal processing. This benefits some types of measurements, such as those based on radar and ultrasound, which become more accurate and more robust with better signal processing.
More power also means faster updates for these measurements. For the types of instrumentation like transmitters and valve positioners we're already familiar with, greater bandwidth means you can put more devices on a network than with traditional fieldbus and still get fast response time. That is, you donāt need as many networks as you did with fieldbus. It also gives you greater spare capacity and flexibility to later add more devices to a network, without having to reengineer with an added network and junction box.
Ethernet-APL also provides greater flexibility to accommodate changes late in a greenfield project or even after startup without extensive reengineering. Such flexibility is critical to initial project execution and later for the plant to stay evergreen.
Q: Can you give some examples by instrument type (valve controller, radar tank gauge, Coriolis meter, magmeter, etc) of the new capabilities it will afford?
A: For a radar level transmitter, more power means it can use frequency modulated continuous wave (FMCW) sensing technology instead of pulsed radar. FMCW has greater temperature stability and is better at handling disturbing echoes, particularly in tall tanks. FMCW requires advanced signal processing, but with added power from Ethernet-APL, transmitters will be able to provide faster updates than in the past. A further benefit of high bandwidth is that during instrument commissioning you donāt have to wait for the radar echo curve to slowly load in your setup app. It arrives instantly and can stream like live video, so you can adjust the installation and see the echo curve dynamically. You can see disturbances from agitators etc, inside the tank, so they're easier to commission.
The Coriolis and magnetic flowmeters we already spoke about, as well as ultrasonic flowmeters, can now move from 4-20 mA or RS485 Modbus or regular Ethernet to instead use Ethernet-APL without needing separate power.
Two-wire gas analyzers might also be possible. Imagine installing the gas analyzer in the field near the process sampling point, with minimal sampling lines, instead running Ethernet-APL back to the people that need the data. This is a whole lot easier to build and maintain than constructing analyzer shelters and laying and maintaining long sampling lines.
HART devices that generate a lot of secondary data about themselves and about the process they serve will particularly benefit from Ethernet-APL. Engineers and technicians will be able to immediately see things that they hadn't beforeāin near real-time and from the safety of the control room, or from their offices anywhere around the globe.
Q: What sorts of brand-new instrument types might Ethernet-APL enable?
A: Well, thanks to digital transformation, IIoT, Industry 4.0, and the 4th industrial revolution, there's huge interest in equipment condition monitoring and analytics, and not just for large critical turbomachinery. Turbines and compressors already have vibration monitoring and in some cases prediction, which is very successful, but these āonlineā systems are expensive.
Plants now want to do that kind of condition monitoring on their second-tier, essential assets such as pumps, fans and conveyorsābut at lower cost, since it's a less demanding application. As you know, some of this is done by wireless transmitters. But for some assets, plants deploy āasset monitors,ā edge devices that sit in the field, monitoring multiple assets. Today they use regular Ethernet with separate power, and they help plants move to predictive maintenance for an ever-greater portion of their equipment. In the future, these could use Ethernet-APL to be even easier to deploy.
But letās think about Ethernet in the office. Itās not just connecting laptops and servers to the Internet. Ethernet also connects printers and scanners. In our office, the phones are on Ethernet, the CCTV cameras are on Ethernet, the video wall display is on Ethernet, and I'm sure there's more. Ethernet is the single common infrastructure. There are no separate phone lines, no separate CCTV cabling, and so on. A single Ethernet infrastructure, instead of maybe five separate infrastructures in the past.
Ethernet-APL can do the same for the process area in the plant. It has the potential to not only take the place of the 4-20 mA infrastructure but also RS485 infrastructure, video cabling infrastructure, and regular Ethernet infrastructure in the plant areaāall into a single common Ethernet-APL infrastructure instead of the five dedicated infrastructures we have today. It's a dramatic simplification.
For instance, many plants want to be able to see foaming, pebble size, or stratification, etc, in their processes. Today, they send a field operator out to check, peeping through an inspection window. In the future, they can just drop in an Ethernet-APL video camera. Iām not talking about your perimeter CCTVāthat will still use regular Ethernet, but Iām talking video playing a more important role in the process area in the future. You could easily drop in an Ethernet-APL HMI panel in the process area if it would help certain tasks.
Perhaps, we'll see LiDAR in process applications, too.
Some of these things are theoretically possible today; you ājustā need to lay hundreds of meters of Ethernet fiber and power for that one device. But it's too costly for a single use case, so it doesn't get approved. But once you have Ethernet-APL in every corner of the plant, dropping in cameras, HMI panels, LiDAR, asset monitors, flowmeters and gas analyzers becomes easy and low cost, paving the way for continuous improvement.
Q: One neat thing about Ethernet-APL is that it specifies only the physical layer, which means it can accommodate multiple different protocolsāeven on the same pair of wires. In practice, will we have multiple different protocols running on the same wires, or will there be some segmenting of networks to separate, for example, electrical equipment speaking Profinet over Ethernet-APL, from process instruments speaking HART-IP over Ethernet-APL?
A: Well, Ethernet-APL supports IP and with that it enables multiple application protocols. So, with Ethernet-APL it's no longer a question of HART or Modbus or Profibus, it's HART-IP and Modbus/TCP and Profinet. Plus, other protocols such as HTTPS for web browsing and RTSP for video, all on the same wire at the same time. And there will also be OPC-UA to HMI panels and analytics.
Having said that, it's good engineering practice to have subnets and security zones. So, there will be a subnet for the electrical gear in that room, and most of the traffic on that subnet might be Profinet, but it will not be purely a single protocol like in the bus days. There will also be HTTP and OPC UA. And electrical gear may continue to use regular Ethernet since the motor control centers are usually indoor with short distances. And, yes, Ethernet-APL instrumentation will most likely use HART-IP, but the subnets for instrumentation wonāt host a single protocol. There will be HTTP and OPC UA there as well.
The mix of devices and use-cases sharing the same infrastructure and the mix of software tapping into their data necessitates a mix of protocols. The benefit of Ethernet is shared infrastructure, and you canāt do that without mixing protocols. Back to the office analogy, the beauty of IP is that one protocol doesnāt have to do everything. In the office, we use HTTP for web browsing, FTP for file transfer, and IMAP for mail, with each protocol specialized for a particular function. Ethernet-APL will be just like that.
Q: From an installed base perspective, the global community of instrumentation technicians and engineers is far more comfortable with the HART protocol when it comes to managing and communicating with smart instruments than any other protocol. Doesnāt it make sense for folks to use the same protocol, the same tools and interoperability ecosystem that most of them have been using for more than 30 years as they begin to embrace Ethernet-APL instruments in parallel with legacy HART instruments?
A: Absolutely. And think about the mix of device signal types. Letās say you, right now, are planning to build a plant based on Ethernet-APL. We'll see Ethernet-APL in DCSs and PLCs very soon, so no problem for the core process control of the main plant to go Ethernet-APL. But what about the safety system, fire and gas system, and machinery protection?
I think they'll be slower to adopt Ethernet-APL, so for now, will tend to use 4-20 mA/HART devices. I also believe package unit vendors like boiler manufacturers will take a while to adopt Ethernet-APL, so they'll also ship modules instrumented with 4-20 mA/HART for now. And, like we discussed, Ethernet-APL makes more sense for certain instrument types than others, so it will take a while before everything is available with Ethernet-APL.
And letās not forget about wireless sensors. Plants now use wireless sensors instead of portable testers for vibration, ultrasound leak tests, ultrasound thickness tests for corrosion inspection instead of temperature guns and so on. And plants put in wireless sensors instead of mechanical pressure and temperature gauges, sight level glasses and variable area flowmeters. These wireless sensors use WirelessHART. So clearly it becomes a lot easier to manage this mix of instrumentation if Ethernet-APL devices use HART-IP, too.
Because HART-IP, 4-20 mA/HART, and WirelessHART are all HART, they all work, look and feel the same way. Instrument engineers and technicians can use the same tools and work processes. It just makes their jobs so much easier. Lots of functionality and terminology is common. And, āoh, by the way,ā you can run HART-IP all the way to the cloud. We already run HART-IP from wireless gateways in the plant to analytics in the cloud without converting to intermediate protocols. Faster sampling time means faster control loops which means better control. Faster response time also means approved Ethernet-APL devices can be used for functional safety.
With digital, we can avoid covert failures associated with analog signals. So high speed enables safety instrumented functions, fire and gas, and machinery protection systems that are hardwired to go digital. That is, all plant systems can go Ethernet-APL. It also means many devices will have embedded web servers, so you can configure, diagnose and manage them from a web browser.
And with increased device memory, the FDI package, that is, the device description file, can be stored onboard the device and automatically uploaded into your system, so you donāt have to search the web for the exact right file. Similarly, instruction manuals and other documents can be stored in the device and uploaded, so you donāt have to surf the Internet to find the right document for your particular device.
Q: I think it's also clear that all those 4-20 mA HART devices aren't going away any time soon. I mean, if you look at the rate of new plant construction, certainly in the U.S., there aren't a lot of new plants going up. 4-20 mA HART is going to be around for a matter of decades. Add, in ongoing WirelessHART installations, and some commonality across a mixed environment is certainly a selling point for using HART-IP.
A: Users already must upgrade their DCS every few years, and with it their device management software. So, in the near term, they should make sure to support HART-IP in their next round of updates.
HART IP isn't just for Ethernet-APL devicesāit's also used in HART multiplexers and WirelessHART gateways, too. So don't wait until that next new plant to upgrade to HART-IP. In fact, you may already have trusted some of your instrument communications to HART-IP, but just don't realize it. If you have WirelessHART, HART-IP is there, tooāworking away in the background, but ready to do more.
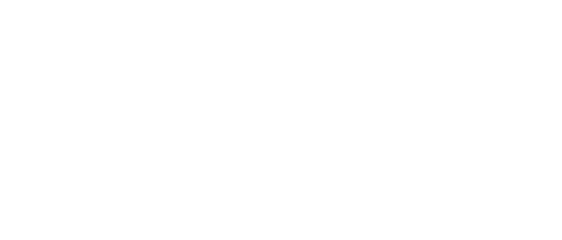
Leaders relevant to this article: