Sure, 20-year-old systems don't have all the bells and whistles that modern ones have, and yes, it can be a pain to find spare parts, but many of these legacy systems are like a 1963 fuel-injected, split-window Corvette coupe: That is, rare and expensive, but in its day technically advanced and still capable of performance equal to that of its modern counterparts. So like the Corvette, your legacy system was worth its price then and worth the time, money and effort now to keep it running.
Legacy of Value
For many processors the value of their legacy control system is measured by the huge capital investment made to purchase the original system. Its legacy is also represented by the commitment to all the sensors, transmitters, wiring, cable, cabinets, power supplies, digital and analog I/O, plant networks, redundant data highways, remote terminal units (RTUs), A/D converters, multiplexers, analyzers, distributed control modules and all the other specific elements and technologies that went into its creation. Old yes, but built to last (Table 1). So, while parts may be hard to find for a decades-old DCS, banking on its current value and investing in its future may be well worth it.
Besides, all your legacy system may really need to run like new is a few relatively inexpensive and simple software and hardware upgrades. But because so many factors can influence the success and cost-effectiveness of a legacy control system upgrade, before you step up, system vendors and plant operators recommend you step carefully along the path you take.
Step One: Upgrade Software
Upgrading system software can be one of the easiest and least costly ways to improve the operational aspects of a legacy control system, says Steve Garbrecht, industrial application server product marketing manager for Wonderware. Garbrecht lists an upgrade path in Table 2, where possible upgrades are ranked from the easiest (1) to the most costly (2).
Table 1: The Upgrade Path
He says bulldozing - completely replacing an old system with a new one - is rarely necessary. "Ninety-nine percent of the time, it is not appropriate to bulldoze your existing control system," says Garbrecht. Any vendor that does not provide an incremental capability is not serving their customers' best interests.
Because it is possible to update almost all legacy DCSs, let's start with HMI software, as the first step down the upgrade path.
Many HMI/SCADA software vendors offer plug-in compatibility with dozens of old DCSs. The software can interface with process historians, databases, PLCs, data highways, and even the system's RS232 ports to gain access to real-time or historical data. This almost immediately provides modern PC-based HMI trend displays, alarm screens, and fresh process graphics to replace the old stick-figure black and white displays you've been living with since the 1970s.
Moreover, a modern HMI/SCADA package also connects that creaky old legacy system to today's modern enterprise software, such as ERP, MES, and supply chain management applications. Built-in web servers also allow you to observe the process from a web browser on a PC.
"With our BizViz software, users do not have to rip out and replace older systems," says Tim Donaldson, marketing manager at Iconics. "BizViz is designed to mine data from legacy systems."
If all you think your system needs are better HMI displays and a connection to enterprise software, then modern HMI/SCADA software and a PC might be the best fit and the most cost-effective solution. For example, CRISP Automation, Raleigh, NC, offers an HMI upgrade package for its legacy systems based on commercially available HMI/SCADA software.
"We created a new HMI based on InduSoft's WebStudio software," says Ken Wild, president of CRISP Automation. Although CRISP and its successors Anatec and Square D are all essentially out of the DCS business, together those companies built and installed about 100 CRISP systems during their heyday, Now Wild works to keep them all running. "Our upgrade allows customers to import their existing operator screens into WebStudio," he explains. "It adds state-of-the-art functionality, such as allowing users to access their systems over the Internet or run their HMI on a handheld PDA."
Wild says the old CRISP systems have legendary reliability and are virtually bullet-proof. Originally based on DEC PDP-11 and VAX computers and I/O, these 1970s and 1980s-vintage systems just keep on ticking.
Like many companies with legacy systems, some CRISP users don't want to change. "No change in the application is very important to our pharmaceutical, food and chemical customers," says Wild. "Recertification is difficult, expensive and draining on internal engineering resources."
Jim Meils, critical systems supervisor at Aventis Behring, in Kankakee, Ill., agrees. "While an upgrade to a newer version of the same equipment may be technically easier, this will not improve the rest of the upgrade path, because our systems must be specified, commissioned, validated and submitted to regulatory agencies," he laments. "Most of our machines, including the control systems, remain the same until the entire system is decommissioned."
Owners of old Bailey Controls (now part of ABB) systems can also update via a software upgrade. Citect, an HMI/SCADA software vendor, has taken legacy Bailey DCSs owners under its wing, and offers an easy-to-implement upgrade path. "Citect has a lot of experience changing-out Bailey systems," says Brooke Mauro, services and partner channel development manager at Citect. "Customers can continue to use I/O and Bailey Infi 90 controllers, but they get the latest operator interface computer equipment and software."
Nufarm, an agricultural and specialty chemical manufacturer in Melbourne, Australia, used Citect to upgrade its Infi 90 system. "We needed to integrate all our plant data into one standard, easy to use interface," says Tuan Truong, Nufarm's project coordinator.
Nufarm just added a Citect HMI/SCADA software system to its existing Bailey DCS, and avoided any disruption to plant operations. "The system is a huge improvement in terms of presentation, user friendliness, control functionality, robustness, data exchange, data storage, remote access and support," says Truong.
Look around at the HMI/SCADA vendors to see if you can just buy a plug-in package. Prices start at less than $1,000, and systems are available from leading software vendors such as Citect, Wonderware, Intellution, Iconics, InduSoft and several others.
As noted, many processors have a significant investment in I/O, field instrumentation, PLCs, cabinets, controllers and other hardware that continues to work just fine. Therefore, the next step along the upgrade path is to keep as much of it as possible and upgrade or replace only what you must.
Before starting any upgrade project, Foxboro/Invensys checks the old I/O to be sure it is up to the task. "In 99.9% of the cases, we find no corrosion present and no need to rip out cabinets or wiring," says Betty Naylor-McDevitt, director of migration at Invensys. "This is due in part to the fact that many older legacy systems required installation in clean environments. The wiring and infrastructure installed in such environments will last virtually forever. So, when it comes to wiring and fixtures, we say - if it ain't broke, don't fix it."
Joel Young, vice president of engineering at Digi International, Minnetonka, Minn., says that adding connectivity to legacy systems is a big part of Digi's business. "We make it possible to extend the life of existing systems with only an incremental investment," explains Young. "We provide a path by which connectivity can still be used as other components get replaced."
Young describes a system Digi installed at ChevronTexaco: "Chevron needed to integrate 200 of its Square D SyNet PLCs with Wonderware software via Ethernet. The existing PLCs used a proprietary system that required a specialized PC board. To further complicate the issue, the PLCs were no longer in production and were not Ethernet compatible."
What to do? Replacing 200 PLCs would be extremely costly. Besides, the PLCs were performing their control tasks admirably. The old technology just couldn't talk to the new HMI.
Digi connected the legacy PLCs to the HMI PC with its off-the-shelf RealPort communications module, so that Chevron could continue operations with no changes.
Schneider Electric has an interesting way of upgrading an old network. "Install a Telemecanique Momentum PLC that can translate other vendors' network protocols," advises Joe Eiden, segment manager at Schneider. Once the Telemechanique PLC gains access to the legacy network, you can take advantage of its built-in web server, XML programming and other languages to integrate it to higher-level systems.
Step Two: New HMIs
If you are working with a "modern" HMI/SCADA system that's more than a few years old, it's probably running on obsolete PC hardware and a dated Windows operating system (OS). These old technologies are unable to access web servers or more current Windows-based architectures, such as .Net and OPC. Virtually every HMI/SCADA package has an update for its own software, and some vendors offer software that can update other suppliers' applications. Wonderware, for example, can update old Intellution iFix or FIX32 HMI/SCADA systems.
When upgrading to a new Windows-based control software package, however, it is best to start from scratch with a new PC and current Windows OS. Trying to upgrade an old PC and its OS is frustrating, fraught with problems and not worth either the time or money. At today's prices it's much easier just to buy a whole new computer system.
The situation is likely to be the same with obsolete HMI hardware. Throw it out and install new. For example, thousands of Allen-Bradley PanelView HMI terminals exist in the control world, and many are getting long in the tooth. Rockwell offers an HMI upgrade path featuring its current PanelView Plus terminals.
You can also replace them with software and a PC. InduSoft's (Austin, Texas) Import Tool for PanelBuilder converts existing applications from PanelBuilder 32 to WebStudio, and then runs them on any PC, Panel PC, PDA or embedded display. Not only do the old PanelBuilder HMI displays work the same as before (See Figure 2), the new HMI software provides all the advantages of a modern Windows architecture.
Step Three: Update Control Processors
The day will eventually come when controllers and other equipment must be replaced. "Several years ago, I installed a PLC control system on an old Amsco Autoclave sterilizer," relates Jim Meils of Aventis Behring. "Prior to this, the system used timers and relays. The upgrade worked well for controlling the process, but the mechanical components were old and presented several operational problems because of their age. The lesson is that, even though you upgrade the control system, you need to look at the big picture and determine if the associated mechanical components are capable of sustaining the efficient operation of the machine."
Sometimes old controls just can't cut the mustard any more. Mark Richardson, senior engineering specialist at Hemlock Semiconductor, Hemlock, Mich., puts it more delicately, saying that sometimes new requirements exceed the capability of the old controllers. This is the case with Hemlock's Fischer & Porter DCI 5000 control systems.
"We replace legacy controllers with new controller boards and new I/O boards, but we re-use existing field instruments and terminations, and convert old control programs to current level," he explains. "This method is used when the reliability or control capability of the legacy controllers is inadequate, but the field instrumentation is capable."
When I/O can't keep up because the modules have corroded, or if the I/O network is suffering a high rate of failures, Hemlock replaces it. "We replace legacy distributed I/O with new fieldbus-based I/O modules and communication boards," he says. "We add software needed to address the new I/O modules, but leave the existing control schemes and programs alone."
Back in the 1990s, F&P developed adapters that allowed old DCI 5000 terminal boards to be connected to F&P's new System Six I/O boards. So far, Hemlock has replaced 16 of 18 legacy F&P controllers with "new" 1993 System Six controllers, but kept the existing field I/O.
F&P was acquired by Elsag Bailey in 1994, and Bailey was acquired by ABB in 1999, so the legacy DCI 5000 controls are now supported by ABB.
Updating control processors to a newer generation is a good way to upgrade a system for power or reliability. Wild says CRISP Automation can upgrade any CRISP system from an old DEC PDP-11 or VAX platform to the newer DEC Alpha platform, and soon will be able to upgrade those systems to the new Itanium platform running Open VMS. He can also do this for non-CRISP systems as well. "We can migrate any type of DEC VAX system running Open VMS to run on a DEC Alpha or Intel server, without any application changes," he claims. "We are currently developing a generic OPC server/client product for all VMS users, which will add enhanced connectivity to the many thousands of existing legacy DEC VAX systems."
Wild also claims that he has access to enough replacement DEC computer hardware and I/O boards to support all the legacy CRISP systems that the installed base is still running.
Wonderware's Steve Garbrecht says control engineers can find many listings on Ebay for "new old stock" or used PLC and DCS hardware. "If the online auction environment is not your cup of tea, then there are several companies that specialize in used and refurbished equipment, like Western Process Computers (www.westernprocess.com), located in Phoenix, Arizona, which specializes in refurbished Honeywell DCS hardware," he adds.
Step Four: Migrating to New Technology
So far, we've looked the first three steps of upgrade strategy. Step one, upgrade software, step two upgrade HMIs, and step three, update controller processors and networks. All are relatively easy and inexpensive solutions. It's when we get to step four, replacing controllers, that is where things can start to get expensive. Step four encompasses everything from simply replacing a PLC with a newer model to migrating over to an entirely new system.
PLCs can be one of the easier controllers to upgrade. Schneider Electric, for example, offers its customers its Validatable PLC service. The service provides users operating with prior-generation Modicon PLCs an upgrade path to new Modicon platforms and enables I/O cards installed 30 years ago to be connected to new PLCs. Through the Validatable service Schneider's pharmaceutical and critical batch process customers can upgrade their PLCs without losing FDA 21 CFR Part 11 certification because the system does not have to be re-validated.
Other DCS migrations allow plants to keep legacy I/O. For example, users running old Moore Products APACS+ systems can upgrade to Siemens PCS 7 without having to get rid of old I/O. This may not be as easy as it sounds, however.
Mississippi River Corp. (MRC), a 400 ton/day re-pulping and de-inking plant in Natchez, Miss., installed an APACS+ control system in the early 1990s. The system featured a Mycroadvantage HMI from TA Engineering, which ran under Windows 95.
After 10 years of upgrades, the system became unreliable. Because TA Engineering went out of business, MRC had no choice but to migrate, convert or up
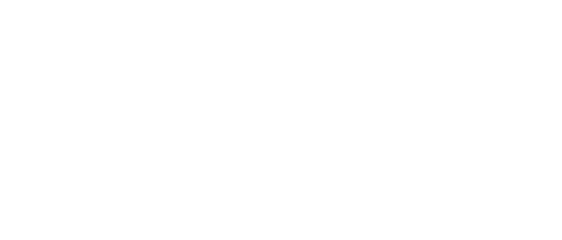
Leaders relevant to this article: