Functionality always comes first. But when faced with alternate solutions that can do the job, total cost of ownership (TCO) is always the rational decision-maker’s first tiebreaker. That maxim is perhaps never more true than when it comes to the DIN-rail mounted power supplies that are so essential to the process industry’s production operations. Indeed, lower cost devices typically penalize their owners in more ways than one: through lower efficiency and higher energy costs, as well as higher cabinet temperatures that shorten the lifetime of the power supply itself and all the other electronic componentry contained in the cabinet.
The TCO calculation for a superior design that results in lower energy usage is typically sufficient from an economic justification perspective. But add in the potential cost of unnecessary shutdowns due to premature equipment failure and the decision isn’t even close. To gain a better appreciation of the considerations at stake when it comes to power supply efficiency, Control caught up with Ed Merkle, engineering manager at PULS L.P., the suburban Chicago-based U.S. arm of Munich-based PULS GmbH.
Q: TCO measures are typically applied to capital equipment purchases. How does PULS apply the same concept to a simple power supply?
Engineering Manager, PULS L.P.
A: At PULS, we believe that the power supply unit (PSU) is the heart of any control system. If the power supply fails, so does the capital equipment, causing delays and loss of production, expensive man-hours to replace failed power supplies, and in some cases, expensive losses due to travel to remote locations, or even loss of in-process recipes such as pharmaceutical batches.
Q: Why is efficiency so important and why should users and machine builders place a premium on highly efficient power supplies?
A: Efficiency has always been the main design criteria at PULS. Everything revolves around efficiency because it not only reduces energy usage, but also has such a huge impact on the lifetime of the power supply itself as well as other electrical components inside of a control enclosure, including controllers, touch screens, I/O modules and communication devices. All power supplies require electrolytic capacitors, not only on the AC input side, but also on the DC output side. The electrolytes in these capacitors are extremely susceptible to heat and can dry out over time. Sooner, if temperatures are extremely hot. Selection and location of the capacitors inside of electronic devices, including power supplies, is extremely important.
A key power supply metric is its “lifetime,” a performance data point rarely provided by most manufacturers. Essentially, it's the elapsed time until failure for a power supply with capacitors fully loaded at a temperature of 40° C. If there are six different types of capacitors in a power supply, the one with the lowest lifetime figure becomes the weakest link. That figure becomes the expected lifetime of the power supply. That’s why it’s important to ask the manufacturer of your power supplies to provide you with lifetime information, not just mean time between failure (MTBF). If we can cut the surrounding temperature inside of the enclosure by 10° C, the power supply will last twice as long. Conversely, a poorly designed power supply with low efficiency will create more heat, decreasing the lifetime of the power supply and other devices.
MTBF is the probability of device failure and represents only a statistical representation of the likelihood of a device to fail. Lifetime, however, considers typical operating conditions of temperature and time, so it's a much more accurate representation of failure rates and maintenance requirements.
Q: What other power supply features can result in more efficient, lower temperature operation?
A: Power factor (PF) is the ratio of true power to apparent power of a device. A purely resistive load has a PF of 1 or 100%. A power supply, however, is considered a reactive load with the current and voltage waveforms out of phase from each other. This can result in a power factor significantly lower than 1, and in conjunction with efficiency, translates to a higher operating current. Active power factor correction helps align the voltage and current waveforms and can improve a power supply’s PF to greater than 99%, substantially reducing energy usage and excess heat inside the enclosure.
A power supply designed to deliver a higher short-term output current can allow a motor or other high inrush DC loads to start without needing to oversize the power supply.
Without this current reserve, the power supply may need to be rated higher than the continuous current than would otherwise be required. It would also be a physically larger power supply, taking up more space in the enclosure, and possibly forcing a larger, more expensive enclosure.
On the other hand, a power supply that produces a very low AC inrush current when it's energized can allow more power supplies to be operated from a single circuit breaker, reducing the number of overall components in an enclosure and possibly resulting in a smaller control cabinet. Lower AC inrush can also help reduce voltage dips on the AC mains if several supplies are turned on at the same time—especially if other AC equipment is being energized at the same time as the power supplies. This also prevents nuisance trips that can cause unnecessary downtime and troubleshooting efforts.
Taken together, active power factor correction, higher short-term output current and low inrush current can significantly reduce the overall size and rating of the necessary power supply and help reduce mains disturbances.
Q: Can you give an example of how efficiency and active power factor correction affect overall energy usage during continuous operation?
A: Efficient design and active power factor correction can dramatically impact energy usage. The equation governing that relationship is:
AC Current = Output Power / (AC Voltage * Efficiency * Power Factor)
The efficiency of a no-frills power supply might be 85% with a power factor of 0.66. So, for a 240W load, the necessary current would be:
3.57A = 240W / (120VAC * 0.85 * 0.66)
A high efficiency design (93.6%) with active power factor correction (to 0.99%) would draw only 2.15A—much closer to the ideal resistive demand of 2A and a full 66% less energy than the basic option:
2.15A = 240W / (120VAC * 0.936 * 0.99)
At PULS, we use not only an efficient design, but other features to result in the the smallest, most efficient, highly reliable and lowest-application-cost power supplies. Each of these features build on the others, resulting in unparalleled TCO across industries.
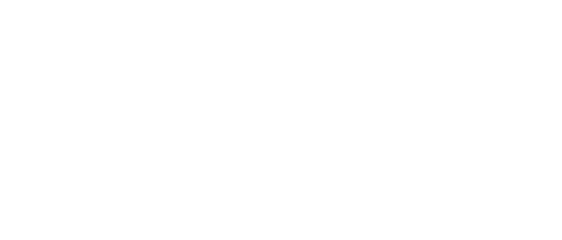
Leaders relevant to this article: