To distribute or not to distribute, that is the question. Is it nobler to use one, large, centralized control system for the entire plant or process? Or is it better to use a number of small, field-based distributed controllers, each dedicated to a particular machine, process, or control loop? Those are the questions, and the answers are changing rapidly due to advances in communications, ruggedness, and software standards.
Process control systems used to be highly distributed because large, centralized, computer-based control systems were simply not available. Local processes were controlled by a combination of relays, timers, and pneumatic or electronic loop controllers. These hard-wired systems were interconnected by contacts and 4-20 mA signals. Operators and technicians roamed the plant in droves to monitor operations and maintain system components.
Ironically, the misnamed distributed control system (DCS) was perhaps the leading agent for control centralization and the chief cause of the demise of distributed controllers. These systems were installed in central control rooms and connected to field devices through miles of dedicated wiring. They served the industry well for decades and did much to improve the operation of large process plants.
In the past few years, a new class of field-based controllers has emerged and is making distributed control a more viable option. These controllers are small, inexpensive, rugged, and equipped with high-end communication capabilities. Cost-effective control of local processes is now possible, and fast, reliable networking of these islands of control is easily accomplished.
Figure 1: Hard Case
Some distributed controllers are housed in enclosures that can be field-mounted without control cabinets. (Source: Phoenix Contact)
Controllers that can be field-based in a distributed control system include micro-PLCs, smart I/O, smart motor starters, smart pushbuttons, smart valve controllers, field-mounted solid-state controllers (Figure 1), and single and multi-loop controllers. Smart products can perform local logic or process control functions and can communicate with central controllers over digital communication networks.
As recently as five years ago, field-based distributed control was impractical. In 1998, a 100 I/O PLC with an open communications protocol such as Ethernet cost about $5,000. At those prices it just didnt make sense to distribute control to the field. Today, a 100 I/O PLC with Ethernet can be purchased for less than $500.
Comparable performance increases can be found in field-mounted solid-state controllers and in single and multi-loop controllers. Smart components with open communications protocols such as I/O, motor starters, pushbuttons, and valve controllers are recent additions to the field-based distributed control team. These products add local logic and process control along with digital communications into footprints not much larger than those required for similar "dumb" components.
These incredible leaps in performance make distributed control a much more attractive option for many processes.
The Case for Field-Based
Technology has made distributed control viable, but process needs are driving its adoption. "Field-based controllers are faster and can be dedicated to a specific control application," says Matt Bothe, senior automation engineer, CRB Consulting Engineers, Plymouth Meeting, Pa. "Distribution of control functions can reduce wiring, facilitate maintenance, and increase the speed of logic and process control."
Field-based controllers also offer other advantages over centralized control systems (Table I). North Fork Electric, Crumpler, N.C., is a systems integrator for AutomationDirect and other vendors. President Andy Feimster says, "In critical control applications, distributed controllers may offer a level of safety and dependability that centralized control systems (whether they be PLC, PC, or DCS) cannot."
Field-based controllers reduce wiring, but so do centralized control systems with remote I/O. The problem is these remote I/O systems can cause heavy traffic on communications networks. Moving intelligence to field devices and to smart I/O allows control to be accomplished locally, thus reducing network traffic.
Status information concerning the local process is still transmitted to other controllers, but time-critical data used for real-time control does not need to be sent over the network. "Less information needs to be handled by the communication path, and I can choose exactly what information to send to the main control system," observes Paul Parker, cogeneration plant engineer with KSL at Los Alamos National Labs, Los Alamos, N.M.
Some processes are just too fast-acting for a centralized controller. "A single controller running a lengthy program can be slow on event-triggered interrupts," says Jeff Birch, president, Industrial Control Services, Centralia, Mo. "We use several dedicated controllers to isolate critical programming and maintain reaction times."
But there are still good reasons to use centralized control (Table II). In many cases, the hardware is still less costly. If a process has 500 I/O, one large PLC will be much cheaper than 10 small PLCs each controlling 50 I/O. These same cost calculations hold if the field-based controllers are devices other than PLCs.
Rugged controllers suitable for field mounting can reduce field installation costs, but not all processes are suited to control by these types of devices. In many cases, not only will a centralized controller be cheaper, it will also be less expensive to house. "An air-conditioned control room serves to remove the heat from a centralized controller, but if you distribute controllers out to the field then mounting issues must be considered," notes Jim Loar, engineering group leader at Ciba Specialty Chemicals, Newport, Del.
Most field-based control systems use different types of hardware from a number of vendors. This can make training, maintenance, and support a real headache. "As a company we try to discourage the use of these new field-based devices because they do not fit our overall strategy of moving to centralized control and maintenance," reports Dale Evely, PE, I&C consulting engineer with The Southern Co., Birmingham, Ala.
There are general pros and cons for using centralized vs. field-based distributed controllers, but in most cases either solution can be made to work,the decision is driven by the details. Application examples can help users make the best choice for their processes.
Easier to Expand
A control system must be expanded when new equipment and processes are added. Building onto a centralized control system can be problematic because some downtime is usually required to add hardware. The software program must be modified--this also requires downtime and can have inadvertent effects on the existing control scheme.
These problems can be alleviated if instead the new process is installed with its own control system. The control system can be tested and verified prior to connection to the main system, and downtime and risk can be minimized.
Engineering firm Wink Inc., New Orleans, decided to use Modicon distributed controllers and an Emerson DeltaV central controller on a recent project. "Facilities are in constant upgrade due to the expansion of the system, and distributed controllers have allowed us to upgrade and expand the control system without upsetting the main controller," reports Pedro Egui, Wink senior instrument engineer.
Many process plant expansions are implemented with packaged systems, and these are a natural fit for distributed controllers. "Plants can purchase a self-contained skid package such as a separator, a chemical injection system, or a filtration system," says Ian Verhappen, director of systems integrator ICE-Pros (www.ice-pros.com). "All controls are configured by the supplier to take advantage of their expertise and familiarity with the process and equipment."
Installation is simplified by digital bus technologies. In most cases, a single cable can provide all necessary two-way communication with a central control system. Add power to the packaged system and perhaps a hard-wired contact or two for backup alarming, and the installation is complete.
Many field-based controllers have a built-in human-machine interface (HMI), so they can be used to provide full control and operator interface for a small system. Expansions can be made without forfeiting any previous expenditure. "Foxboro makes distributed controllers with built-in trending, alarming, batching, and even printing capabilities," observes Stephen Arnold, systems manager at Neal Systems, Newtown, Pa. "These controllers allow a user to put a small system in place, often without the need for a central controller."
Simpler to Fix, Harder to Manage
Reliability can be enhanced with field-based distributed controllers because a single point of failure (the central controller) will not cause the entire process to fail. "Distributed controllers allow users to maintain limited production in case of controller failure," says Egui. Reliability is also improved because local operation does not depend on a plant-wide control network.
All things being equal, it is easier to troubleshoot a small system than a large one. This is yet another reason for using field-based distributed control. "Distributed controller software programs are easier to maintain because there is no need for multiple subroutines. Modularization of our control systems have allowed us to add focused diagnostics, thus expediting troubleshooting sessions," says Birch.
It is also easier to separate and partition small as opposed to larger systems. This can be important for safety systems. "Safety is enhanced with distributed controllers because critical and non-critical interlocks and alarms can be zoned according to the controllers physical distribution," reports Egui. Safety can also be improved by using the local operator interface provided with many field-based controllers.
Field-based distributed controllers have many advantages as compared to centralized controls, but perhaps their biggest drawback is maintenance of multiple controllers from different vendors. This causes headaches in maintenance, training, and software change management. In many cases, these problems will be significant enough to preclude the use of field-based controllers.
The proliferation of PCs has been a nightmare for many IT system administrators. Some firms are moving back to a central computer system with thin clients to regain control of their corporate computing systems. In a similar vein, many users see value in central computing systems.
"Control software management is much easier with centralized controllers. It is also easier to tie one controller (rather than many) into our overall strategy of enterprise wide information collection and analysis," says Evely.
It may be easier to troubleshoot a small system than a large central controller, but this advantage is often negated when plants are populated with different types of field-based controllers. "With a central controller, we do not have to train personnel on multiple control devices. We do not have to maintain multiple spares, and we can use a single programming tool for all of our troubleshooting/development needs," says Andrew Rowe, the technical manager-process controls and MIS with the United States Gypsum Co. in Chicago.
With field-based distributed controls, maintenance personnel must be familiar with multiple software programming packages and they must also know how to program field-based controllers at the faceplate. This is no trivial matter because many of these local controllers can be very difficult to program, especially if they are only revisited on a sporadic basis as problems occur.
Do You Really Want to Distribute?
Some end users think they want and need field-based distributed controllers, but they change their minds after implementation. CH2M Hill, Herndon, Va., recently completed an expansion of a waste treatment facility. Operators insisted on field-based distributed controllers because they didnt trust the DCS and because they wanted local control of the process.
According to Scott Farrell, CH2M Hill designer, the operators have now become comfortable with, dependent on, and confident in the DCS. "If we were to design this process now it would be without the distributed controllers," says Farrell. "One of the most difficult parts of the startup was programming the distributed controllers and establishing communications with the DCS."
Farrell has long-term (17 years) experience with a wastewater treatment plant that uses a DCS for its central control system and a variety of PLCs and distributed controllers as subsystems. The system was originally designed to use distributed controllers to provide redundant backup for key systems and to placate operators familiar with local control. "The reliability of the DCS and the addition of remote I/O has eliminated the need for this type architecture," he says. "The distributed controllers are being eliminated by attrition."
A good rule of thumb is to use field-based controllers only when a central computer cannot effectively control the process. "There is nothing inherently wrong with distributed controllers; they often offer more sophisticated control algorithms. They also offer independent control that could possibly be maintained during a central control failure," says Rowe. "But without a need for the sophistication and small-scale mission critical control, the central control approach best fits our needs."
But there are already increasingly good reasons to use field-based control, and industry evolution might yield other compelling advantages. "Distributed control will lead to an array of self-contained controllers with highly specialized control algorithms such as fuzzy logic, neural networks, multivariable predictive, specialized model-based, and iterative convergence control technologies," says CRBs Bothe. "For most processes, it is a mistake not to evaluate distributed control as an alternative or a supplement to conventional topologies."
Special Functions Are Fulfilled
Specialized control applications can be a good fit for distributed control. Systems integrator Synergy Systems, Naperville, Ill., uses distributed controllers for furnace combustion control.
"A Foxboro T640 controller can provide combustion master (steam header pressure or furnace temperature) loop control by sending demand to a fully metered cross-limited combustion control of air and fuel loops with load-compensated O2 trim controller," says Mark Urda, Synergy president. "Not bad for a single controller that costs about $2,500."
It would take dozens of rungs of code to provide the necessary control scheme with PLC ladder logic, according to Urda. It also would be far more difficult to troubleshoot ladder logic as compared to the simple function block approach of a distributed controller system. He says a DCS could easily duplicate the distributed controller logic, but at a much higher price.
Another specialized application is field-based controllers in hazardous areas. Weatherford Intl., a Houston-based oilfield services firm, uses Beckhoff Automation controllers on oil drilling rigs in Class I, Div. 1 environments. Jorge Pinal, a rig system installation supervisor for Weatherford, says it is much easier to field-mount these relatively small controllers than a large central controller.
"Some field-based controllers can be used in intrinsically safe installations," Pinal says. "Even if the installation cannot be made intrinsically safe, these small controllers can be easily installed in NEMA 7/9 boxes without venting or cooling systems."
Valves Do It in the Field
Smart valves are becoming more intelligent, to the point where some of them are as capable as single-loop controllers and even small PLCs. For example, CRB Consulting Engineers, Plymouth Meeting, Pa., installed a Valtek smart control valve with StarPac electronics for lube oil temperature control. The system is for a 2,500 hp ethylene motor/compressor assembly at a bulk chemicals production facility.
Temperature readings are transmitted from the mixing assembly (after the convergence point for the hot and cool oil streams) to the valve, from the cooling water output, and internally through sensors on the valve body. Pressure sensors located at an upstream point and near the vena-contracta of the valve plug provide pressure information (see figure).
According to Matt Bothe, CRB senior automation engineer, these four analog signals coupled with the analog output to the valves I/P result in a highly versatile control strategy with unprecedented performance. All the above information is available to an existing central controller via RS-485 Modbus.
"From a maintenance perspective, the valve provides as-installed performance information (e.g., valve signature) so comparisons could be made to future similarly derived signatures in an effort to assess degradation over time," says Bothe. "Key components of degradation such as stiction, hysteresis, sluggishness, and overall response were then strategically applied for scheduling preventive maintenance activity."
Valves with pneumatic controllers can be effectively retrofitted with field-based smart valve controllers. "We would like to upgrade our old Fisher Wizard pneumatic valve controllers with Foundation fieldbus hardware," says Southern Co.s Evely. "I dont know if this product exists, but we would like to install a local manual/automatic station that could sit on a Foundation H1 segment. The station would provide basic manual/automatic functions to a PID controller function running in either a transmitter or a control valve positioner on that same H1 segment."
Valve control is sometimes best accomplished with a locally mounted controller instead of with a smart valve. Viewpoint Systems, Watertown, Mass., recently installed an air control system for a semiconductor plant. Very precise and high-speed PID control was needed to maintain temperature within 0.05* F of setpoint. Viewpoint used a National Instruments FieldPoint controller to provide precise control of valve position.
The central controller communicates setup and control parameters while the local controller provides feedback alarm information, all via TCP/IP. "A unique aspect of this project was the requirement to fit these new control loops into an existing system," says Erik Goethert, Viewpoint branch manager. "The flexibility of the FieldPoint controller allowed us to customize the communication and control paths between the old and new systems."
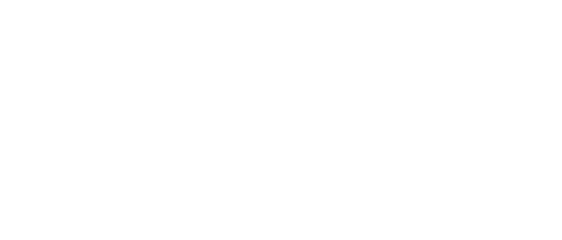
Leaders relevant to this article: