Taking a turn from the normal interview format, this Manufacturing Tomorrow’s Workforce podcast brings together a roundtable of Putman Media editors to discuss the workforce trends and challenges they’re seeing as they report on their respective industries. You’ll hear from Jim Montague, executive editor of Control magazine and ControlGlobal.com; Pan Demetrakakes, senior editor of Food Processing magazine and FoodProcessing.com; and Christine LaFave Grace, managing editor of Plant Services magazine and PlantServices.com.
Transcript
Amanda Del Buono: Hello, and welcome back to another episode of Manufacturing Tomorrow’s Workforce. Today, we have a special pod in store for you. We brought in several of our editors to discuss the workforce issues they’re reporting on within their various industries.
So, joining me today is Jim Montague, executive editor of Control magazine and ControlGlobal.com, and he’s also the host of the Control Amplified podcast. Thanks for being here, Jim.
Jim Montague: Glad to be here.
AD: We also have Pan Demetrakakes, senior editor of Food Processing magazine and FoodProcessing.com, here today. Thanks for joining us, Pan.
Pan Demetrakakes: Delighted.
AD: And last but not least, a regular interviewer here on Manufacturing Tomorrow’s Workforce, Christine LaFave Grace, managing editor of Plant Services magazine and PlantServices.com. Thanks for taking on the interviewee role today, Christine.
Christine LaFave Grace: Thanks very much, Amanda.
AD: I know you’re all quite busy, so we’re just going to get started here.
I guess, Jim, can you start by telling us about how the companies you cover are dealing with the skills gap, brain drain and other buzzwords that we’re hearing about for shrinking workforces and other workforce issues?
JM: Well, they’re often not dealing with it very well. The skills gap, brain drain, or whatever you want to call it, has been a recurring theme in just numerous Control interviews and conference sessions we’ve attended over the past, you know, 10 or 12 years. This is due to the reality that baby boomer engineers, technicians and other experienced veterans have just been retiring in much greater numbers than they’ve been replaced. I haven’t seen the latest numbers, but there are reportedly hundreds of thousands of skilled manufacturing jobs that are going unfilled each year. As a result, the know-how required to run many manufacturing processes efficiently has been just walking out the door, and many companies haven’t been able to capture it and pass it along to new employees, if they can get them. Consequently, many manufacturers have been recruiting, but they report the usual advertising, including online job boards, just don’t work. One packaging machine builder, R-Pack in Shiller Park Illinois, told us a few years ago that they even put a billboard up on a nearby expressway, and it didn’t produce results either, which is why it has taken them a year to fill an engineering position.
At the same time, many process discrete manufacturers and system integrators complain that young people apparently only want to be sports or entertainment stars, lawyers or FBI agents, doctors or nurses or other jobs that they see on TV, and believe that manufacturing is just dirty if they think about it at all, and they don’t want to take on the math and science courses usually required for them to become engineers or technical professionals.
There are several ways to combat the skills gap and the brain drain, but the require companies to be a lot more proactive than they’ve been before.
AD: Right. Well, Pan, kind of in line with people kind of viewing these jobs as that, Food Processing's 2018 Job Satisfaction and Salary Survey asked people who are in the jobs, what they are frustrated with. Can you kind of tell us a little bit about some of those things people were saying they’re frustrated with in their manufacturing jobs?
PD: Well, just to be clear, that particular article, that particular survey, had more to do with the white collar than blue collar workforce. And they are affected by the same trends that are affecting really American business as a whole, which is that companies want to keep costs down and there’s more competition for qualified potential employees in times of low unemployment, So as a result, a lot of positions are going unfilled, and this impacts workers in the obvious way of having to do more work. In the comments section of the survey, several respondents mentioned having an increased workload. “Required to handle more than one person can handle,” one guy wrote, “Too much to do with under-qualified staff,” another one said. And beyond that, beyond their own personal burdens, they also, in many cases, see that it’s affecting, having a detrimental affect, on the company’s development as a whole. 56% of the respondents said that they saw positions going unfilled, and 21% saw that and agreed with the statement that “unfilled positions are constraining our capacity or preventing us from expanding.” So, that means that it’s obviously a series problem, a serious situation, if even the rank-and-file blue collar employees can see it and are concerned about the future of the company in that context.
AD: Sounds like it. So, Christine, Jim and Pan have kind of talked about this inability to get people in the door. What has Plant Services seen in terms of getting people in the door to fill that gap and fill these open positions that everybody seems to have?
CLG: Yeah, absolutely. It’s far and away the top challenge for respondents to our 2018 workforce survey. Our findings really complement what Pan was talking about with Food Processing’s survey, and as far as Jim’s point, yeah, I think it was the latest 2018 numbers from the DeLoitte and Manufacturing Institute study, found that up to 2.4 million manufacturing jobs could go unfilled by 2028. It’s a really pressing concern, and for our respondents, it’s a concern right now. More than 70% of people who took our 2018 workforce survey ranked filling jobs that are open right now, finding skilled workers to fill positions that are already open, as their top workforce challenge. The immediacy of that is notable, too, because we also asked about addressing future hiring needs, you know planning to meet future hiring needs, the challenges that they will face maybe five years from now as even more boomers retire. That was much less of a concern for our respondents than meeting their hiring needs today. It’s a good and the bad, it’s a double-edge sword with the economy as it is and with manufacturing, in particular, as strong as it has been, as robust as it has been in the past year.
One of the sources I actually spoke with for our story about the survey’s findings was a guy named John La Bla, super intendent of a vocational high school that’s based in Andover, Massachusetts, which was part of the second industrial revolution, 130 years ago, great textile region, and in the second half of the last century, plants closed, jobs moved abroad, work class was really devastating for the region. But now, different productions, more high-tech production, different companies are really growing in the area, and John said for every student in his vocational training program, every student that their program puts to work, employers in his area probably need three or four more. When I spoke to him last summer, he had had a call the week before from a company that was looking for 10 students, 10 students to come in and help fill the roles. So, the need is there, it’s how to fill that need that manufacturers are really struggling with.
For more, tune into the Manufacturing Tomorrow’s Workforce podcast.
Continue Reading
Latest from Asset Management
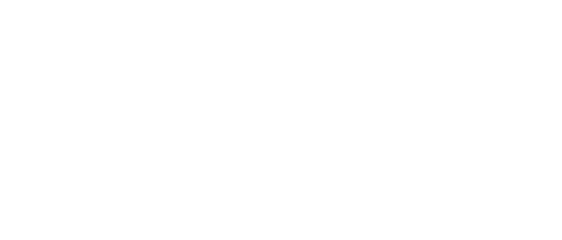
Leaders relevant to this article: