RELATED STORY |
The next generation of smarter valves – Part 1 |
- Increased accuracy, 0.1% to 1% vs. 0.3%-2% for analog.
- Improved stability, about 0.1% compared to 0.175%.
- Wider rangeability (without sacrificing accuracy) up to 50:1 compared to 10:1.
In addition, they are capable of performing multiple functions, self-testing and diagnostics; can be miniaturized, calibrated or adjusted without physical access to the instrument; and can use information that can not be measured or accessed by analog means.
Valve Performance Monitoring
Valve performance is usually monitored by checking valve calibration parameters, such as the zero position and the travel span of the valve. Additional tests can monitor the air pressure in the actuator as a function of stem travel and compare this signature against data that was obtained when the valve was newly installed.
A major deviation from the desired characteristic can be an indication of the valve stuffing box being too tight, the valve stem being corroded, or the actuator spring being damaged. When such conditions evolve, they can cause an increase in the dead band and the dead time of the valve, thereby creating a potential for instability and cycling in the control loop.
This test data can be called up via HART protocol and can be a vital part of the plant’s asset management system. Some believe such data could also be transmitted over a fieldbus to a computer by a digital signal while the valve is actively controlling the process. Others argue that to measure the valve’s performance, one has to provide an artificial offset to the control signal. Therefore, some plant operators are understandably reluctant to use this feature, because they fear that this offset to the control signal would cause too much disturbance to the process. As a result, one typically has to wait until the valve is out of service (process is shut down) in order to perform the functionality tests.
Future Trends and Tasks
Future uses of the intelligent positioner as “data transmitter” will no longer be restricted to monitoring the condition of the valve actuator but will most likely include:
- Monitoring the leakage of the valve’s packing box or bellows using the output of suitably placed pressure sensors, or by “sniffing” the ambient air around the valve stem to detect toxic substances by means of a miniaturized chemical detector.
- Checking for fluid leakage between plug and seat by measuring the sound frequency detected by a sound pressure transducer (located within the valve housing) and comparing that against a known frequency profile.
- Discovering excessive seat leakage by comparing the controller output signal at low flow conditions with the same signal that was measured for the same low flow rate when the valve was new. Excessive leakage would be indicated if less travel (less opening) was required to obtain the same flow as when the valve was new.
An important feature of all positioners is the time they take to either evacuate all the air from the actuator (if the valve is “air-to-open”) or to deliver the maximum air pressure to the actuator (if the valve is “air-to-close”) when the control signal calls for the valve to be closed. When this occurs, to avoid seat leakage the positioner output signal must change rapidly to apply the maximum actuator force to the valve plug.
Some digital positioners also provide memory-embedded data such as the serial number, date purchased, vendor, tag number, valve size, etc. These are all useful for asset management purposes and are especially handy when the original valve serial plate is corroded and has become unreadable.
Future intelligent positioners may be able to receive their control signal via radio transmission. The difficulties with such techniques include reliability, path loss, RF interference, multi-path radio echoes, and the required transmission power. Most of all, these positioners will still require sufficient electrical power to operate their pneumatic and electronic components. Consequently, valve positioners will never be truly “wireless.”
Changing the Valve’s Characteristics
Another common feature of digital positioners is their ability to modify the relationship between the controller’s output signal and the pneumatic output signal to the valve actuator. The effect of this relationship is to alter the valve’s inherent flow characteristic. In addition to “quick opening,” “linear” or “equal percentage,” characteristics can also be user defined and custom programmed.
Such a modification of the valve’s inherent characteristic is similar to placing a mechanical cam in the travel feedback linkage of a pneumatic positioner. This can convert, say, a butterfly valve from linear to equal percentage. The trouble is that the travel vs. flow coefficient (Cv) of a butterfly valve remains linear.
The result is that the signal resolution at low flow becomes very poor because, with an equal percentage output signal at low flows, the valve travel is very small compared to a given signal change. Therefore, in such cases the valve’s dead band becomes high compared to its signal resolution.
Valves Can Also Measure the Flow
A control valve is a variable area flow meter with a variable pressure drop. Just as the float position in a rotameter (a constant ΔP flowmeter) can indicate the flow, the stem position of a control valve can do the same if the ΔP can be detected. Naturally, in order to do this, accurate knowledge of the valve characteristics and the process properties of the flowing fluid must be provided.
Smart valves can measure the flow through the valve by solving the appropriate valve sizing equation for flow. For example, for turbulent, non-choked liquids, flow (q) can be obtained from a formula (click the Download Now button below for a .pdf version of this formula) if the valve capacity coefficient (Cv), the piping geometry coefficient (Fp), the liquid specific gravity (Gf) and pressure difference (ΔP) across the valve are known. (For equations to calculate the piping coefficients or for equations to be used when the process fluid is a gas or a choked liquid, refer to the 2nd Volume of the Instrument Engineer’s Handbook.
For smart valves of the future to accurately measure their own flow, they must be provided with sufficient intelligence to identify the sizing equation that is applicable. Therefore, they will have to be able to detect laminar flow condition in viscous, choking conditions in cavitating liquid or sonic flow in gas flow applications. Naturally, the other requirement is to be able to accurately measure the variables that are required for solving the applicable equations. The required measurements include valve stem position, inlet, outlet and vena contracta pressures, flowing temperature, etc.
Yet, the potential advantages of such smart valves much outweigh the required investment of time and money. The savings include the elimination of both the initial cost of purchasing and installing, and the energy cost of operating, a separate flow sensor. An added advantage can be the increased rangeability of the flow measurement obtained from the valve. This is because the rangeability of traditional flow detectors is usually 3:1 to 10:1, while control valves can provide rangeabilities of 25:1 to over 100:1 because of their variable area orifices.
Self Diagnostics and Control
If the sensors of the intelligent control valve are connected to a PID chip within the valve positioner, the smart valve becomes a complete local control loop. In that case, the operator’s displays need to be provided in a location from which the operator can conveniently reconfigure the control loop or recalibrate the valve as well as to adjust the limits of its travel.
Smart valves can provide improved maintenance through self-diagnostics. If the proper intelligence is provided, the valve can compare its own behavior with its past performance. When the same conditions result in different valve openings, it can conclude, for example, that packing lubrication is needed or that the valve is getting plugged. When the conclusion of the diagnosis is that the stem is sticking, or that the trim is worn (or any other changes that might warrant maintenance), the intelligent valve can automatically request and schedule its own maintenance.
REFERENCES
1. Baumann,Hans D., “Intelligent Valves, Positioners, Accessories,” Instrument Engineers’ Handbook, Volume 2, 4th edition, CRC Press, 2005.
2. Schneider, Hans-Josef, “Digital Feldgeraete: Vorteile, Probleme und Anforderungen aus Anwendersicht,” Praxis, atp Automatisierungstechnische Praxis, April (1995), pp. 50-54.
About the Author |
Click the Download Now button below for a .pdf version of the formula referred to in this article.
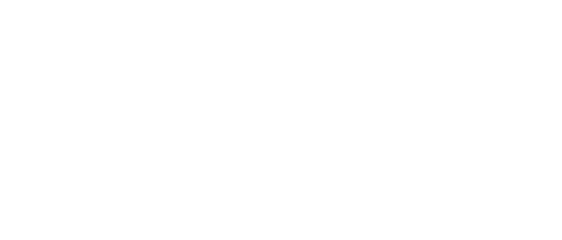
Leaders relevant to this article: