The introduction of Ethernet-APL technology earlier this year is an important technology milestone, enabling a new, high-performance paradigm of digital field communications for the process industry. Its dramatically higher bandwidth and delivered power promise to enable a new generation of far more capable field devices in hazardous and highly distributed locations. And, because it’s based on Ethernet, it promises to unify and dramatically simplify the control and information architecture of tomorrow.
But from a practical perspective, tens of millions of analog 4-20mA instruments are installed around the world—and their numbers continue to grow daily. No one will be tearing them out anytime soon. Further, these analog devices are joined by a growing number of wireless monitoring instruments that are helping to realize the Industrial IoT ambitions of process manufacturers worldwide. So, you may be wondering, how can all these devices coexist and work together tomorrow and for decades yet to come?
The answer lies in the HART protocol, which effectively transcends the physical layer differences among analog 4-20mA wiring, wireless mesh networks and Ethernet. Importantly, HART also preserves the ubiquitous, well-established knowledge base of industry professionals when it comes to field instrument implementation and support.
Chief Technology Officer, Automation Solutions, Emerson
To learn more about how these important differentiators among Ethernet-APL capable networks creates a unified experience for users, Control caught up with Peter Zornio, chief technology officer for Emerson’s Automation Solutions business.
Q: Peter, to start things out can you tell us a bit about the original 4-20mA HART protocol, how it came to be, and how it’s continued to stay relevant now for more than three decades and counting?
A: In the mid to late '80s, as intelligent field devices with microprocessors were first coming out in the industry, every system vendor also had their own digital protocol to communicate with those intelligent devices, often in a relatively closed manner. Each vendor used their own protocols to communicate with their own devices, licensing them to a select few partner suppliers of field devices. Industry and the customer base, however, were looking for an open protocol that could be used interchangeably across multiple vendors.
So, Rosemont, a part of Emerson, pioneered the HART protocol as an open digital protocol for communication with control systems largely because, at the time, they were much stronger in field devices than in systems and wanted a uniform digital connection to all systems. And one of the very smart things they did from a technical point of view was to add the HART protocol as a digital signal superimposed over the existing—and very ubiquitous—4-20mA analog communications signal for process measurement and control.
This meant that all the systems currently in place still worked, but with this extra digital information. That preservation of current technologies really helped HART to be rapidly adopted among independent instrument vendors and end users who were looking for a digital protocol not tied to one system vendor. Simultaneously, industry started an effort to develop an official standard for a digital-only protocol, which became known as the Foundation Fieldbus protocol. But by the time that standard was ready to go, HART was supported by most device vendors and up and running across the broad installed base of control systems. Further, the ease of adoption that it brought by not disturbing existing work processes had let HART build up a big head of steam.
Then, in the past 15 years or so, all the system vendors have come out with much more flexible I/O solutions that allow HART devices some of the same benefits of reduced wiring and more flexible installation that Foundation Fieldbus offers. That's also increased HART adoption, further cementing it as the de facto standard for process field devices. Finally, in 2008, the digital, wireless version of HART became an IEC standard and has achieved good usage. It’s considerably different from the 4-20mA standard because it’s all digital. Obviously, there’s no 4-20mA signal over the airways.
Q: Was the continuity of work processes that HART offered part of what caused Foundation Fieldbus and other fieldbus alternatives to underachieve?
A: I think if we look back, everyone liked the idea of a digital network-based field communication protocol. They liked the idea of multi-dropping instruments on fieldbus segments and the potential wiring savings that Foundation Fieldbus offered. But what they found in practice was that it required significant retraining of the workforce. It took additional engineering hours during system design, plus more highly trained technicians—in control systems, not just instrumentation—during installation and troubleshooting.
In short, Foundation Fieldbus technology works, and works very well. Emerson was one of its big supporters when it first came out. We’re still very proud of the state-of-the-art—we think best-in-class—solutions we have for Foundation Fieldbus. But customers who have not adopted Foundation Fieldbus tell me they are not adopting it because of the changes in work practices and the increased training and complexity it brings.
Q: Are there lessons to be learned from the underachievement of fieldbus that are applicable to Ethernet-APL adoption?
A: Absolutely. I’m a firm believer that we need to make sure we don’t repeat some of the missteps made with Foundation Fieldbus. And it really does come down to making sure that the introduction of the Ethernet-APL technology does not bring the same sort of dramatic step change in training, work practices and skillsets. If it does, it’s going to suffer the exact same adoption hurdle that Foundation Fieldbus did.
Q: Emerson’s a long-time leader in the realm of human-centered design (HCD) principles in the realm of automation and controls. Are there some UX principles that apply here?
A: The HCD principle we talk about is “the relative amount of gain for the relative amount of pain.” It’s a principle that can apply anywhere, but I think you can see it very clearly here. When HART was introduced, it was digital technology on top of an existing analog ecosystem. You could do everything you did before, it was just more. If Ethernet-APL introduces a lot of new pain for the promised performance gain, adoption will suffer.
Q: When WirelessHART was first introduced, now more than 10 years ago, HART-IP (for Internet Protocol) was created to backhaul data over Ethernet from WirelessHART access points. In a way, that work seems to have anticipated the development of Ethernet-APL. Can you describe some of the latest features of HART-IP that now make it suitable to go all the way down to the field?
A: At Emerson, we first realized the need for HART-IP to aggregate wireless HART or 4-20mA digital HART messages and send them along on a higher bandwidth Ethernet network. HART-IP was first standardized for this use by the FieldComm Group’s predecessor, the HART Communication Foundation. WirelessHART already had mandatory cybersecurity features to ensure its secure use in potential control applications. And as we now look at HART-IP being used more broadly; those same cybersecurity considerations have been applied to secure HART-IP for direct control over an IP field-level network like Ethernet-APL.
Q: Interoperability is another key attribute of the HART ecosystem that’s been hard won over the years. Will that interoperability goodness carry over into the next generation of secure HART-IP over Ethernet-APL devices and systems that we’ll soon see on the market?
A: Yes. And when you talk about not changing work practices, about easing the technology into a new customer site, that very capable and rich interoperability ecosystem that we've developed around HART is probably the biggest thing that secure HART-IP is bringing to the party. You will not find a more supported, more mature, more interoperable field protocol ecosystem than HART.
We have a very well defined ecosystem in which all vendors' devices get certified by the FieldComm Group. This ensures that they work with another vendor's host system, that they can be configured on that other vendor's host system simply by providing a file. In the beginning, it was a Device Description (DD) file, then an Electronic DD Language (EDDL) file, and now what we call a Field Device Integration (FDI) package. The FDI package supports a very rich configuration environment that combines the benefits of EDDL with all that the FDT Group’s Device Type Manager (DTM) templates have to offer.
End users have come to expect that a HART device will “just work” on their control system, and that they're not forced to use specific configuration tools from specific vendors to make those devices work. They can simply pick any vendor configuration package and expect that a HART device will be configurable and integrated into the control environment.
Further, all the major control systems provide very rich integration with secondary HART data right off the back of that automatic configuration that you get from the tool. So, the ease of configuration of any third-party device, the ease of integrating that data into the control environment, those are all things that users know work well. And with secure HART-IP over Ethernet-APL, they can expect the same experience from the same tools; just faster!
Q: It seems that the new HART-IP over Ethernet-APL devices will, for purposes of device management and configuration, act a lot like 4-20mA or WirelessHART devices. How would you describe the continuity of experience that users will have when switching back and forth between analog, wireless and Ethernet-APL devices?
A: Let me just say, I believe Ethernet-APL is largely going to be a greenfield technology. We're not going to see customers going in and upgrading existing Foundation Fieldbus, 4-20mA or any other protocol devices unless they really have a specific application that's driving the need for the increased data rates that they'll be able to get with Ethernet-APL. But even in greenfield there will be a mixed environment for a long time. The experience they should be able to get will be the same tool, the same look and feel whether it’s a 4-20mA device, a WirelessHART device, or a secure HART-IP over Ethernet-APL device.
Q: That certainly seems a more straightforward path than trying to introduce another new protocol. HART has been with us for a long time, but is it reasonable to expect that it'll serve all the communication needs of all types of devices going into the future?
A: While we typically use the relatively slow 4-20mA HART for simpler devices with perhaps 50-100 pieces of data to communicate, such as temperature or pressure transmitters, we’ve done some very complex devices with WirelessHART. For example, a vibration transmitter where we're able to communicate an entire wireless spectrum over the digital signal. So, we believe there really isn't a device that secure HART-IP won’t be able to handle, as far as the fundamental commands and the structure of the way the data is communicated. And, of course, with Ethernet-APL, you’re going to have 10-Mbps of bandwidth to work with, moving large amounts of data quickly.
Now, when you go into the world of electrical equipment, there are other protocols that have been used over Ethernet for a long time, such as EtherNet/IP, PROFINET, and many others. I would propose that we probably could use secure HART-IP for these devices, but I think that because customers are already using those protocols and have workforces that are trained in them, they are going to want to continue with them, just as HART users will be comfortable with HART-IP. There might also be cameras, more complex sound sensors or devices that we don't even think of now that might bring along their own Ethernet-based protocols.
Q: And there's nothing stopping you from having a shared infrastructure with multiple protocols on it, which is kind of a mindset switch when you're moving to more of an Ethernet type of infrastructure, isn't it?
A: That’s correct in principle, but I think what we're going to see is some segmentation among networks used for different purposes so that, for example, a network segment used for control has sufficient bandwidth reliability. But then think about bringing these dedicated segments together at the trunk level.
Q: You mentioned FDI is really a key component in this interoperability equation for HART. How does that play as we move into this Ethernet-APL world? Does FDI continue to play the same sort of role that we see today?
A: Yes, FDI is a key component of making sure that as device manufacturers build devices with lots of new features, capabilities, and parameters, that the host systems that connect to those devices can auto-discover those features and technologies, just like they do today for HART and Foundation Fieldbus. FDI also provides the ability for the device vendor to provide user interfaces in the form of, for instance, web pages that allow the end user to see the device in the way the device manufacturer intended it to be seen and to be configured. So, FDI allows device manufacturers the freedom to add capabilities and features that are then auto-discovered by the systems on which they're hosted and become integrated into those host systems—automatically and across multiple vendors!
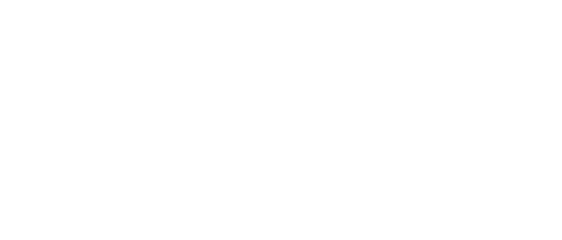
Leaders relevant to this article: