Manufacturing Tomorrow's Workforce: How to bridge the skills gap in product manufacturing
In the first full-length pod, Amanda Del Buono interviews Guy Loudon, president of the Jane Addams Resource Corp.(JARC), about the skills gap and 2019 workforce trends. JARC, which has an affiliated corporation in Baltimore, trains workers and connects them with employers in their manufacturing sector.
Transcript
AMANDA DEL BUONO: Hello, and welcome to the first episode of Manufacturing Tomorrow’s Workforce, a podcast about workforce issues in the manufacturing industries. I’m your host, Amanda Del Buono, and in this podcast, we’ll focus on workforce issues impacting companies and individuals across industries through in-depth interviews with a variety of experts about many different workforce-related topics.
To kick off the series, I’ll be speaking with Guy Loudon, president of the Jane Addams Resource Corporation, about some key manufacturing workforce issues, with a special focus on the skills gap.
Founded in 1985 and based out of Chicago with an affiliated corporation in Baltimore, the Jane Addams Resource Corporation trains workers and connects them with employers in their manufacturing sector. We’ll put a link to the Jane Addams Resource Corporation in the show notes, for those interested in learning more about the organization.
So, Guy, why don’t you start off by telling us a bit about your work at the Jane Addams Resource Corporation.
GUY LOUDON: Thanks Amanda, thanks for having us on the program. So, our mission's pretty straight forward. JARC helps low-income workers, job-seekers and community residents attain financial self-sufficiency through skills training and bundled services, but it's a dual-customer strategy, because we rely on our employer partners as the end customer in this approach. Our training programs target middle skills gaps in the regional labor market, including CNC Machinists, welding, press break operator, and we serve a variety of populations. So, in the JARC model, within these core competencies there's really two families of training programs. Our Careers in Manufacturing programs provide job training and employment services for a variety of unemployed adults, so that could be dislocated workers, you know, who's skills are obsolete or not really relevant in the labor market and they're coming here to learn a new skill set, but it also includes highly barriered individuals like returning citizens or maybe a female head of household, who she's been working raising kids for the last 10 years, but doesn't have skills developed that are relevant to the labor market. And then together with the technical skills training, we also offer an array of bundled support services to create a more holistic approach to helping the job-seeker succeed in the training program and then succeed in their life and careers once we've placed them on the firm side. We have a second family of training programs at JARC, our Business and Workforce Services design and execute customized worker training programs on the firm side. So, an example of that would be maybe one of our employer partners they hire people from our programs, but they also have skills gaps among their existing workers. So, they have us come in and teach a class it could be very basic skills like math or print reading, or it could be more hands-on technical training classes like welding or CNC or forklift operation, things like that. So, taken together, our job training and employment programs and, on the firm side, our worker training programs, taken together, these programs are really trying to be a relevant resource for our employer partners at all points along the skills gap continuum.
AD: Now, how do your employer partners get involved with JARC? How can a company touch base and take advantage of JARC as a hiring resource?
GL: So, our strongest, so, our relationships with employers typically start in a couple of ways. They may be looking for quality entry-level hires, and they're having trouble filling the entry-level positions they have. You know, if you know manufacturing's really rebounding, a lot of jobs are being created or coming back to manufacturing and a lot of people are having trouble filling those positions. So, a lot of times our relationships with our employers begin by them reaching out to us to see if we can provide them with a high-quality, entry-level hire. I mean, since 2011, I think we've placed close to 300 people in close to 500 firms. That's just in Chicago, that's not including Baltimore. But alternatively, sometimes our relationships with employers start on the firm side. They uncover skills gaps among their existing workers, maybe they buy a new, they're investing in a new technology, and they immediately discover that the workers they have aren't really equipped to run that technology. They're not even equipped to be trained to run that technology. But our strongest relationships with employers tend to be with companies where we're working on both sides of the problem. That is they're hiring out of our job training programs, but they're also retaining us to do worker training on site with their existing workers.
I wanted to say one more thing about employer engagement. One of the things that really builds a relationship is in all of our locations we have what we call an Employer Industry Advisory Council, and what that is is a group of close industry partners that are key stakeholders to our program. So, what we do in order to organize the employer's voice in our work is we organize the Employer Industry Advisory Councils that allow the employers to really share their perspectives, their expertise with us, to provide guidance and feedback in regards to curriculum and program design. Give us feedback on on how we're doing, not just with placing people at their firms, but the follow-up. Giving us that kind of feedback is very important. And also, the Employer Advisory Councils help us figure out what kinds of technology we should be investing and featuring in our program, so we can continually update our programs to be sure that they're relevant for the end customer, which is our employer partners.
AD: Why don’t we jump into the skills gap in the manufacturing labor force? How have workforce systems responded to the challenge?
GL: Sure. So, a lot of people are familiar with there was a landmark study in late 2012, published in 2013 I believe, by Deloitte Firm and the Manufacturing Institute. And at that time, they concluded that there were about 600,000 unfilled jobs in the manufacturing sector, and that study really became featured in a couple of very prominent national conversations. One was a conversation around manufacturing is really returning to this country, it's vital to the economic strength of our country, and a related conversation was you knowthe need to update our federally invested workforce system and make it relevant and high-performing for the private sector. And so, the Deloitte Manufacturing study really galvanized a lot of attention around the need to update and improve our federally invested workforce system and make it more responsive to the needs of manufacturing. So, the good news is that those conversations have taken a very favorable turn for manufacturing.
One of the indicators of that was that in the second Obama term the Workforce Innovation and Opportunities Act (WIOA) passed by a margin of 413 to six in the House and 95 to three in the Senate, which if you look at our current political environment, that doesn't happen very often. But what it showed was that there was really a strong public/private support for improving our workforce system and making it more responsive to the private sector. And one of the features of that in the new WIOA, the new Workforce Innovation and Opportunities Act, was that it very explicitly now favors sector strategies, that is focusing on middle-skills jobs and career paths in strategic sectors, like manufacturing, in fact manufacturing is called out in the legislation, and was very much in the political narrative around the passage of WIOA.
So, that's all the good news. The more sobering news is that despite all of that attention, the skills gap's continued to widen. Deloitte Manufacturing did a follow-up to their survey in 2015/16, and they concluded that despite the favorable turns, despite the renewed attention and investment in our workforce system, and attention to manufacturing, the skills gaps in manufacturing are projected to widen. They're now projecting that by the year 2025, there will be 2.5 million unfilled jobs in manufacturing. So, when we talk about a lot of the favorable news that we've seen relative to the labor market, I mean that's just kind of one of the sobering indicators is that in terms of responding to opportunities in manufacturing, in terms of helping to connect lower-income workers and job-seekers with middle-skills opportunities, jobs and career paths, we still have a ways to go. And I think that's a challenge that's still in front of the manufacturing sector and organizations like mine and the workforce system as a whole.
For more, listen to the Manufacturing Tomorrow's Workforce podcast.
Latest from Asset Management
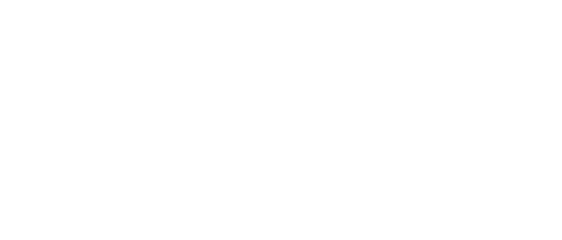
Leaders relevant to this article: