Many industrial networks solutions built on IEEE 802.x Ethernet standards are available to vendors and end users. Even as vanilla Ethernet evolves with the support of organizations such as the Ethernet Alliance, many Ethernet-based standards—or more accurately, Ethernet-based industrial networking protocols—have emerged. They help developers use commercial IT economies of scale, and future-proof networks as Industrie 4.0 and the Industrial Internet of Things (IIoT) redefine smart manufacturing across industry lines.
Industrial Ethernet solutions serve diverse needs, and speeds, which typically range from 10 Mbit/s (megabits per second) to 1 gigabit per second (a.k.a. Gigabit Ethernet), while 100 Mbit/s is the most common speed for communicating control data from field to host devices.
Some solutions are tailored to process applications, while others are best known in the discrete world. Generally, it’s not the technology, but market factors that give each solution its momentum. The key is vendor support, says Harry Forbes, research director with ARC Advisory Group. “If the solution is widely used in the end user’s vertical industry, and it's also an important part of their vendors’ offering, then they're much more likely to adopt it," explains Forbes. "They don’t want to be the only plant in their industry or region that's running their process with a particular platform.”
As a result, process industry professionals would do well to become familiar with developments from several industrial Ethernet consortia, including those that cross industry lines.
HART-IP, Foundation Fieldbus HSE
As the digital transformation of IIoT and Industrie 4.0 emerges, “End users are increasingly interested in gathering diagnostic data from their HART instruments," says Paul Sereiko, marketing director, FieldComm Group, which administers the HART and Foundation Fieldbus protocols. "HART-IP multiplexers, RTUs and WirelessHART gateways provide a simple, easy way to capture this information.”
The most recent Ethernet-enabled developments at FieldComm Group include HART-Internet protocol (IP). Similar to the hybrid analog-digital HART communication protocol, HART-IP communicates between intelligent field instruments and host systems, such as DCSs, asset management, safety and SCADA systems, and mobile devices from laptops to handheld configurators. The application layer for HART-IP is the same for all HART protocol-enabled field devices, but employs Ethernet physical media and a standard TCP/IP protocol in a solution with speeds from 10 Mbit/s to 1 Gbit/s. Therefore, it eliminates the time and errors of data mapping, for example with Modbus RTU, and simplifies setup and using a backhaul network for WirelessHART gateways, wired HART multiplexers and remote I/O. Security continues to evolve for HART-IP (Figure 1).
[sidebar id =1]
Meanwhile, for Foundation Fieldbus users, Foundation Fieldbus High-Speed Ethernet (HSE) specification has been available since the early 2000s, is standardized as IEC 61158, and uses Ethernet to connect plant communications from fieldbus to higher-level devices such as controllers and remote I/O using a 100 Mbit/s solution tailored for process plants.
In addition, FieldComm serves as clearinghouse for Field Device Integration (FDI), which allows integrating competing electronic device description language (EDDL) and field device tool (FDT) device data standards into one platform for greater interoperability, adding value to higher-level Ethernet solutions.
[sidebar id =2]
Profinet proves pervasive
Mike Bowne, executive director of PI North America, says more than 3 million Profinet devices went to market in 2015—a 30% increase over the previous year. “And 2016 is on pace to beat that again,” he adds. The latest news is that a new, intrinsically safe (IS) version of PI's Profinet industrial Ethernet protocol is being developed that will be based on Advanced Physical Layer (APL) technology. It will employ a two-wire connection with limited current/voltage to be IS, while still providing power and segments longer than Ethernet’s present, 100-meter wired limit (Figure 2).
In related news, work on Profinet includes Process Application (PA) Profile 3.02, which eases replacement of aging instruments by eliminating reconfiguration of the DCS or device by automatically assuming the parameters of the (older) device they’re replacing. A pending PA Profile 4.0 will be released in the near future, Bowne adds, “with further developments for process control users.”
[sidebar id =3]
Profinet can connect to devices, controllers, I/O and field devices, the latter through the use of proxies to access data from IS fieldbuses such as Profibus PA. “In these hazardous environments, Profibus PA cables can land directly on an instrument; Ethernet cables can't—yet,” explains Bowne. This is partly due to PI North America’s support of FDI technology.
While work continues to bring Ethernet-based solutions to the field, Bowne says inexpensive sensors and actuators without a Profinet interface can employ the point-to-point communication IO-Link standard (IEC 61131-9), which uses the same, common, three-wire cable that many sensors already use.
EtherNet/IP evolves
ODVA, formerly the Open DeviceNet Vendors Association, was founded in 1995, and evolved to support EtherNet/IP. It adapts the Ethernet standards for TCP/UDP/IP to its own Common Industrial Protocol (CIP), which includes device profiles, objects and services for real-time control of production applications for process and discrete/factory automation. ODVA publishes new editions of its specification twice yearly. The latest news was the December publication of its cybersecurity services, CIP Security, which provide security between two EtherNet/IP devices with encryption and authentication capabilities.
“When combined with best practices for defense-in-depth mechanisms to enhance cybersecurity, CIP Security allows users to reduce their risk from cybersecurity threats to their production processes,” says Katherine Voss, president and executive director, ODVA.
Voss cites a 2016 report from analyst firm IHS Markit showing EtherNet/IP led industrial Ethernet solutions with a nearly 25% share of new nodes shipped in 2015. This news may chip away at process plant users’ traditional reluctance to change, and help them consider Ethernet to “accelerate the time clock for achieving 100% digitization, and work together to refine requirements for an Ethernet communication system for the process industry.”
This possibility is demonstrated by a new partnership between ODVA and NAMUR, the international process industries automation association, developing an EtherNet/IP installation at the process automation lab at Industriepark Höchstin Frankfurt am Main, Germany, to include field devices, controls and infrastructure from Cisco Systems, Endress+Hauser, Rockwell Automation, Schneider Electric and other ODVA members.
Modbus/TCP open and free
The Modbus Organization, like its Modbus/TCP protocol, is unlike other standards organizations “because Modbus is an open protocol and free to use,” says Lenore Tracey, executive director. Introduced in 1979 by Modicon (now Schneider Electric), Modbus is available free of licensing fees for users to adopt and adapt. While there’s no requirement for testing and conformance, firms taking advantage of the optional Modbus Conformance Testing Program can provide independent verification of compliance with Modbus specifications.
The organization’s main role is educational, with support for members at its website, which offers newsletters highlighting member activities (and product releases), discussion forums and a new Technical Resource Page for developers and users. It hosts links to specifications, a TCP toolkit, conformance testing details, and an offsite resources list.
The Modbus Organization's latest activities include work on security issues and a pending announcement of a guideline for developing Foundation Fieldbus and Modbus gateways to WirelessHART.
Ethernet Powerlink and safety
Ethernet Powerlink was developed by B&R Industrial Automation, and launched with the 2003 formation of the Ethernet Powerlink Standardization Group (EPSG). Based on Ethernet and CANopen standards, it offers speeds up to 1 Gbit/s, or Gigabit Ethernet.
It supports determinism with an isochronous phase, and adds openSafety integrated safety that eliminates added cabling and hardware safety functions. This provides functional safety conformance with IEC 61508 and SIL 3 functional safety standards. Efficient safety communication minimizes shutdowns, offering the potential to enhance plant and communication efficiency.
Among the latest news from EPSG is “Industrial Ethernet Facts,", a 40-page PDF comparing Profinet, Ethernet Powerlink, EtherNet/IP, EtherCAT and Sercos III (primarily for servo applications). It also covers Profisafe and openSafety, and offers insight on OPC UA in relation to industrial Ethernet.
EPSG members lean toward discrete automation, including B&R along with ABB Robotics, Yaskawa and Festo, but participants familiar to process users include Schneider Electric, Phoenix Contact, Baldor and Pepperl+Fuchs.
Also, EPSG has been an active partner with the OPC Foundation, demonstrating at industry expos how “interface-free" OPC UA-based solutions provide platform-independent communication for Ethernet Powerlink networks.
CC-Link IE emerges
Like other industrial Ethernet developers, the CC-Link Partner Association (CLPA) offers varieties of its protocol: CC-Link, CC-Link IE and a new specification, CC-Link IE Field, which John Wozniak, P.E. and manager of CLPA in the Americas, calls “the world’s first and only open gigabit Ethernet Industrial Automation field network.” This 1 Gbit/s network has separate bands for cyclic communication for real-time data and transient messaging for diagnostics and other data.
The latest CC-Link news comes in the form of partnerships. Woszniak says CLPA prefers cooperation, and welcomes collaboration with all organizations including the FieldComm Group. In November, CLPA completed a yearlong collaboration with Profinet on a specification that enables transparent, bidirectional communication between CC-Link IE and Profinet. OPC is beginning similar cooperative work within its OPC Foundation to create an open specification for OPC UA as “the path that will allow communications from devices to plant information management systems such as MES and up to office type TCP-IP networks,” says Wozniak.
Progress also continues on security to allow “anyone with a TCP-IP or UDP-IP network, including those with legacy RS networks, to access that token network of CC-Link,” adds Woszniak.
[sidebar id =4]
EtherCAT crosses industry lines
The EtherCAT Technology Group (ETG), with more than 4,000 members, “is the world's largest fieldbus organization,” says Joey Stubbs, North American representative of ETG.
EtherCAT wasn’t developed for any particular industry, but for ease of use, low cost and openness, which led to its use in many fields, Stubbs says. “Though EtherCAT systems found their way into many process applications, several ETG members and vendors introduced added devices that meet the environmental certifications of some process industries.”
EtherCAT has been used for digital I/O, analog I/O, temperature, pressure, servo drives, stepper drives, condition monitoring, data acquisition, robotics, HMI and other applications. When used with OPC UA, EtherCAT provides a real-time network for machine and plant control, and OPC UA provides a platform for data transfer up to MES/ERP systems and into the cloud.
[sidebar id =5]
Latest from Industrial Networks
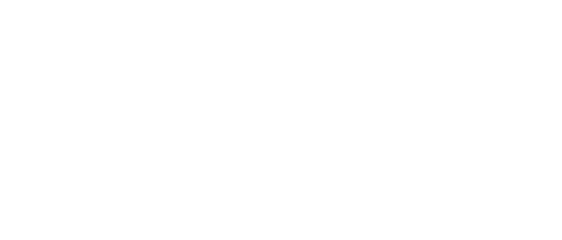
Leaders relevant to this article: