In this podcast, Sam Hoff, CEO of Patti Engineering, a CSIA-certified system integrator in Auburn Hills, Mich., talks with Jim Montague, Control’s executive editor, about the Industrial Internet of Things, workforce development and other topics.
Transcript
Hi, this is Jim Montague, executive editor of Control magazine and ControlGlobal.com, and this is the latest in our Control Amplified podcast series. In these recordings, we talk with expert sources about process control and automation topics, and try to get beyond our print and online coverage to explore some of the underlying issues impacting users, system integrators, suppliers and other people and organizations in these industries.
For our eighth podcast, we're talking to Sam Hoff, CEO of Patti Engineering, a CSIA-certified system integrator in Auburn Hills, Michigan. Sam has given us the system integrator's perspective, experience advice, and in connection with a bunch of process control and automation topics in recent years, including cybersecurity a couple of years ago, and most recently with the workforce development cover article in the September issue of Control magazine. These days, many of what used to be separate topics are now coalescing around digitalization and the Industrial Internet of Thing, so we're going to talk about that, though more than likely, we'll lapse into some of the others. Well, Sam, sorry for the usual preamble, and thanks for joining us today.
OK, let’s get started.
Sam Hoff: Hey, no problem, Jim. I’m happy to be here and would just like to add, I do sit in Auburn Hills, Michigan, but we also have offices in Indianapolis, Indiana, and Austin, Texas.
JM: First off, how do you and your colleagues, but in Michigan and your other offices, how are you guys seeing IIoT and digitalization unfolding lately? What are its latest big milestones?
SH: So, the whole IIoT, industry 4.0, digitalization, I think it’s been a lot of talk and a lot of theoretical over the last 10 years basically. I think just in the last year or two or so, you’re seeing where it’s going from theoretical to practical, and you’re seeing real-world applications of digitalization and seeing the benefits and seeing proof of value and people really starting to say: What can I do with IIoT? What can I do with digitalization? How can this affect my throughput and my quality? It’s gone from the board room to the plant floor at this point.
JM: Are there characteristics, things that are common to IIoT applications, any typical equipment they use?
SH: The whole plan with IIoT is you really need to decide up front what you’re going to collect, what data you’re going to collect, where you’re going to store the data, and how, in particular, you’re going to analyze the data. A lot of the benefits of IIoT are the analytics of the data coming off the plant floor. It’s interesting, you go into a lot of these facilities and they’re very data-rich, but they don’t do a whole lot with the data because quite honestly, the people that are running the facility don’t have time to take a look at all the data and see what it’s telling them.
JM: So, given that being the case, how is digitalization and IIoT impacting system integrators like yourself, and then what types technologies, applications and projects are affected by that?
SH: So, I think it’s as integrators we’re figuring out ways to get closer to the end-users and being able to use the data and information coming off their plant floors to help give them the analytics to help them perform better and the digitalization to perform better. I can tell you that these systems get more and more complicated all the time and to ask somebody in the manufacturing floor to maintain and be an expert on all these disparate systems is really asking a lot of somebody.
JM: Are they any particular projects Patti Engineering has done that you can talk about where IIoT and digitalization were used, and if so, how were they carried out and was using IIoT an improvement over former ways of doing it?
SH: Sure, we have a couple different projects we’re doing right now. One is pulling analytics off of parallel CNC machines to measure OEE, to look at data, to see predictions on tool wear. A lot of time if you take a look at the tooling that’s sold with the CNC machine, maybe the manufacturer says it’s good for 20,000 hits, but, depending on how you use that tool, it could be good for 10,000 hits, it could be good for 50,000 hits. It’s kind of like the tires on your car, and the manufacturer says your tires are good for 30,000 miles. Well, depending on your driving habits, they could be good for 15,000 miles or they could be good for 50,000, and what you do with your tires is you look at them, and you see how they’re performing, and you replace them when the tread gets low. Well, it’s tough to really look at a tool and tell exactly when it’s getting dull, or when it needs to be replaced, but through analytics, we can kind of tell that.
JM: So the old way, I mean people used to gather tire information or OEE in the past, but I guess it was more cumbersome, the programming might have been more difficult, so digitalization and IIoT, as I understand it, is making some of these tasks easier, and I assume it’s easier for you guys, too, right?
SH: Yeah, and a lot has to be done as far as how you’re going to take the data, because of communication rates and all, you might have to have an edge device to do some pre-processing, and then take the data to the cloud or some data lake or something like that. But the design and how you’re going to lay out the data and planning upfront is very important to do.
JM: Is there any particular tools, data laking, or data gathering or analyzing methods that you guys have found to be preferable?
SH: There’s a lot of AI-type systems on the market. We’re a big Siemens partner with Siemens MindSphere, there’s a lot of analytics and AI tools that are actually built into the MindSphere platform, which is nice.
JM: Some sources report that users can deploy an IIoT box or gateway and go right to the cloud and to skip PLCs and DCSs entirely. So, some of those control systems might become obsolete in the future. Is there any truth to this idea, and if so, how much and why?
SH: Much like your phone is a gateway to the Internet, I don’t ever see some type of controls device at the machine level going away. You’re going to need to have the real world and the pretty much instant control of I/O happening at the machine level. Will the devices in the future become a little bit more dumb because some of the analytics and all can be done in the cloud? Yes, absolutely. But I see it kind of morphing over time, but I don’t see it going away.
JM: In covering IIoT and digitalization in some of the stories in Control magazine, we've noticed they tie together many formerly separate disciplines, such as cybersecurity to protect IIoT's networking. What are some former silos that digitalization and IIoT bring together, and how do they do it?
SH: It’s amazing. The siloes that have to break down within our company and even within our clients’. For instance, the old way of designing lines or designing manufacturing systems is a company like a large line builder like a canal, they’ll use a simulation tool to layout the mechanical design and how the parts going to processes, and design all the mechanics of the system. How big steel do we need? How big a load? How big a servo-drive? And then the controls engineer would make everything work.
Well now, that simulation is coming together and you can do a lot of that design in the simulation. And now, you can even use the simulation as the basis of your system, and as controls engineers are writing their code, they can test the code in the simulation, which in the whole virtual commissioning aspect of the simulation software is really exciting.
I’ll give you a little story, Jim. We had a project last year for one of our really good clients, and it took them six months to build up one week of stock to shut down and upgrade this line that we were going to do for them. We were the only company that could ensure them that they would only be down for a week. The other two competitors that were bidding against us said they’d need to shut down the system for four weeks. The reason that we were able to accomplish that one-week downtime and switchover was because we had tested every line of code through virtual commissioning and simulation before we ever hit the plant floor.
JM: This is kind of, it goes into the digital twin concept as well, which is another way of an operational simulation.
SH: Yes. And now, what do you do when the system’s running?
JM: Yeah, it isn’t just for designing and setting up. You use the simulation for operations, just as you guys used it to multitask as the project was being put together, right?
SH: Yes, sir.
JM: Wow, man. It’s a brave new world out there. And as we found out with the workforce story in September, there’s plenty of new skills that IIoT and digitalization are going to require. It seems like rookies, veterans and everyone in between will need training. If so, what do you think they need to learn?
SH: Yeah, and I was talking with another client, by doing the digitalization and doing the digital twin and the simulation and all, you don’t have the mechanical engineer designed something, and the controls engineer says, “you realize what you designed mechanically, I can’t control.” And now they’re communicating a lot earlier, so instead of building the system and having the controls engineer say “I can’t control this, we have to make some changes,” they make it before anything is ever built. The siloes between the IEs, the MEs, and the EEs are all breaking down because they have to communicate more often and earlier in the process.
JM: And that’s good, because you might not find out about a conflict like that until the acceptance test in previous years, so that’s really good, right?
SH: Yep.
JM: But is there any mental or psychological stress that goes along with that being joined at the hip sooner? Is there any down side to that? Or maybe it’s just beneficial, maybe it’s less stressful to work together sooner.
SH: Yeah, it’s a different way of working, and maybe you have to get a little bit more outside your comfort zone, and engineers have a tendency to be a little introverted, so there’s a little bit of uncomfortableness that way.
JM: They must get used to it with practice right.
SH: Right.
JM: So, one of the things that we’ve been a little concerned with is once IIoT and digitalization really get going, that just like things like Amazon Web Services are just going to eat everything, and if so, why’s it going to happen? Or if not, why not?
SH: Well, you know Amazon Web Services, they certainly have a great cloud-based storage system. Like I know the Siemens MindSphere, on the backend their partnered with AWS. So, I think AWS is certainly going to be a big player, and I think one of the things that you’re seeing is like Amazon and Google and Microsoft and all are getting closer to manufacturing. They’ve kind of discovered manufacturing and what they can do as far as the data and all. So, yeah, I think they’re going to be a force in the future without doubt.
JM: Right, but they won’t replace, like with the earlier question about is IIoT going to take over from controllers? There’s always the feeling that one’s going to win and one’s going to loose and somebody’s going to go take over and somebody’s going to go away. And it really is a lot of these things just go together, you know, like Amazon Web Services will have it’s place, and it may be a large piece of the pie, but then many of the existing ways of doing things, you can’t use the cloud everywhere you may need to be on the edge, so it’s not always one thing will replace the other, a lot of times they’ll just go along into the future and like TV was going to replace radio and movies, and they just all continued together. You think that’ll happen with that we’re looking at now.
SH: Yeah.
Well, Sam, that was some great input. Thanks for cluing us in today about some of these things.
This has been another Control Amplified podcast. I’m Jim Montague. Thanks for listening. Oh, and please remember that Control Amplified podcasts are available on most podcasting apps, such as the iTunes store and Google Play, and on Control magazine's YouTube channel podcasts. Plus, you can also listen at controlglobal.com, of course.
For more, tune in to Control Amplified: The Process Automation Podcast.
Latest from Asset Management
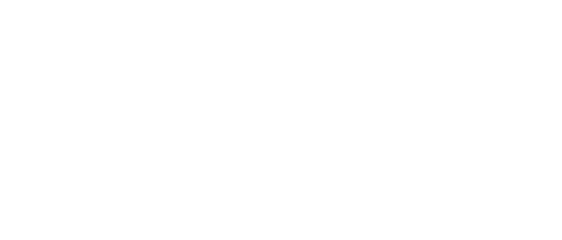
Leaders relevant to this article: