To his credit, the Rockwell Automation commercial competency developer lived up to his title. Schriver delivered his presentation as smooth as silk. And the technical glitches only served to reinforce his message – things go wrong in any complex process; the challenge is to mitigate the fallout.
The method to that mitigation in the manufacturing realm is smart devices, or more accurately, the strategic, connected deployment of smart devices. “There is no question that a smart, connected system using intelligent devices is easier to operate and maintain, and will have higher uptimes,” summarized Schriver. “All of the situations that would have required downtime, troubleshooting and other efforts can either be prevented or, in the event of an interruption, we can move more quickly that we were previously able to.”
“Situations that would have required downtime, troubleshooting and other efforts can either be prevented or, in the event of an interruption, we can move more quickly,” said Brian Schriver at Rockwell Automation TechED this week in Orlando.
Schriver credits enterprises like Apple and Google for prompting changes in the industrial arena. “What they have done with smart devices raises the bar for us,” he said. “My 18-month-old was able to play videos on my phone, while we as an industry have typically produced products that required an engineering degree to use. This was just accepted as the way things were. Now we’re making a concerted effort to make our products easier to use.”Working smarter, working easier – not harder
The presentation summary promised to give attendees a look “under the hood” of smart “edge” devices, and the presenter delivered just that – a video feed on one screen broadcast Schriver manipulating device controls as he described the processes for each.
Schriver repeatedly referenced sensors as the best examples of smart devices on the factory floor. Whereas sensors historically communicated just one message (“This part of the process is working”), the modern, smart sensor performs that basic task while also providing real-time updates on its own performance (“I am not functioning optimally”), analysis of its own condition (“I am overheating”), and a projection of its own lifespan (“I need to be replaced soon”). “This information enables predictive maintenance, rather than reactive maintenance,” the presenter said.
A key component of Schriver’s presentation was using IO-Link point-to-point serial-communication protocol to communicate with sensors and/or actuators, and the troubleshooting advantages that tool provides. “We have just had to live with spending hours troubleshooting to learn why a sensor stopped working,” he said. “To get advanced notice of that built into a control system is a really powerful thing.”
The application of (and benefits from) smart devices was highlighted throughout the presentation, as was Schriver’s simple description of what, exactly, makes a device smart. “To me, a smart device has two aspects. One – can I get contextual, useful information out of it? Two – is it easy to use? A smart device should just work, without me having to do a whole lot of things to it to make it work.”
Tell that to the slide projector.
Latest from Asset Management
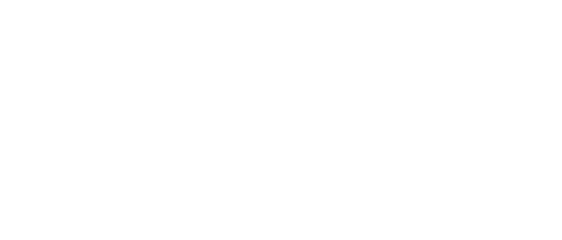
Leaders relevant to this article: