Manufacturing Tomorrow's Workforce: Breaking barriers to gender diversity in manufacturing
Sheri Plain, director of workforce services at Owensboro Community and Technical College (OCTC), and Amanda Saam, a new instructor at OCTC, discuss the program they’ve developed with manufacturers in their community, and how they’re working to remove the barriers to entrance for women in the field.
Transcript
Amanda Del Buono: Hi, welcome back to Manufacturing Tomorrow’s Workforce. I’m your host, Amanda Del Buono, and thanks for joining us today for another workforce conversation.
Before we get started, with only four days remaining until the nomination deadline, I’d like to remind you to recognize an innovative and influential woman from your organization by nominating her to be one of this year’s Influential Women in Manufacturing. The deadline is March 31, so don’t wait, nominate now!
Moving on to today’s discussion, partnerships between manufacturers and educators could be one of the keys to success for those organizations looking to fill their workforce vacancies with skilled workers, but there’s several other keys that can help to unlock workforce potential. One of them is gender diversity in manufacturing.
In this interview, Christine LaFave Grace speaks with Sheri Plain, director of workforce services at Owensboro Community and Technical College, and Amanda Saam, a new maintenance technician hire at Hitachi, to learn about the program they’ve developed with manufacturers in their community, and how they’re working to remove the barriers to entrance for women in the field.
Without any further adieu, here’s the interview.
Christine LaFave Grace: Owensboro, Kentucky, has a need: skilled manufacturing workers. And it needs them in a big way. Manufacturers in the region face dire shortages of skilled multi-craft technicians, placing these companies' production and growth targets at risk. Fortunately, they're also getting local help to address this need. Owensboro Community and Technical College, in partnership with local employers who are involved with the Greater Owensboro chapter of the Federation for Advanced Manufacturing Education, or GO FAME, offers an advanced manufacturing technician training program to help build the skills of individuals who are already working in industry but need more training to advance in their careers. Through the program, students work while attending school on an accelerated schedule and can complete a two-year associate of applied science degree in 20 months.
A little while back, program coordinators noted a huge area of opportunity: 44% of technical students at OCTC are women. But only 7% of them were involved in manufacturing programs. In addition, although women have a presence on the production floor at area manufacturing companies, they haven't been advancing into, for example, maintenance technician roles.
Sheri Plain wanted to do something about that. Sheri is director of workforce services at the college and is principal investigator on a new project, funded by a half-million-dollar grant from the National Science Foundation, that looks to better understand why women aren't participating in the advanced manufacturing technician training program in higher numbers and how to remove the barriers to their participation, so they can advance in their careers and local manufacturers can better address their critical workforce needs.
I'm talking today with Sheri as well as Amanda Saam, who a few years ago was a recent graduate of the Industrial Maintenance Technology program at Somerset Community College in Kentucky and a new maintenance technician hire at Hitachi. This summer, Amanda embarked on a new adventure: She signed on to teach at Owensboro Community and Technical College.
Sheri and Amanda, thanks so much for joining me today.
Sheri Plain: Thank you for having us.
Amanda Saam: Thank you.
CLG: Now, one of the key points of this program, the National Science Foundation grant-funded program is a focus group, reaching out to individuals within the community, to women who maybe contemplated participating in the program, or started but didn’t finish, to find out why aren’t they moving forward with it? What did you find from these focus groups, where are these women working, how did you identify them to participate, and what did you hear from them?
SP: Okay, I’m glad to start. This is Sheri, and I’m glad to start with that to let you know how we identified the potential participants. We actually opened it up to any of our manufacturing employers who were already participating in our GO FAME program. And the employers who actually had the largest amount of women already working in their facilities were the ones who were most interested, and we’ll continue this and still offer it to any company that would like to participate, but we had two companies that were very interested in being our first group, and that was Sun Windows and Unifers in Owensboro. It was purely voluntary in that all the women working in the production areas were invited to participate if they were interested. They knew that it was an opportunity to learn more about a training program, so those who had some interest in potentially pursuing that were the ones who actually participated.
CLG: Okay, that’s great. What did you hear? What were some of the overarching comments that you heard about the program and maybe what was stopping them from moving forward with it?
SP: Well, the most, probably the No. 1 thing we heard from the women, and we talked to 31 women in total, was that time was their biggest challenge. It was important to them to work full time, retain their full-time salaries, their full-time benefits. Many of the women were the single income-earners of their families, they were also, many of them, were the single care-taker of their family. So, working and retaining those full-time benefits is very important to them, and that was the biggest obstacle for them pursuing training in the past.
Some of the other things we heard were accessibility. They very much like the idea of training, but weren’t able to come of the college and sit through a program or the opportunities weren’t close enough. They really needed something that was available in between breaks at work or immediately after work or before work. So, accessibility was also a key issue.
CLG: Okay. That’s really interesting, too, the point you made about women being the single income-earners in their households. I know I’ve had a chance to speak with you before, you mentioned that men sometimes have the opportunities to take on extra work that women in that role haven’t been able to. Can you elaborate a little bit more there?
SP: Yes. Actually, in our GO FAME program as it’s designed, the participants will take classes two days a week, two full days a week, and then they work a minimum of three days a week at their sponsoring employer. And so, any work or time that they might miss being in class, they were more easily able to make up that time, to work overtime, or work on the weekends or to work over a shift, because they may not have that same family commitment or childcare commitment that some of our females did.
CLG: That’s such a critical point that can so easily get overlooked if we’re not asking, if you’re not asking about the barriers.
SP: Yes.
CLG: It sometimes seems that it’s so easy to take, sort of, the easy way out of, well, women just aren’t interested in these programs, or weren’t interested in applying, or they weren’t jobs that they were applying to, but when you dig a little deeper you find some really interesting results.
Amanda, how has this resonated with your own experience? Can you tell me a little bit about your story and background, and involvement with the program, and what appeals to you about coming back to become and instructor then?
AS: Sure. Basically, I found myself going through a divorce, and losing everything. I lost my car, I lost my house. The only thing that I really got to keep was my kidd-o, thank God, but I knew that I needed to find something and do more. So, I did a lot of research, and I found that the world needs more maintenance technicians, and so I thought well, that would be something worth a shot. Not only are there not enough qualified technicians, but there aren’t enough female technicians in it, to say the least. So, I ended up taking everything that I could while working. And unfortunately, the program at Summerset, you had to go Monday through Friday, 8 to 3, a very set-in-stone program and there was no bending in that at all. So, at some point, I did have to let go of the job that I had and just submerge myself fully into school. I’m very thankful I had a wonderful support system to help with my kid along the way. But that’s one of the things that I’m really excited about our program is that we are trying to remove those barriers and cross those areas off the list of things that may keep a potential industrial maintenance technician from pursuing their career path. So, it’s very exciting, and I’m really excited to be a part of all of this.
For more, tune in to Manufacturing Tomorrow’s Workforce.
Latest from Asset Management
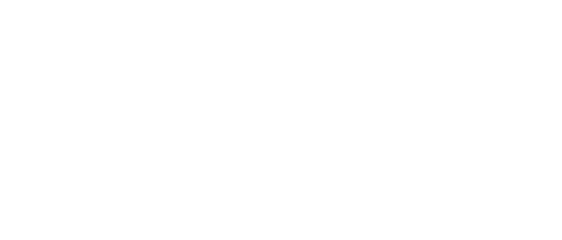
Leaders relevant to this article: