Continuous systems have existed alongside of, and in competition with, batch systems throughout modern manufacturing history. Both approaches have their champions and both have advantages and disadvantages, which leads to competition between the practices.
Batch systems generally require less capital to build, but are considered more difficult to operate, which offsets the cost advantage. Batch is dominant in areas such as pharmaceuticals where material genealogy tracking is important. Continuous processes dominate areas where mass production is important, such as petrochemicals.
At Procter & Gamble, we apply a mix of these types of systems. Sometimes we have the same products made on both continuous and batch systems. There is continual debate as to which is the best manufacturing approach, and, based upon business requirements, the right answer is sometimes "both!"
The examples below are similar to several systems that have been successfully implemented within Procter & Gamble. Some of the aspects of these systems have been generalized for simplification, but the significant details remain.
Physical Differences
A simple example batch system uses two units and five different materials (Figure 1). The two batch units use weigh scales to indicate the amount of material added. As such, they can only add materials sequentially, which will dictate the batch cycle time and therefore how much material can be created in a given period of time.
Figure 1: Simple Batch Example
A simple example batch system uses two units and five different materials. The batch units can only add materials sequentially, which dictates the cycle time and hence the production rate.
A continuous system that makes the same product (Figure 2) has all of the same processing capabilities; they are just performed in a different manner. There is significantly more processing equipment, so capital costs are typically higher. The continuous production is controlled by a final-product flowmeter against which all other flowmeters are proportionally controlled.
There are six materials in the continuous system, as Recycle has been added. This is a common requirement because an indeterminate material is created during transition times (startup, shutdown, and running product change). Rather than waste this material, it is common to blend it back in. The philosophy in the batch system is to make sure the product produced is right before sending it to product storage, therefore no recycle handling equipment is required.
Material handling can vary significantly between batch and continuous systems. Continuous systems generally include recirculation lines to reduce the amount of recycle produced. These provide a method to fill the supply line and guarantee proper operation of the flow-monitoring instruments before the full system is started. This is not needed in batch systems that use weight control, because empty lines do not affect accuracy, they only delay delivery.
In both the batch and continuous systems, when a material is not being used for a given product, the supply lines are cleared with compressed gases.
Operational Differences
Some believe the only difference between continuous and batch is the length of the steady state. Others say a batch is just a continuous system in a continual flux of startup and shutdown. And one good friend says they are "exactly the same--except for what's different." People who have worked with both know that what's different is significant. The focus of continuous systems is running, which can be hours, days, weeks, or longer. Continuous systems can generally make more product in shorter time than comparable batch systems; this is one of the primary advantages of continuous systems.
Figure 2: Equivalent Continuous Example
A continuous system that makes the same product as Figure 1 is controlled by a final-product flowmeter against which all other flowmeters are proportioned. More equipment means higher capital costs, but typically higher production rates.
The traditional focus of operations for continuous systems is the startup, which is a one-time event. These systems mostly take care of themselves after an operator has "lined out" the system. Batch systems, on the other hand, traditionally have required "continuous" attention by operations as product is made. Thus, we see a tradeoff in the cost of equipment vs. the cost of people.
Automation Differences
The traditional approach to automation of a continuous system has been to rely on industry-standard controllers that maintain the flows of materials at ratios against the total flow of finished product. This is well-understood technology and easy to successfully implement almost anywhere. If there is any automation in the startup of the system, it traditionally has been custom, leading to very complex monolithic systems that only a few people understand and even fewer can support and modify. As with older batch systems, any change in product formulation becomes difficult to manage.
Since the early 1990s, batch systems have received a lot of attention because of the ISA 88 standard and the many newly available products to automate the continual starting and stopping of batch manufacturing. This led to many products that are designed to manage both a product recipe and the process sequence to create that product.
The modularization techniques recommended by ISA 88 have proven to be extremely effective in automating batch systems, and have become the batch industry standard approach. Many of these automated systems now run with even less attention than their continuous counterparts.
During the early days of the ISA 88 definition effort, it was observed that the standard could apply to all forms of manufacturing and not just batch. While most everyone agreed with this, Thomas Fisher had the wisdom to keep the focus only on batch: He said there never would be an ISA 88 standard if we attempted to reach too far, and continuous was too far at that time. It may still be too far today, but may not be tomorrow.
A Merging of Technologies
In three successful applications, Procter & Gamble has been able to blend batch and continuous technologies to create systems that use batch automation technology to manage product formulation and recipe, use batch sequencing to automate startup of a continuous system, and retain the traditional continuous operation automation that is so comfortable to manufacturing.
This has required a mind shift in modularization of the continuous systems by those responsible for the process and its automation. This is no small task, but once done the benefits are eventually obvious, and it becomes the property and philosophy of the engineers who own these continuous systems. It is unfortunate that they do not have a method to broadly share this information, since it seems to reside in small groups and is not widely accepted.
The implementations consist of three independent "managers," one for recipe management, one for the start-up sequencer, and one for continuous operations.
The recipe manager uses the standard ISA 88 guidelines and is a commercially available package that we are able to use as-is. This has allowed all in charge of the product specification to have their intent directly applied to the actual production, and this has had a significant positive impact on data entry mistakes. By removing the need to program a recipe into the controller, the time it takes to introduce a new recipe has been drastically cut and the errors generally experienced in its rollout have been greatly reduced or even totally eliminated.
The start-up sequencer uses a standard ISA 88 Equipment Phase (Figure 3) to interface with a commercial recipe sequencer that manages three phase types: initialization, material, and sequencer run. Each phase interacts with components of the continuous manager.
Figure 3: Phase States
For continuous processes, the start-up sequencer uses a standard ISA 88 Equipment Phase to interface with a commercial recipe sequencer that manages three phase types: initialization, material, and sequencer run.
The Initialization Phase clears all pending material information and informs the continuous manager that a new recipe download is in progress. The Material Phase provides the materials for this recipe, with all the necessary information, and issues a request for those materials to proceed to their ready states if they are not already there. The Sequencer Run Phase provides all other recipe-processing information, such as temperature and residency times; informs the continuous manager that all materials are ready for production; then terminates the Recipe Start-Up Sequencer.
Functionally, the Start-Up Sequencer replaces the manual operation of bringing the material paths to a useable state. It eliminates the varying effects of different operator approaches, resulting in much smother operation and better quality product sooner.
Material Equipment Modules
The ISA 88 Control Module concept is used to manage each individual piece of equipment: one for the pump, one for each block valve, etc. These Control Modules are in turn controlled and coordinated by an Equipment Module (EM) that orchestrates the Control Modules to carry out the necessary process functions.
The Material EM states and actions are represented in Figure 4. These provide a bridge between the Start-Up Sequencer and the Continuous Production Manager. As indicated, the Material EM can receive transition commands from three sources, the Start-Up Sequencer, the Continuous Production Manager (by operator action), and itself.
The Start-Up Sequencer provides recipe information in a "pending" storage area for the Material Equipment Modules; upon production start-up, this information is transferred to a "running" storage area and will be used for production. The operator has access to all this data and can modify it within the parameters of the recipe.
By creating a single, modular EM for material transfers and then reapplying it for all material transfers, the engineering effort is greatly reduced over traditional approaches. It also proves to be much easier to support than previous monolithic systems, and necessary changes to the process are now more easily accomplished.
How Continuous Production Operates
The Continuous Production Manager has three modes: Full Auto, where it will rely on the Sequencer for "advice" and the Operator for confirmation; Semi-Auto, where the operator can assume direct control of the EMs [bypassing the Sequencer and Continuous Production Manager (CPM) but taking full advantage of the EM logic]; and Manual Mode, where the operator takes direct control of all Control Modules, bypassing all other control and logic.
In Full Auto, during the initial startup of a recipe the CPM is waiting for indication that all required materials have reached the Started state. Once that has occurred and the operator signifies the start of production, the CPM instructs all required materials to proceed to the Run state. During this time the production rate is maintained at the minimum setting and all material produced is directed to the recycle vessel.
When the operator is satisfied the product quality is at target, production is redirected to product storage and the production rate is set as desired. Any system upset affecting quality will cause the rate to be set to minimum and will redirect product to the recycle vessel waiting for the operator's decision to Hold, Shutdown, or Resume production. If the operator chooses to Hold, all active materials are commanded to the Started state in which no product or recycle is produced. If the operator chooses Shutdown, all materials that are not already in Idle are commanded to the Shutting Down state, which will cause all material paths to be cleared and all equipment to go to its Off state.
When the operator determines conditions are right, the command to switch to product storage is issued and the rate adjusted as needed. In the past, only a few operators could successfully perform this function, and even then, it often lead to catastrophic results, shutting down production for significant periods. With the ISA 88 modular implementation, the Running Recipe Change has never failed.
There are times and situations where continuous systems are appropriate and where batch systems are appropriate, and there are situations where either could be used. Using the modularization recommended by the ISA 88 standard has significantly reduced the effort and cost of automating batch systems, and these approaches have been demonstrated to improve the automation efforts of continuous systems. But getting this approach accepted by those who do the automating is difficult, with most still following the traditional monolithic automation approach.
The recipe management and sequencing capabilities of commercially available batch products have also greatly improved operational management and execution of continuous manufacturing, though again, gaining acceptance is difficult. There are groups that believe strongly in the superiority of continuous manufacturing and they will go to great lengths to prove it, including rejecting any automation techniques that are shared with batch systems.
When the reluctance to use the ISA 88 concepts is overcome, continuous systems realize the same improvements found with batch systems. In fact, batch and continuous are exactly the same...except for the differences.
David Chappell, batch technology manager at Procter & Gamble, may be reached at [email protected].
Figure 4: Continuous EM States and Actions
The continuous material equipment module (EM) states and actions provide a bridge between the Start-Up Sequencer and the Continuous Production Manager:
Final State Idle (EM initiated)
Lines drained
All equipment off
Hold
Transient State Starting (Sequencer initiated)
Recirculation equipment on
Waiting for flow indication
Command to started
Final State Started (EM or Operator initiated)
Lines full
Recirculation equipment on
Production equipment off
Hold
Transient State Transition (Operator initiated)
Transfer material information to continuous storage
Recirculation equipment off
Production equipment on
Waiting for production rate
Command to run
Final State Run (EM initiated)
Rate to production
Transient Shutting Down (Operator initiated)
Clear material information in continuous storage
Source valve closed
Equipment energized
Air valve opened for line drain until lines flushed
Command to idle
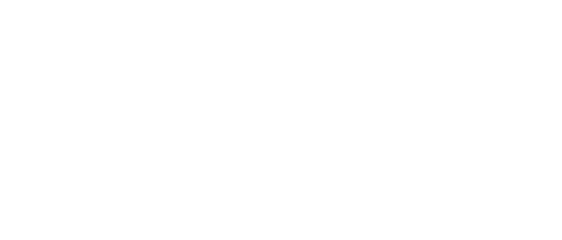
Leaders relevant to this article: