By Greg McMillan and Stan Weiner, PEStan: We had a reply to the September puzzler, ĀYou CanĀt Drop a Control Valve on Him,Ā from Ralph Quigley that shows considerable practical experience and insight as to why the plant instrument engineer said the control schemes and instruments successfully used at other locations would not work in his plant. Ralph: The plant instrument engineer's answer is correct. The control schemes will probably not work in his plant. The controls from the successful plants have proven that your control logic is valid, so there are two reasons that would keep the "next unit" from operating as well:Ā
- There is something at the new site that makes your team's logic invalid, orĀ
- The plant instrument engineer will not let it be successful.Ā
Get your spouse their very own copy at www.isa.org/books-- ED.
Greg: We also had an excellent summary from Hunter Vegas on top batch control opportunities, which in response was to the October puzzler, ĀThe Case of the Batch Unicycle.ĀHunter: At my company, we do a great deal of batch automation for a wide variety of industries. I would say some of our biggest cycle time reductions have come from:Ā
Greg: We also had an excellent summary from Hunter Vegas on top batch control opportunities, which in response was to the October puzzler, ĀThe Case of the Batch Unicycle.ĀHunter: At my company, we do a great deal of batch automation for a wide variety of industries. I would say some of our biggest cycle time reductions have come from:Ā
- Automating the process and moving along material charges and the batch processing without operator intervention. As a result, the batch doesn't have to wait around for operator breaks, lunches, coffee brewing, arguments over weekend football games, etc., etc.
- Starting batch heat up after a portion of a material charge is completed. If you need to raise a batch temperature prior to further processing or additional material charge, you can often get a 'jump' on the heatup by starting heating once you have charged enough material to create a decent thermal mass.Ā
- Reduced rework through automation. Despite what you may think every operator runs a batch differently. Batch automation greatly reduces this variability, and lets you iron out and streamline your process. Most often the best cycle time and quality improvements were obtained within a few months after the process was automated.
The process lage trend in the November Puzzler was increased from 5 seconds to 50 seconds, and the controller reset time was decreased from 20 seconds to 5 seconds.
This Month's Puzzler:
Greg McMillanandStan Weiner, PEbring their wits and more than 66 years of process control experience to bear on your questions, comments, and problems. TheyĀre accompanied in this edition by honorary columnist Hunter Vegas.
This Month's Puzzler:
Valve needs all the trimmings?
Why did Stan include four sets of different-sized trim when ordering a control valve with a Cv less than 0.1?
Send an e-mail with your answer to The Puzzler, CONTROL questions, or comments to [email protected].
Ā About the Authors |
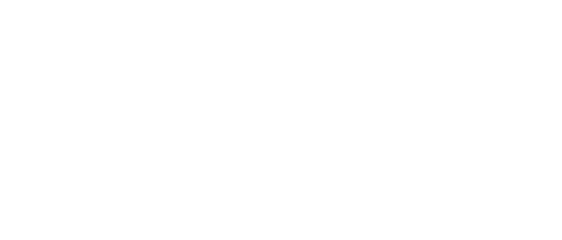
Leaders relevant to this article: