Check out ControlGlobal.com on Google+
A few years ago, Chevron Energy Technology decided it needed to make an assessment of cost and schedule risks. The results of the study were not positive. Chevron is essentially broken down into two businesses: upstream and downstream. The study found that the downstream business was doing pretty well, but it had long schedules and high costs. For the upstream business, the situation was worse.The large, multinational oil and gas company set out to make a change.
The results of the study were not a big surprise—it's why Chevron did it in the first place; to confirm what was already suspected, said Roy Corbett, I&C engineer for the project support team tasked with turning things around. To put things on the right track, Chevron partnered with Yokogawa as global main automation contractor (MAC) to put together a world-class major capital project program.
Corbett, who moved over to Chevron from Yokogawa, helped to develop and manage a MAC toolkit for the alliance. He and Russ Griffith, manager of the project support team, presented the initiative's progress this week at the Yokogawa Users Group Conference in New Orleans. "We were looking to provide a guide to how to implement process automation systems with Chevron," Corbett explained. "We've had success and some stumbles. It's still a learning process for us."
Global Standardization
"You certainly don’t have to take all 154." In familiarizing Chevron engineering teams around the world with the extensive MAC toolkit, Roy Corbett stresses the modular applicability of the tools included.
A key objective of the MAC toolkit, of course, is to manage project cost and schedule risks, which have improved already through the project, Corbett said. Also important is to ensure standardization across company divisions and locations by promoting the MAC toolkit across all projects. Although the project team can't tell other divisions what to do or how to do it, Corbett emphasized, they can try to promote the benefits of following the MAC guidelines.With tens of thousands of employees around the world, it is important for Chevron to standardize globally. "We have billions and billions of dollars of projects every year," Griffith noted. "Some of those are executed in several places. We might have some fabrication done in China; we could have fabrication and testing in Korea. Wherever a project is being done, it should be in a similar style."
Other team objectives include executing projects in a safe, efficient way that ensures reliable operations; building a business relationship based on performance driven by continuous improvement; and creating a true lifecycle program that provides goods and services through all project phases.
However, the partnership remains flexible in design and execution strategies for project-specific requirements. As Corbett pointed out, Chevron's operations in Kazakhstan are very different from operations in the Gulf of Mexico. "It needs that flexibility built in," he said. "[The toolkit] can be seen as being quite large and ornery because it's all-encompassing."
Modular Approach Meets Scalable Needs
That all-encompassing MAC toolkit is a comprehensive library for project execution and technical guidance. The technical guidance alone consists of 12 volumes at this point, with 154 documents designed to help projects succeed. That can seem daunting to anyone approaching it for the first time, but it doesn't have to be.
Corbett explained, "When I do my training, I emphasize, 'If you only need two documents, only take two. You certainly don't have to take all 154.'" In one training session, an employee told Corbett he was lacking only a communications plan for his project. Corbett handed him one document to get the job done, and that one deliverable made his training time worthwhile.
In general, the MAC toolkit encompasses templates for standardized engineering, design and implementation; an optimized project schedule; detailed project control, planning and execution; definitions of roles and responsibilities; and best practices and lessons learned. It minimizes the diversity of the system, building on Chevron specification requirements to reduce design and execution risk.
Though there's always some customization assumed, the toolkit is designed to get projects to 80% of where they need to be very quickly, Corbett said. Solutions are based on Yokogawa products that meet Chevron guidance. Through the project, the alignment between Chevron and Yokogawa has grown very quickly, he added.
Feedback from Users
"We're really coming to the end of the first phase of leveraging the MAC toolkit," Corbett said. "Now we're going through that first major recycle of learning lessons and streamlining it. We're getting lots of feedback from users."
The MAC toolkit was developed locally, leveraging some major projects to get it up and running. "There have been some great successes; there've been some failures; and there's been some stuff in between," Corbett confided. "Hopefully we will mature this toolkit more and more over the next several years."
The MAC program expertise is concentrated in Houston, but the team has ongoing training around the world, running side-by-side through the Chevron and Yokogawa organizations. "It's got some good branding now," Corbett said. "The goal over the next year or two is to promote it, to achieve the goal that we have of standardization."
The team's vision is to successfully demonstrate the execution of global major capitol projects using the MAC program strategies, template and tools. "We've got to show that there are benefits in using it," Corbett said. Cost and schedule were two major drivers to starting the program, but the team wants to improve quality and safety expectations as well. They also want to show improvements in project execution, quality of engineering and compliance to Chevron requirements; and to capture lessons learned and feed them back into the governance process for continuous improvement.
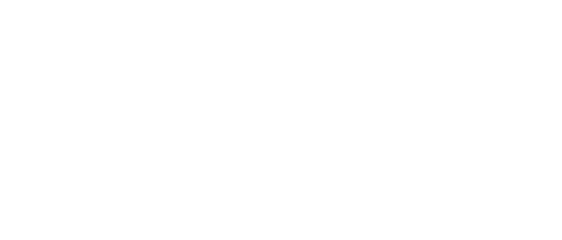
Leaders relevant to this article: