āAsk the Expertsā is moderated by noted process control authority BĆ©la LiptĆ”k. In this column, he and other experienced process control engineers welcome questions concerning process measurement, control and optimization. If you would like to be on our team of āexperts,ā please send a resume to [email protected].
Q: I have a question on the split-range concept. I normally see split-range control designs of 0%-50% and 50%-100% OP (in percentages) from the controller. My question is what determines these ranges? Why not use 0%-60% and 60%-100% ? What is normally the deciding factor?
Nkanyezi Mqadi
Sasol Technology
A: We use multiple valves in applications where automatic switching from cooling to heating (c/h) is involved, and when the rangeability requirement of the process exceeds the range of a single valve, such as pH and many others. The main difference is that in the c/h applications, both valves are closed at the time of switching, and the process gain also abruptly changes, while in the rangeability application, one valve is always open, and the process gain usually does not experience an abrupt change as a result of valve switching.
The goal in all applications is that the loop gain remains constant while switching valves. Assuming, for example, you sequence two linear valves on a 50%/50% split range, and the Cv of the large one is 10 times that of the small one, the loop gain would change by a factor of 10 as you cross the 50% point. This being unacceptable, you could operate the small valve from 0% to 10%, and the large valve from 10% to 100% of controller output, but that is not very convenient when calibrating the positioners.
The sequencing of equal-percentage valves is done as follows: If the small valve has a Cv of 10 and a rangeability of 50:1, its minimum Cv would be 10/50 = 0.2.Ā A line drawn on semi-logarithmic coordinates connecting Cv(Kv) 100 and 0.2 appears in Figure 1. Observe that the Cv of 10 of the small valve falls slightly above the midscale of the controller output (to about 65%), providing a much more favorable span for the calibration of the positioner than did the splitting of the linear valves.
Ā In order to have the two valves act as one without disturbing the smooth equal-percentage characteristics at the points of switching, only one valve must be open at any one time. Therefore the large valve must be prevented from operating at low flows, because in its nearly closed position, its characteristic is not equal-percentage.
As shown in Figure 1, the small valve alone is manipulated until the controller output reaches the value corresponding to its full opening. At this point (if the valves are pneumatic) a pressure switch energizes both three-way solenoid valves, venting the small valve and opening the large valve to the same flow that the small one had been delivering. Switching takes place in one second or less, adequate for all but the fastest control loops.
Figure 1. A method to minimize upsetting the control loop when switching equal percentage values.
When the controller output falls to the point of minimum flow allowed for the larger valve (35%), the solenoids return to their original positions. Thus the switch has a differential gap adjusted to equal the overlap between valve positioners (30%). The range of the positioner for the large valve is found by locating its minimum Cv on Figure 1. A rangeability of 50 would give a minimum Cv of 2.
This same approach can be used to sequence three or more valves. If linear characteristics are required, one should insert a 10:1 multiplier relay in the controller signal to the small valve, so that a 0% to 10% controller output will result in a 0% to 100 % signal to the small valve.
In some applications, including pH, better response can be provided by the use of a āfloatingā valve position controller, which slowly moves the larger valve while keeping the smaller one near its 50% opening. This way, the small valve provides sensitivity and fast response to the loop within its capacity. The large valve is a sort of automatic bypass, which sets the capacity and has a limited frequency response.
BƩla LiptƔk
A: The selection of the ranges for the valves in split-range operation should be based on keeping the loop gain constant. The closed loop should behave the same whichever valve is being manipulated by the controller in response to the process load. This will vary with the process and with the size of the valves. In some cases, the gains for the individual operating conditions can be calculated; in other cases, a test may be needed. Ultimately, the loop behavior should be the same for both valvesāif it is not, the split point should be adjusted by recalibrating the valve positioners to produce the same behavior.
Greg Shinskey
Process Control Consultant
A: This is a good questionāone that should be asked more often.
Consider a typical heating-cooling application. Suppose a fail-open cold water valve is fully open at 0% and closed at 50%. A fail-closed hot water valve is closed at 50% and open at 100%. Then suppose it is discovered that the sensitivity of temperature to changes in the HW valve position is twice as much as the sensitivity of temperature to changes in CW valve position. In other words, the process gain is twice as high on the heating side as on the cooling side. Then a better split would be 0% to 33% cooling, and 33% to 100% heating. That would make the process gain uniform over the entire range of controller output.
It probably is never a simple as this. Just recognizing the process gain is higher when heating than it is when cooling leads one to shift the split point to the left. How much is probably an experimental decision.
One other point: In the heating-cooling application I described, when the controller output is at the split point, both valves are closed, which is their worst controllable point. I would tend to overlap the operating range slightly; say 0% to 55% and 45% to 100% (if I am splitting at 50%), so that within the overlap range, both valves are slightly open. This may require slightly more energy consumption to gain a control improvement. How much to overlap, and whether the control improvement is worth the excess energy cost is a local decision.
Harold L. Wade
Wade Associates, Inc.
A: The ārightā answer depends on what is needed and the details of the application. Below are three simple cases. Simple calculations of flows and process needs should aid in making the design decision.
CO is controller output in percentages. V1 is the first valve stem position in percentages. V2 is the second valve position in percentages.
Case 1. Very simple for easy heating and cooling. If these control the flow through something like a reactor jacket, the control dynamics will change greatly, depending on CO, and thus might not be acceptable. If there is a circulating pump on the jacket, then the jacket dynamics change is reduced. Note the serious change in control gain as you approach the 50% point where flow is nominally zero. This calibration is often used for H&V applications. Heating and cooling energy use is minimized when the CO is 50%.
Case 2. Total flow stays more or less constant. This works for applications such as jacket temperature control without a circulating pump. Heating and cooling energy may be lost as part of the cost of good control.
Case 3. The compromise case with overlap in the valve flows to suit the issues. A predetermined minimum flow exists even at CO of 50%
Consider that the relationship between the valve positioner input signal and the inherent valve coefficient may not be linear, and this will also affect the CO versus flow and is part of the control consideration.
Cullen Langford
PResident, Cullen Langford Inc.Ā Ā
A: Split-range control is often used when there is a need to shift or transition the manipulated variable in order to affect the controlled variable over its expected operating range. For example, in the control of jet velocity out of a paper machine headbox over the entire speed range of the machine, it is often necessary to shift from vacuum to pressurization in the vapor space of the headbox, so the output from a headbox pressure or level controller may be split to two different three-way control valves depending upon whether the operation is in vacuum range (exhausting air/vapor) or pressurization (pulling in air).
Another common example is pH control, where either an acid or base reagent may need to be added, depending upon design pH setpoint and expected pH range. In this case, there may be two valves or two variable-speed or variable-stroke metering pumps.
Here are a few points to consider:
- There is no reason you can't use other splits, such as 0% to 60% or 60% to 100%. In the case of control valves, setting up the positioners or I/Ps appropriately can usually get the stroke and direction desired out of the valve for a given controller output, e.g., 50% to 100% output to 0% to 100% valve stroke. The same is true for most variable-speed drives.
- The physical system should be designed so the split does not occur at a normal operating point, since there is more likelihood of a discontinuity or upset in control at the transition.
- If the gains of the multiple manipulated variables (e.g., vacuum, pressure valve; base, acid pumps) are different, selection of a split somewhere other than right in the middle could be a strategy for helping to linearize the process gain that the controller sees. In this case, assign a larger portion of the controller output range to the manipulated variable with the larger gain, and vice versa.
This is likely not a complete answer, but I hope it is somewhat helpful.
R. H. (Rick) Meeker, Jr., PE
Reliable Power and Controls Corp./
Process Control Solutions, Inc.
A: As commonly happens in control, certain methods of split-range design are holdovers from the past limitations of the control abilities of the hardware. When pneumatics were used, the air tubes splitting the signal were equal diameter, hence, splitting the signal equally.
The 0% to 50%/ 50% to 100% was commonly used in heating/cooling applications using a common medium so an equally split signal may have made sense.
However, it is more likely that the media for heating and cooling are very different.
For example, in plastics extrusion, I've seen heating as an electric heater and cooling as chilled water. Or in reactor control, heating is a fluid heated by a fired heater, and cooling is water chilled with a propane cooler or chilled Syltherm or the like.
The point is that the process dynamics from the heat range is different from the cool range, so the control from a temperature PID is unstable in one region and sluggish in another. Some type of adaptive tuning is needed where the tuning constants are changed, depending upon region of control. Control through the transition then becomes difficult.
One way to control the dynamics across the region is to attempt to linearize the response by translating the temperature you want to control to its basic form, which is actually heat applied. Thus what you are attempting is to linearize across the entire heat range.
If you can describe the medium in terms of BTUs instead of temperature, then maybe you are able to linearize the response through the heating and cooling ranges. Of course, valve dynamics may be incorporated here too. This may then give, as you note, a 0% to 60% / 60% to 100% split instead that would provide for a better control. One application I did was 0% to 18%, 18% to 100%.
Other novel approaches include an overlap or gap in order to control moving through a transition. I've seen 0% to 49%/51% to 100% as a gap control (but here a problem arises if the control wants to live around the 49% to 51% space, which is undesirable). And I've seen 0% to 51%, 49% to 100%, in which both mediums are active (and energy wasteful)
The essence of the solution is linearizing on a parameter common to the range of both outputs you are trying to control. If you can, the split range will probably vary from the standard 0% to 50%/ 50% to 100%.Ā If not, well, adaptive techniques are still in play.
Bruce Jensen
Manager, Systems Technical Solutions Support
Yokogawa Corporation of America
A: There is no good reason at all, would be my reply. If you are trying to maintain constant gain in the control loop, the gain of each valve should be the same. If they are the same size and linear, a 50% split makes sense, but they usually are not.Ā BUT I would also say that I endeavor to avoid designs using split-range outputs.
The better approach is to get two analog outputs from the DCS. You can set these up with separate A/M access and with overlap or underlap between the settings. Much more flexible, and both positioners are calibrated for 0% to 100%, avoiding confusion in maintenance.
Ian H. Gibson
Engineering Consultant
Process, Control and Safety Systems
A:Ā I think the deciding factor is the effect on loop gain, considering the multiplication factor on the gain of the final control device. If you drive a final device over its full range with a reduced input (controller output), you have an increase. I think the reason splits are often set for 50% is simply to equalize this multiplying factor for each control device and give each an equal amount of "working room" in the controller's output range.
Obviously, you could set the split to/for some other percentage, which might be useful in some situations, but the unequal gain factor to the final control elements would have to be considered, and some devices can be harder to calibrate to a greatly reduced input.
Al Pawlowski, PE
Almont Engineering
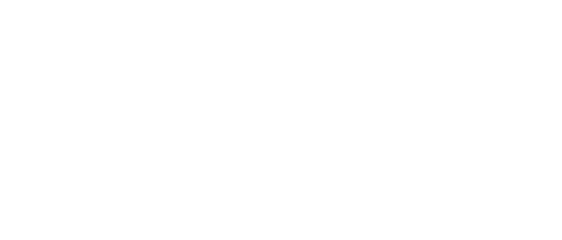
Leaders relevant to this article: