One constant required for any sensor or actuator is a need for power. Commonly used power sources for field devices include instrument air, hydraulics and electricity. Fortunately, wireless sensor networks (WSN), which include IIoT devices, do not require continuous power, and the power levels they do need are quite low. As a result, energy scavenging techniques are a viable option that can be considered.
Energy scavenging—also known as power harvesting or energy harvesting—is the process in which energy is captured from a system's environment and converted into usable electric power. Energy scavenging harnesses small amounts of ambient energy, which otherwise dissipates or gets wasted. It allows electronics to operate where there's no conventional power source. This eliminates the need to run wires or manage batteries.
An energy harvesting system generally includes circuitry to charge an energy storage cell and manage the power, as well as regulate and protect the system.
The common sources of ambient energy that can be scavenged are:
- Light energy (captured by photovoltaic cells);
- Kinetic energy (vibrations and mechanical stress captured by a piezoelectric element);
- Thermal energy (captured by a thermoelectric generator); and
- RF energy (radio waves captured by an antenna, such as in RFID systems).
Solar cells are very common; however, when they are dependent on solar light as their only source they have the disadvantage of not being able to harvest at night. That creates the need for battery storage. They also require maintenance to keep the solar cell surface “clean.” For example, in Canada, that means snow.
To illustrate how ubiquitous energy scavenging systems are, a few examples of piezoelectric harvesting include:
- Pressure sensors on car tires: Piezoelectric energy-harvesting sensors are installed inside the tires of cars. They monitor the air pressure in the tires and relay this information to the dashboard;
- Battery-less, remote-control units: Remote control units where piezoelectric transducers convert the force of the buttons being pressed into energy that powers the remote’s IR signal; and
- Piezoelectric “shoes”: sparkling running shoes worn by children.
One of the early WSN piezo-based energy scavengers used the natural frequency of the process pipes themselves to cause what was effectively a “tuning fork” to oscillate and harvest the energy from the oscillation. The problem with this system was the process operated at different process conditions. That moved it outside the systems calibrated frequency range. No more oscillations meant no more energy.
A thermoelectric harvesting system is based on a thermoelectric generator (TEG), which consists of several thermocouples connected in series to a temperature differential to generate energy directly proportional to the temperature difference as well as the size of the TEG. Therefore, as the temperature differential changes, so does the available energy.
Some other ideas which could work in some applications include a turbine installed in the instrument air supply for an actuator, but with actuators being designed to minimize air consumption. This option will need both a reliable air supply and to continuously bleed to atmosphere. If you are running air to the device, chances are a reliable power supply is around as well.
Another idea is a paddle inserted in the process with spring or hydraulic reservoir to push back so oscillation can generate electricity like wave generators offshore. This does require another penetration into the process line and a potential emission source. Since it is mechanical, it will likely need maintenance and a way to isolate it. The result is more complexity.
Meanwhile, miniature fuel cells, which have the advantage of not requiring replacements, are still in the research stage. If attached to a sensor “vent” could provide the fuel for 24 x 7 power.
As mentioned for each option, almost all the energy scavenging systems have one or more limitations that restrict their use with the associated risk of not always being available.
This is why every energy scavenging system requires some form of energy “smoothing” or storage, which can be either a capacitor to bridge short fluctuations or, as is more often the case, a battery.
If you are going to use a battery, many applications simply reduce complexity and go battery all the way, which is one of the main reasons why most of the time that is what is done. Manufacturers using batteries also need to consider that the EU has regulations on cradle-to-grave management of batteries, especially if they use metals such as lithium.
Energy scavenging will continue to evolve, largely driven by IoT applications in the commercial space. As this happens, we will see the technology move to the industrial sector and a decrease its dependence on battery storage.
Continue Reading
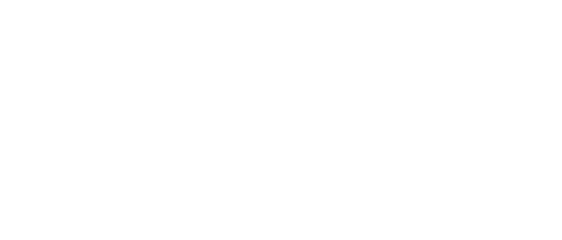
Leaders relevant to this article: