Peter Coleman, president and CEO of Buffalo Niagara Manufacturing Alliance, joins Amanda Del Buono to discuss how the coronavirus pandemic is challenging the manufacturing industry and its workforce.
Transcript
Amanda: Welcome back to Manufacturing Tomorrow's Workforce. As always, I'm Amanda Del Buono. For today's episode, we're taking a break from our traditional content to take a moment to discuss how manufacturers are coping with the coronavirus pandemic here in the United States.
As we all know by now, manufacturers are being called on to help supply medical equipment that is desperately needed and for others to maintain their normal essential operations to keep society up and running, whether that be oil and gas or food and beverage. No matter which bucket a manufacturer falls in, there's no doubt that they're facing workforce challenges in keeping up with their existing or new demands.
As this pandemic challenges manufacturing workforces, we want to be sure that we are here to provide some guidance along the way. As such, today is the first special edition podcast covering the impacts of COVID-19 on manufacturing workforces. Going forward, we'll be publishing special editions as available around our normal publishing schedule. So, if you haven't yet, subscribe to Manufacturing Tomorrow's Workforce in your favorite podcasting app so you can keep up on all of these podcasts as they publish.
On to today's episode. To discuss the impact of coronavirus on manufacturers more in-depth, Peter Coleman, president and CEO of Buffalo Niagara Manufacturing Alliance, is joining me today.
Hi, Peter, thanks for calling in to talk about this.
Peter: Thank you for having me.
Amanda: So, to get started, can you just give us a general snapshot of how COVID is impacting manufacturing? Obviously, this could differ by vertical or by geographical location in the country but, what are you hearing from those that you work with?
Peter: Well, within three weeks, we've had a complete transformation of our industry that started out with, obviously, some COVID cases being identified in New York City and other areas and the regulations coming down from the state government and executive orders, which seem to change on a daily basis. The first step was to get non-essential personnel out of the front office and working from home. So, that's the new normal. The second one was addressing workplace safety issues on the production floor and making sure that we are providing proper safety operation procedures and standard operating procedures for manufacturing industry to make sure people felt safe.
Then there was the call to stop all non-essential manufacturing, which shuttered some of our facilities but then, further guidance came out on what is essential versus non-essential. Right now, we're seeing over 50% of our manufacturers operating at full capacity. Now, that's in Western New York. There's 1,500 manufacturers in Erie and Niagara County, and they're serving essential markets be it energy, medical devices, and other essential, food production, entities. So, they're operating. The best part about our environment is it's inherently social distant, usually on a production floor. We average about 400 to 500 square feet per employee in the production state. So the question is how do you operate in those low-risk areas and then address safety concerns on areas of congregation such as break rooms, restrooms, and maybe like your shipping and receiving departments where you would have interaction with the outside world.
Amanda: Okay. You know, we've seen that, kind of you just pointed out, the impact that the pandemic has had on unemployment rates and then, obviously, many people are working from home and there are some facilities trying to run leaner. In general, how are you noticing the manufacturers in your area maintaining their staff? You said that they're running at full capacity but are they still keeping people in the facility? Are people showing up? Have they had problems with anybody coming into work, things like that?
Peter: Well, again, what I would identify as engineering, accounting, project management, those functions are occurring. Again, I would call those front office staff is head home and working from home. Have there been reductions and furloughs and layoffs? Yes. We're very encouraged by the new CARE Act that came out with the payroll protection plan that's coming in. So that gives us eight weeks of payroll subsidy that's in the form of a loan that will be forgiven if we maintain and keep our work staff above 80%. So, there are some significant policies being enacted at a federal and state level to really protect our industry, so we're encouraged by that.
Other areas, just how do we address concerns in the workplace and, if you have at-risk populations inside on the floor they oftentimes will self-declare and say, "I can't work because I am at risk," or they may be caring for somebody, or an older family member may be at risk. And then the last part is, obviously, the schools being shuttered and closed, how do you take care of your children? So, I think everybody is working on plans and policies to adapt to this environment. It's been difficult. Again, it's easier for a larger, more mature company possibly with significant human resource capabilities to handle. It's really difficult on the small-medium enterprise, that family-owned business.
So, understand what manufacturing looks like. 90% of our manufacturers in this area are fewer than 50 employees and usually, family-owned or closely-held businesses. And they may not have a robust HR department and they're still functioning. Then how do they learn to navigate this new regulatory environment, this new operating environment in the best way? So, there's a lot of questions there. Everybody's trying to do the right things and making sure they're operating with an abundance of safety in mind.
Amanda: Yeah. And I was curious, what, if any, guidance the Manufacturing Alliance is offering to your local manufacturers? Are you offering any kind of safety tips on ways to keep their employees safe or any other kind of support?
Peter: We are. So, we formed a task force made up of primarily what I call subject matter experts and the focus of the task force is risk mitigation and business continuity. So one, how do you mitigate risk in your facility? Kind of developed a heat map of functions that would occur in most manufacturing centers with regards to process mapping, what occurs in the map. And then in that, we then define what are your risk profiles? And in those risk profiles, what steps should you be taking with regards to increasing social distancing, reducing outside influence on your facility? And then what are the cleaning measures that should take place? Not only with the individuals but with material that comes in and then material that transfers or goes from workstation to workstation, how do you do that?
The other thing that we're working on is when you have multiple shifts, which we've done, right? So, in order to increase the social distancing, many companies have gone from one to two shifts, so then how do you clean between those shifts, those work areas? Usually, we stagger the shifts by an hour. We have our cleaning crews come in and clean the workstations and gives us about an hour turnover. Then that person in place, part of their cleanup is, hey, sanitize your workstation so when the next person comes in, they're protected and then you're protected in the morning when you come back to your shift.
Amanda: It sounds like it requires kind of calling on people to look out for your co-workers too?
Peter: We're all in this together. I think people understand, the economy's going to have to function again. The question is, how do we do it in a safe manner and then how do we start to ramp up? We've been really focused on fattening the curve, right. When we come out of this, how do we...what are the best practices that should be utilized and integrated with significant input from the CDC and OSHA on how you should operate in this new environment?
Amanda: Yeah. Well, we're gonna get out of this at some point like you mentioned. Obviously, the future is very unpredictable right now but how do you think manufacturers are going to pull out of this? My colleague recently had done some reporting on the topic in the process industries and a lot of them are investing in digitalization now, kind of bumping up those efforts and maybe planning for those so that if something like this were to occur again, they are ready to run their operations remotely or what have you. Are you seeing that kind of thing in your area? Do you see manufacturers kind of looking at the future and how can we avoid this or, you know, what are you seeing on the horizon?
Peter: I think this will be a game-changer. I think people are understanding, hey, I can work from home, I can perform a task. There may be benefits to this, social distancing aspect. I think, really, we are a process-driven industry and these processes are being developed. The question is, how do you measure the impacts? How do you measure success and ensure that this is continuity of your company and of manufacturing in general? Those people in the front office are oftentimes serving a customer who is really the production worker, that skilled worker that needs to be fed and given good, accurate information. So how do we make sure, in this environment, we maintain our quality, you know, the quality of the product that we're delivering? That's a concern.
Amanda: Well, are there any other points that maybe I didn't touch on or areas that you wanted to reinforce to manufacturers who are maybe looking for some guidance?
Peter: I would say, getting as much information into their hands as possible in a clean and orderly way is important. We're trying to do that for our members. We're being very proactive in reaching out to them to see what they need and understand what they need. You know, again, serving this industry and making sure that they're operating and operating in a safe manner is incredibly important.
One of the other ones is what happens if we do have a positive COVID-19 case, right? So, education of our workforce before an incident occurs is critical. So, what would we do if we had a positive case? And the simple is... obviously, we send everybody home. We identify individuals that were in close contact with that person, they're asked to stay home for three days. If they don't present any symptoms, then they're allowed to come back to work. And really, this is all with guidance that we're getting from OSHA and the CDC. So, educating everybody on how to function and identifying the processes and procedures that need to take place to, again, operate during the pandemic in a safe and orderly way.
Amanda: Are there any resources that the Manufacturing Alliance has available or anywhere that you suggest that people go to, to acquire information on running their facilities during this time?
Peter: We have, on our own website, a COVID-19 response page that our task force then puts up. And those areas that we focus on are going to be, again, risk mitigation, proper OSHA and CDC operating guidelines. We then get into the financial side of the business, which is how do you ensure liquidity? What do you do with furloughed, laid off or terminated employees? How do you handle and engage in this new marketplace and subsidies and programs that are being delivered and offered by the federal and state government? So really, that's kind of our service.
Amanda: And that's available to anybody?
Peter: It is. Our pages are public. We have links to the subject matter experts from accounting to finance, to insurance, to safety, things that you should be doing and how to operate. And most businesses are making that open not to just their clients, but to the public.
Amanda: Well, I mean I'm glad to hear that there are still manufacturers out there plugging along and keeping a little bit of hope and just trying to keep the world going, right? So, thank you so much for joining me today and, you know, sharing these suggestions and resources with our listeners. We really appreciate that and I'm sure that it will be very helpful to many of them.
Peter: Well, I appreciate the time and thank you for getting the word out about all the great things happening in the manufacturing sector even during these difficult times.
Amanda: Yes, yes, and thanks to our listeners for tuning in today. And please, everybody, stay safe out there.
For more, tune into the Manufacturing Tomorrow’s Workforce podcast.
Latest from Podcasts
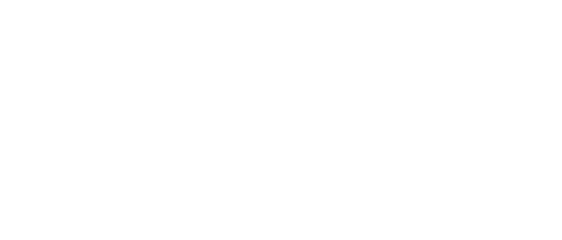
Leaders relevant to this article: