Augmented & virtual reality training in industry
In this podcast, Amanda Del Buono interviews Dirck Schou, CEO of Taqtile, about the use of augmented and virtual reality for training in the manufacturing industry.
Transcript
Amanda: Welcome back to another episode of Manufacturing Tomorrow's Workforce. I'm Amanda Del Buono. And today, we're taking a look at a technology that may be gaining more traction as the COVID-19 pandemic continues to define a new normal for the workplace. Keeping in mind that this interview was recorded prior to the COVID-19 pandemic hitting North America, I was joined by Dirck Schou, CEO of Taqtile, to discuss the benefits of augmented and virtual reality for training. Here's our discussion.
Today, I'm joined by Dirck Schou, CEO of Taqtile, a provider of workforce enablement software that works for XR Solutions. Thanks for joining us today, Dirck.
Dirck: Thanks, Amanda. Happy to be here.
Amanda: Awesome. Well, we've done a few podcasts last year on AR/VR training. So, I wanted to start out by asking you what you're seeing with manufacturers implementing the technology, is it still few and far between? Are more people using it? We talk about it so often, but how common is AR/VR really in the industry?
Dirck: Sure. Well, I think that there's been a number of reports done recently that at least the manufacturers that have been queried on this, which probably tend to be on the larger side, very close to all of them are looking at this technology. Now, there's a difference between looking at it and implementing it. The fact is that implementation involves large changes to the way that workers do their job oftentimes. So, rolling out of this technology can take many months or, even up to a year or even longer to fully implement it. But without question, we are seeing a large number of manufacturers starting to look at this technology. And as more of those folks start to look at it, we start to see production use cases come out of the back end, and those are accelerating.
Amanda: All right. So, then for those who aren't buying in yet, whether it is for economic reasons or implementation issues, why should they be considering the technology? What are the ROI benefits of it that may overcome these hesitancies that people are having?
Dirck: Yeah. I mean, there are a number of drivers of this technology. The first of those drivers really has to do with the graying of the workforce, right? We have a very highly skilled set of workers who are wanting to wind down their careers and you don't have nearly enough younger people coming into this space. The whole mantra of, go to college, earn a better living, that sort of a sales pitch has been successful, although as many folks are seeing, is not all it's stacked up to be. But the fact is that we know that there are, over the next 5 years and 10 years, the aging workforce population of experts are going to be retiring and just not enough new people are coming in. The manufacturers are being forced to look for ways to very quickly ramp up the operational capability of the new workers. So, companies are thinking about training differently. They're also needing to enable different types of workers in different systems. Modern manufacturers have never been more connected. There's this whole category referred to as IoT or the Internet of Things that basically is sensors that allows plant managers to understand better what's going on in the plant and giving frontline workers access to that information in many cases in a hands-free mode, it's very important. And it's also very enabling for the workers.
The way that I look at modern AR/VR technology is, really, as the knowledge worker has been doing for the last 30 years. Their jobs have changed and have been made easier and different because of digital transformative tools. Let's just start with Microsoft Office and Outlook, right? Knowledge workers now, they sit at their desks and their job is on the computer. It's no longer pen and paper and that sort of thing. And that has become the digital transformation for the modern knowledge worker, but the frontline worker in a manufacturer, they have not had the benefit of these transformative tools, but because they have to use their hands in their job, right? So, if you can't hold something, if you're not sitting at a desk while you're doing your job, there has been no tools for you until when it's sort of the modern augmented reality headset for that matter. And that sort of digital transformation, that tool is going to change the job and the capability of the frontline worker in ways that we can't even imagine over the next 10 years.
Amanda: Right. Wow. So, you kind of mentioned the ROI, and I know you're more on the software side of things, but what does investment to implement these technologies look like from both the software and hardware side? I presume they go hand in hand, you're going to need both, right? So, what kind of goes into that? What should a manufacturer expect when they are looking to invest in the technology?
Dirck: Sure. Well, as we know, this technology is early, so the costs are going to come down over time. And basically, this ROI is always going to be a factor of increased safety, increased productivity, reduced time to do jobs, that sort of thing. But you need to look at this from sort of a larger perspective as far as what happens if you don't implement this technology, right? This technology, as you mentioned, we're a software company and we're not here to pitch our software. But if we look at examples of our customers who have implemented our technology, they have seen total elimination of errors on the job. So, you have to look at what is that worth to a worker who is in the middle of a manufacturing line or in a manufacturing environment in which they are working on multi-million-dollar pieces of equipment, right, or hazardous equipment. What is the cost to the enterprise for failing to deploy expertise where it is needed? Now, the other side of that, one of the other arguments there has to do with how much time-saving a worker has. We've seen, for example, tasks that would take two and a half hours for a worker to do drop to a half an hour, let's say, for a maintenance job on a manufacturing line, that sort of thing. This is going to be a very personal thing for every manufacturer to look at. I mean, an airplane manufacturer is going to have a different set of ROI metrics that they're looking at than someone who manufactures furniture or some other smaller consumable device. But the real issue here is that the modern worker going forward will have this tool ready for them. And those companies that do not adopt this technology are going to put themselves at a disadvantage.
Amanda: Right. That's interesting. And we've talked with a lot of people about the other issues was bringing in new people, especially with the skills gap. And as you're seeing, baby boomers retiring, it was interesting because I was talking to someone recently who was like, there's a lot of other costs that come to not properly training that we don't always think about, safety, repetition, and having things come out at quality. And those things could be a cost to you that you're not realizing because you're not properly training, and it's just a lack of experience. It's not incompetent workers necessarily, it's how do we get them trained quickly when we get them in the door?
Dirck: Sure. And there's two other elements to this. One, you hit on as you were sort of introducing the piece, and that is how do you attract workers, right? If you're a company, let's say you're company here in Seattle, and you're at a recruiting fair, and you're a manufacturer, and you're trying to recruit people when Microsoft's on one side, and Amazon's on the other, and Starbucks is on the other, how do you show that employee, that potential employee that you are going to invest in them and give them the tools to be better? And if you can say, "Listen, we are a modern manufacturer and we are using the best tools that we can going forward and you're going to learn how to use these tools," that's going to be compelling. The other thing that I'll say on that is that on the second half of this, we have to look at...we've done training in the same way from the beginning of time, right? It's watch someone do something, or have someone teach you how to do something and repeat that over and over again.
While with very well done, augmented reality, let's call them step processes, so any sort of a process that you follow a set of steps in order to accomplish something, if you have a set of well-authored step processes that have been authored by an expert, and anyone can access those at any time, well, as long as that worker has a general level of familiarity with the type of job that they're doing and the environment that they're working in, perhaps they actually don't need to be trained to do that job. Perhaps using an overlay, a digital overlay, which is what modern augmented reality headsets enable you to do, they enable you to look at a piece of equipment or a facility and have markers call attention to various buttons, or knobs, or processes that you need to do. If someone can follow along, that knows how to use this platform, that can follow along with a well-authored set of instructions, then maybe that person doesn't have to be trained. Maybe the skill moves from the understanding of how to do this one process into the understanding how to use this platform that allows you to do 100 different processes as if you were an expert. These are some of the areas that really start to make this technology very compelling.
Amanda: Right. So, you're kind of saving money too then with that as you're not paying somebody to spend their time training somebody else either.
Dirck: Absolutely. And the military refers to this as a force multiplier. So, if you ever watch a military mechanic working on a plane or working on a tank or whatever, there's one guy actually doing the work, and then another person holding the instruction boat saying, "Hey, look for the nut right next to this bolt or this joint or something like that, that's what you need to unscrew." So, if you don't have two people working on this job, if each person can do their job together, the military refers to this as a force multiplier. So, instead of monopolizing two people to do one job, each one of those people can do their own job, thereby you double in effect the capacity of your workforce.
Amanda: Right. Right. And I think that general training is something that a lot of companies are keeping in mind when they're hiring on new people. What's going to be the cost of bringing these new people in to replace the old people, new positions, things like that. Well, the next thing I was kind of curious about was, maybe there are some people who may argue that they have workers who maybe aren't so technologically inclined, and that training with like AR or VR or some other digital method may just not be practical for their workforce. What do you think would be the argument against that? How can this technology help less technologically inclined workers? Is it easy for them to pick up? What would be your argument for why those workers would still benefit from this?
Dirck: Sure. Well, the true test as to whether technology is doing a good job is when it starts to disappear. That's when technology no longer becomes something unto itself but a part of the whole, right? So, if you have a very complex technological solution that is intimidating to a worker who maybe doesn't spend their job sitting in front of a computer or who isn't a trained computer engineer or anything like that, that's going to be very intimidating to that person. The real key is to develop the solution such that it just becomes a part of the natural flow of the worker when they do their job. This actually amplifies when you are trying to deliver a means by which an expert, someone who's been doing their job for some time, so maybe that's a 50-year-old worker who's been on the job for 25 or 30 years, right? These people are not digital natives, right? They are not people who grew up with an iPhone in their hands. There are people who maybe have intentionally or unintentionally sort of shunned or avoided that technology. You have to make it very, very easy for them to use technology in a way that's not intimidating.
I think that in the end, if you're sitting in a scenario where you have a person who's, again, been on the job for, let's say, decades, maybe they're not wanting to sort of do the level of intense job that they've been doing before, or maybe they're the only ones that know how to fix this one piece of equipment, and whenever it breaks down on the weekend or in the middle of the night, they get called and they have to come in and do the job, and they don't want to do that anymore, right? They're beyond that. They're more involved in their children or their grandchildren or whatever, and they would like their personal life, right? To them, if you could show them a way to capture their knowledge such that other workers can come in and can sort of take advantage of that knowledge in the emergency situations or the environments where they may not want to work anymore, like lifting heavy weights or whatever that sort of environment might be, they're actually going to be very motivated. We've seen this with our customers that the older workers have, number one, the solution is easy enough for non-digital natives to understand how to use it. It has to be very simple to create step processes and capture knowledge. The older workers, the more experienced workers have been very open to the use of these tools. And in some cases, very enthusiastic about using these tools because they know it's going to let them sort of live their lives a little bit more intentionally.
Amanda: Right. Right. I'm curious, what are you seeing for AR/VR in the future going forward? Where is its place?
Dirck: Sure. So, you have a number of converging momentum, quite a bit of converging momentum going on in this space. Number one, the headsets, right? It starts with the headsets. If you're going to use AR/VR in a hands-free mode, you have to have a headset that's usable in an industrial environment. But the good news is that probably the biggest challenge of leapfrogging from the technological perspective, current environment in the industrial workplace is introducing new equipment. And the fact is that in every manufacturer, every worker is already walking around with a set of safety glasses on. So, they are familiar with the need to put on safety equipment when they go to their job. And that's in effect what this is. And if you look at the sort of supply chain driving the headset technology, let's start with Qualcomm, that is a major chip manufacturer in mobile devices, which is what a head magic computer in effect is, they've recently released a number of new updates to various chip sets to support specific implementations on augmented and virtual reality. The other part is if you're going to use AR/VR technology in a production environment, you need to have a solid network connection. And if you have been paying attention to what the carriers are doing, they are very focused on deploying 5G, and 5G is an interesting technology for consumers.
You can imagine, it gives you perhaps a greater level of connectivity when you're talking to someone on your cell phone, but for the enterprise, it really could potentially be a game-changer because 5G has capabilities that far exceed the capabilities of standard Wi-Fi. So, if you think about deploying basically a wireless network on steroids in manufacturing facilities, getting to places where you couldn't get to before with the network, and connecting to intelligent cloud solutions where you have your knowledge base stored, giving you access to expert knowledge and perhaps even connecting you to experts remotely, that can sort of help you through very challenging processes, this really is going to change everything. And I just guarantee you, I mean, the genie is out of the bottle on this technology. It has been for a while, but you are now seeing real-world production implementations of this technology. You're seeing accelerated development in the hardware available to deploy to frontline workers. In 5 years and in 10, the environment is going to be very different. And I'll say one more thing about this, this is not a replacement for your workerās solution. This is an enhancement to your workersā solutions. You can imagine robots have come in and they have dominated certain sectors of the manufacturing space, but where workers have to do multiple jobs, this sort of technology enhances their ability to do multiple jobs and further sort of forestalls the replacement of human workers by robots for some time if not perhaps indefinitely in many cases.
Amanda: Interesting. I kind of had a follow-up question. I'm curious to see if there are certain sectors of manufacturing that you're seeing maybe embracing the technology more, or that are setting a good example for AR/VR training in manufacturing. Do you have any of those off the top of your head? If not, that's okay.
Dirck: Yeah. I mean, the need to do very small, very specific work with your hands may not necessarily be the best use case for this technology just because the finite focus that is required from advanced optics and all that to really align specific steps or markers or augmented instructions to a millimeter or sub-millimeter sort of level of accuracy is not really realistic this point. So, you tend to look at...again, you're going to implement things in the sorts of environments where you're able to, at this point, so many of these things are indoors because if you have outdoor environments, you have to deal with the elements and sun and everything like that. So, you want indoors, which is good for most manufacturers, tend to be sort of larger pieces of equipment where someone may be operating something or maintaining a piece of equipment for that matter. If you're on a very repetitive manufacturing line, then people are going to do the job once and/or 10 times or whatever, and then eventually, they're going to do it, and they're not going to need any help. So, environments where you're asking people to do multiple things and perhaps areas where you have workers that are...I won't say transient, that's not exactly what I'm thinking, but where you have workers doing multiple jobs as a course of their day and perhaps they only touch this one piece of equipment once a year or very infrequently, then this sort of a tool can really make sure that they do things correctly, in the proper order, and in an efficient manner. So, those are some areas that we're seeing.
Amanda: Wonderful, wonderful. Were there any other points or anything else you wanted to add before we close out today's podcast?
Dirck: I mean, I'll just summarize that this is in the very near future going to become required technology. And this really is not an answer, it's a when question. And that's a phrase that's thrown around a lot, but this is absolutely the case with this technology, and the companies that embrace this and learn the lessons and the use cases that are optimal for them specifically using this technology are the ones that are going to put themselves at a competitive advantage going forward. And I think that people will find that it's easier and less expensive to deploy these sorts of solutions than they think. I mean, many solutions including our platform and others are production-grade solutions. These are not little test samples of, this is not the art of the possible, this is how you get this technology and production to make your enterprise safer, more resilient, and more productive. And I just encourage people to consider this as they think about their companies into the future.
Amanda: Wonderful. Well, thank you again so much for joining us today and sharing all this information with our listeners. It's been a popular topic from our previous episodes, and I think that they're going to take away a lot of new information from our discussion today.
Dirck: Thank you very much, Amanda.
Amanda: And that was my interview with Dirck Schou, CEO of Taqtile. Don't forget to like and subscribe to Manufacturing Tomorrow's Workforce on your favorite podcasting app, and stay safe out there.
For more, tune into the Manufacturing Tomorrow's Workforce podcast.
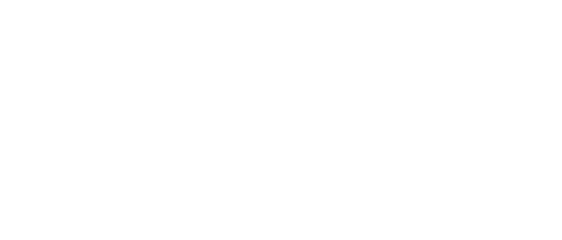
Leaders relevant to this article: